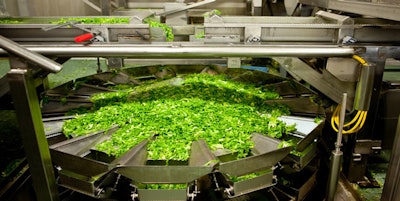
Parsec Automation Corp.
Phone: +1 714 996-5302
Fax: +1 714 996-1845
www.parsec-corp.com
© Parsec Automation Corp 2014. All rights reserved. Parsec Automation Corp., Parsec logo, and Parsec product names are trademarks of
Parsec Automation Corp. References to other companies and their products use trademarks owned by the respective companies and are
for reference purposes only.
EFFECTIVELY IMPROVE OPERATIONAL EFFICIENCY
FOR FOOD AND BEVERAGE MANUFACTURERS
Delivering Significant ROI with TrakSYS™
Effectively Improve Operational Efficiency Page 1
All print and electronic rights are the property of Parsec Automation Corp. © 2014
Abstract
The predominance of sophisticated control networks has set the stage for some revolutionary advances
in the utilization of detailed plant floor information that can drive the next round of food and beverage
manufacturing improvements. Optimizing Asset Utilization in order to maximize the productive capacity
of existing manufacturing systems—before investing in large scale capacity additions—is the key to
continued reduction in per unit manufacturing costs.
With real-time operations and performance management software such as TrakSYS™ from Parsec
Automation Corp., it is now possible to automatically collect and analyze detailed real-time and historical
information, such as Overall Equipment Effectiveness (OEE), to continuously optimize the performance of
all sources of manufacturing processes. In this operational efficiency guide, the author will show how real-
time data collection tools, coupled with web-based delivery of critical manufacturing information related
to downtimes and efficiencies, are allowing users of these tools to take the next step in their evolution as
World Class manufacturers.
Effectively Improve Operational Efficiency Page 2
All print and electronic rights are the property of Parsec Automation Corp. © 2014
Introduction
The primary internal business objectives of many of today’s high volume manufacturers—whether they
are producing pharmaceuticals, food/beverage products, electronics, or other products—have become
remarkably similar. Repeatedly, business managers tell us that excellent product quality is presumed,
while on-time delivery and a high level of customer service are also essential. The real differentiator
between competing manufacturers that helps most to grow earnings is the ability to engineer and manage
a process that results in the lowest possible unit cost when all factors are taken into account.
Global competition and the quest for ever-increasing corporate profits dictate that manufacturing
companies must constantly strive to produce at an ever lower cost. Given that many companies have
already picked the low-hanging fruit related to business systems and supply chain, the author contends
that a relatively untapped major area of opportunity lies directly on the plant floor itself: Asset utilization
and production efficiency. Why? Look at the cost of owning and operating a production line: Capital
equipment (depreciation), operators, maintenance technicians, supervisors, floor space, utilities, spare
parts; the value of production time for high-volume lines certainly runs in the thousands of dollars per
hour. Yet the vast majority of plant managers do not have a clear picture of their true operational
efficiency, and they certainly don’t have the data that is required to drive continual incremental
improvement. TPM (Total Productive Maintenance), Continuous Improvement (“Kaizen”), and measures
such as OEE (Overall Equipment Effectiveness) are well recognized as providing high value, however, most
out-of-the-box solutions that allow manufacturers to cost-effectively collect the accurate data required
to support TPM and OEE don’t provide simplified reports of this critical data that is needed for operational
improvement. Add to this, these out-of-the-box solutions typically require an extensive implementation
process in both time and money, thus the cost to improve operational efficiency can dramatically increase.
Therefore, a straightforward means of automatically collecting and analyzing the detailed real-time and
historical information that is required to continuously optimize all sources of your food and beverage
manufacturing losses will provide tremendous value. This value will be derived:
▪ By increasing output per shift and OEE for existing lines.
▪ When capacity is a constraint: Allowing large capital investments to be deferred, as well as deferring
all the long-term operating costs associated with a new line. High volume production lines typically
cost $1-10 million to build and can cost thousands of dollars per hour to operate.
▪ When capacity is not a constraint: Allowing for a reduction in overtime or in the number of shifts
resulting in labor and energy savings.
▪ When new lines must be added: Reducing the start-up time and associated costs by providing accurate
and specific data related to the frequency and duration of faults caused by each system in the line.
With this, problems can be rapidly identified and resolved.
▪ By minimizing overall production cost per unit by continually monitoring and improving the process.
Effectively Improve Operational Efficiency Page 3
All print and electronic rights are the property of Parsec Automation Corp. © 2014
The True Character of Losses
In order to maximize food and beverage production efficiencies, it is essential to understand the key
sources of Manufacturing Losses which typically involve:
▪ Planned Losses: Cleaning, preventative maintenance, no demand, development, holidays, etc.
▪ Operational Losses: Changeovers, stoppages, breakdowns, materials shortages, personnel shortages,
quality checks, infrastructure failures (no power, no air, etc.).
▪ Speed Losses: Speed reductions or cycle time extension vs. the expected operational speed
(intentional or otherwise).
▪ Quality Losses: Scrap product, time and material loss due to defective materials, rework.
Since “Good Production” is defined as Maximum Possible Production, the reality is that many production
lines or work cells in use today are operating at less than 60 percent, and in many cases even less than 50
percent. Hence, there is tremendous potential for improvement in current production processes.
Another important insight that is confirmed by real data from users of automated data collection systems
on high speed mechanized lines is that downtimes related to machine jams and other short stoppages
occur much more frequently than the plant management team realizes. One hundred or more short
stoppages per shift often occur on a single line, with each stoppage typically averaging one minute. Many
operators do not even consider these short stoppages to be “downtime” given that there was no need to
call maintenance; they are accustomed to dealing with the numerous jams and other failures that
frequently occur on automated lines, and indeed consider it a part of their daily function.
This operational efficiency guide will explain how utilizing existing instrumentation to facilitate the
delivery of a comprehensive and versatile set of web-based real-time reports—and with the rapid
identification of process areas and systems for improvements—together provide the best payback in
terms of plant efficiency. TrakSYS™ quickly and efficiently integrates into existing operations to offer a
complete solution that not only includes real-time reports, but also includes visual management tools and
customizable dashboards providing a cohesive overview of your operations that indicate points for
production improvement and optimization.
Reducing Process Variability
The running of a complex food or beverage manufacturing operation involves many factors. At the heart
of any improvement program must be an effort to reduce the process variability. On a daily basis, plant
operations teams seek to optimize the key elements involved in the process, which include:
▪ Equipment.
▪ Raw Materials (ingredients, consumables, packaging, etc.).
▪ People (operators, maintenance technicians, managers, planners, contractors, etc.).
Effectively Improve Operational Efficiency Page 4
All print and electronic rights are the property of Parsec Automation Corp. © 2014
▪ Infrastructure (business systems, communication networks, utilities, etc.).
Unfortunately, reducing process variability is a moving target given the large number of sources of that
variability, hence the need for continuous monitoring and easy access to current efficiency and downtime
data. This allows process problems to be addressed in real time rather than after the fact, when the daily
production target has already been missed. This also provides the potential for predictive maintenance,
where a system is observed to be performing outside of its specified operating parameters and
maintenance is conducted proactively, rather than reactively, after a major system failure.
Key Elements of a Solution
The most critical elements involved in taking a plant that may be running at 50 or 60 percent efficiency
and providing the tools that will allow it to get to 70 percent during a one year period are:
▪ Management involvement to set the objectives and provide the focus required to get all team
members understanding and involved in the efficiency improvement process.
• The management team must also provide periodic reviews and ensure that the improvement
processes and systems that are put in place are being fully utilized.
• The team will typically involve members from Operations, Maintenance, Engineering, and Quality.
▪ An out-of-the-box solution that may be rapidly implemented and at a cost that produces a return on
investment in under 12 months, as opposed to custom implementations which require a significant
amount of capital and custom programming to implement, support, maintain, and enhance.
▪ Real-time data collection directly from the process equipment—typically via PLCs (Programmable
Logic Controllers), OITs (Operator Interface Terminals), HMI (Human Machine Interface) systems, and
plant databases.
• This data collection should utilize existing plant data networks and industry standard
communication drivers like OPC (OLE for Process Control), however, it should NOT require
changes in the existing PLC, OIT, or HMI code, which can produce support issues, and in regulated
industries, the need for revalidation of the line.
• A component that selectively involves operators in the process but does not make the operator
the key collector and classifier of the data. It should also be able to integrate with any existing
shop floor PC or SCADA (Supervisory Control and Data Acquisition) system, typically through a
browser-based interface.
▪ Web-based reporting via a standard browser that allows all team members involved in the
improvement efforts to easily share information, or to allow equipment vendors to monitor the
machines they are servicing.
▪ A wide variety of summary level and detailed web-based reports that provide different users the
ability to understand the source of losses and to take corrective actions.
▪ The solution must be user configurable without programming; therefore, the system owner may keep
the system in step with any changes in plant configuration, and the system logic may be modified as
the plant operations begin to improve.
Effectively Improve Operational Efficiency Page 5
All print and electronic rights are the property of Parsec Automation Corp. © 2014
▪ The web-based reports should be self-configuring, so that as the plant configuration is changed, no
programming is required to generate updated reports. This significantly reduces the cost of
maintaining and fine-tuning the system as more data is sought as part of a continual improvement
process.
▪ The configuration capability should allow the user to exclude consequential downtimes that are a
result of upstream and downstream failures.
▪ Supplementary data such as SKU, package size, work order number, line speed, shift, etc. that will aid
report users in understanding process issues, should be captured as a system goes down or comes
back up.
▪ The solution should provide utilities that aid in the long-term support of the production monitoring
system, such as the ability to archive a portion of the database, report on archived data, compress the
database, output data as a .CSV file, and output the system configuration in XML format.
As previously indicated, a key element of the solution for reducing process variability is to rapidly integrate
an out-of-the-box solution that produces a return on investment in under 12 months. TrakSYS™ offers
real-time visibility into production processes for production area managers and operators through web-
based interactive dashboards that are easily arranged and quickly deployed, producing a positive and
immediate impact on operations that can easily scale with your operations. To make the value proposition
even more attractive—because of its versatile technology and small footprint—the cost of ownership is
incredibly low. TrakSYS™ accomplishes this by leveraging the existing infrastructure of the factory, without
disrupting ongoing production or requiring significant additional investment of resources and capital.
Data Collection and Operational Intelligence
Accurate measurement of equipment stoppages and their causes is possible today, typically by using
existing instrumentation and plant networks. Many food and beverage plant managers, however, are
unaware of either the advances in techniques for both acquiring and presenting the data in a meaningful
format to enable production efficiency to be raised, or the potential return on investment implementing
such systems can bring. Consequently, the prevailing method today of recording downtime is still the
operator using a clipboard and paper, or whiteboard, and later transferring the information to a
spreadsheet. This method is at best delayed; by the time the data is analyzed a day or week later, it no
longer has significant value because the plant is now dealing with its current set of problems. Forthcoming
examples will illustrate how TrakSYS™ can seamlessly synthesize operational intelligence into
customizable dashboards, paperless reports, and alerts that automatically provide plant managers and
operators with the critical information that they need, when they need it, and in a format that can easily
be understood.
The principle of Operational Intelligence is to maximize the operation of a line or plant by better
understanding the causes of losses and by delivering efficiency data as expediently as possible to the right
people. The optimization process must shed light on equipment issues, operational issues, maintenance
Effectively Improve Operational Efficiency Page 6
All print and electronic rights are the property of Parsec Automation Corp. © 2014
problems, and vendor problems (i.e., equipment not performing to specification or defects in
consumables and supplied raw materials).
Many food and beverage factories, by virtue of having instrumentation attached to their equipment,
already have a sufficient infrastructure in place that can be utilized to provide the basic framework of a
production monitoring system. Utilizing knowledge of production progress, bottlenecks and constraints,
asset performance, and workflow patterns, TrakSYS™ dynamically maps process capabilities. Specific
intelligence concerning actual capabilities for each product (SKU) by asset, resource, and date ranges is
used to significantly improve the accuracy and effectiveness of production planning and scheduling and
to reduce work in process (WIP).
Consider for example, a vitamin packaging line consisting of a tablet filler, followed by a capper/sealer
system, labeler, case packer, shrink wrapper, palletizer, and stretch wrapper. Under automatic control of
the PLC program, tablet bottles are passed under the filler heads and then filled, plastic seals and caps are
then put on in the capper/sealer, labels are applied to the bottles, and then they are processed through
the rest of the packaging line.
At any given moment in time, the PLC software is responsible for evaluating the conditions of this sub-
process and deciding what to do next. Let us imagine that during a normal running shift, the capper runs
out of caps. A beacon is activated, an alarm sounds, and an operator is alerted to refill the cap bin and
restart the process. This operation takes one or two minutes at the most. Does the equipment operator
record a downtime incident on his clipboard? Probably not. Even if the operator considered the downtime
significant (unlikely because of the short duration), he probably sees nothing significant in the event—it
is a part of the job he does several times a day. In any case, documenting that the capper had run out of
caps and stopped the line—is something the operator may not be too keen on admitting!
Because the instrumentation understands the bottling process, it is possible for this information to be
communicated to another automated system and recorded without interfering in the process itself.
Indeed, there are many other signals available to report additional downtime reasons, currently reported
to the operator via message displays, stack lights, and other indicators. However, this data is typically not
preserved once the line restarts. TrakSYS™ can be configured to allow production personnel to manage
production events and tasks, be alerted to area-specific and relevant events, catalog root causes of
problems, record observations, and view real-time and historical reports. TrakSYS™ does this by directly
interfacing in real time to the various manufacturing operations, systems, and applications, and also
engages the human resources that are part of the overall execution workflow. By managing the multi-
source data acquisition, analytics, and business rules, TrakSYS™ delivers a well-focused wealth of
personalized, relevant, and timely manufacturing intelligence (MI) that is critical for effective decision
making. MI is delivered via the TrakSYS™ web-based knowledge portal—for real-time use—to the office,
remote, and mobile clients.
Effectively Improve Operational Efficiency Page 7
All print and electronic rights are the property of Parsec Automation Corp. © 2014
Web-Based Visualization
Today, the preferred delivery mechanism for information is invariably by means of an organization’s
Intranet or the Internet. Requiring no special client software to be installed, the browser is an ideal
visualization tool for reporting this information. As seen in the following illustrations, TrakSYS™ offers
graphical and tabular information can easily be delivered and accessed by those requiring it.
The report in Figure 1 details a live web page in TrakSYS™ showing the calculated real-time KPIs and
runtime information of a production line; this is an ideal method for supervisors and managers to get the
big picture at a glance, related to how well the line is running. In this scenario, the dashboard shows a
productivity snapshot: The table represents the current OEE, Cycle Time, and other KPIs for the current
shift; the pie chart breaks down the overall time for the shift by runtime and downtime codes used by the
factory; the Pareto chart displays the top five downtimes by fault code experienced during the shift. The
machine graphics at the bottom of the dashboard provide quick links to more detailed reporting for the
Figure 1- TrakSYS™ Produces Real-Time OEE Trends Enabling Managers to Effect Change When it Matters: Now
Effectively Improve Operational Efficiency Page 8
All print and electronic rights are the property of Parsec Automation Corp. © 2014
shift or other user-defined production period. This information can help you determine if you are going
to meet your production targets for the current production run, shift, or day.
Overall Equipment Effectiveness (OEE) has emerged as the premier metric for measuring factory
productivity, and as with all critical production data, flexibility in the overall reporting system is important.
The previous dashboard report illustrated a single shift within a complete week of production. It is
necessary for analysis purposes to be able to rapidly generate reports for other time periods—by
production run, by day of the week, and other group data, such as by SKU—so that important trends and
conditions may be observed by the process improvement team.
The report in Figure 2 identifies different downtime causes for a line on a system-by-system basis, showing
both the number of downtime events and the total number of lost production minutes. This report will
typically be monitored for the current shift so that emerging problems can be addressed before significant
productive capacity is lost.
Different reports are needed for different audiences. The TrakSYS™-produced report in Figure 3 shows
over 76 downtimes, and each averaging approximately three minutes. Over a week, this would average
Figure 2- Historical Information via TrakSYS™ Helps Managers to Quantify Lost Time by System
Effectively Improve Operational Efficiency Page 9
All print and electronic rights are the property of Parsec Automation Corp. © 2014
out to over 500 downtimes and 1,800 minutes—or 30 hours of production time lost on this line. At any
cost, this would be an unacceptable level of downtime were it perceived as such by a plant manager.
Typically, however, this production loss is merely factored into a plant efficiency calculation, reducing the
overall efficiency by some unknown fraction.
How can more detailed information be used to best target areas for improvement? Again, flexibility in the
overall reporting system is important.
Figure 3- Detailed Information Provided by TrakSYS™ Helps Managers Perform Root-Cause Analysis
Effectively Improve Operational Efficiency Page 10
All print and electronic rights are the property of Parsec Automation Corp. © 2014
Figure 4- Downtime Reason Selection
This report also gives an indication that there are times when it is important to involve the operators in
the data collection process. When there is not enough detail available from the automated systems
relating to the cause of a downtime, it is useful for the operator to be able to rapidly classify (from a
predefined list of reasons) and annotate particular incidents for later analysis.
In Figure 4, the equipment operator has been prompted by TrakSYS™ to acknowledge a downtime event
(Label Jam) by selecting an associated reason code from a pre-configured list. There is also a Notes field
designated for the operator to enter additional comments or an explanation for the specific incident. The
key issue to bear in mind is that operators are not downtime trackers, and they should be interrupted as
infrequently and for as short a time as possible. Whenever possible, equipment operators should not be
required to interact with a production monitoring system at all. When interaction is absolutely required,
a simple acknowledgement of a downtime event should be made from a predefined list of reasons as to
why the downtime event occurred.
Effectively Improve Operational Efficiency Page 11
All print and electronic rights are the property of Parsec Automation Corp. © 2014
Consider a bottle filling line. We can identify from the instrumentation when the labeler is out of labels,
and the line has therefore paused. The operator should simply reload a new roll and restart. We would
always want to record both the fact that this event happened and its total duration, but there is no need
to ask the operator for any information since we understand the downtime issue. What if the labeler was
out of labels for 10 minutes, and the line was paused for that entire length of time? In this case, we would
want to ask the operator for an explanation since the normal procedure of loading a new roll should be
completed in a shorter amount of time.
But how can we be sure which downtimes are real and which are simply consequential upstream or
downstream events resulting from material starvation or product jams? Usually, this comes down to the
thoughtful implementation of the tracking system and the presentation of the resulting acquired data in
a well laid out report.
Figure 5 shows all downtime events for a labeling system within a user-defined time frame. Presented in
a Gantt-like format via TrakSYS™, this report clearly illustrates the cause-and-effect relationships between
cascading faults on the labeling system, and their effect on other equipment centers both upstream and
downstream in the production line. The data acquisition and reporting tools within TrakSYS™ allow all
downtime conditions to be identified, tracked, and resolved to the root cause. Once accurate downtime
data is captured, it is necessary that engineering and management personnel are able to utilize this
information in real time to monitor key production indicators so that timely action can be taken to ensure
optimum line efficiency.
Figure 5- Downtime Gantt Chart Compiled by TrakSYS™
Effectively Improve Operational Efficiency Page 12
All print and electronic rights are the property of Parsec Automation Corp. © 2014
Figure 6 details a live web page produced by TrakSYS™ showing the calculated efficiency of a production
line; this is an ideal method for supervisors and managers to get the big picture at a glance, in relation to
how well the line is running. In this scenario, you can see the OEE, each of its components, and the
production summaries.
Figure 6- TrakSYS™ Web Reporting Portal Allows Managers to Quickly Review Production Statistics
Effectively Improve Operational Efficiency Page 13
All print and electronic rights are the property of Parsec Automation Corp. © 2014
A TrakSYS™-generated Mean Time Between Failures (MTBF) report is shown in Figure 7; this is a critical
report used to gauge the effectiveness of preventative maintenance programs as well as operator training,
related to solving problems on the line.
Figure 7- TrakSYS™ MTBF by Machine
Effectively Improve Operational Efficiency Page 14
All print and electronic rights are the property of Parsec Automation Corp. © 2014
Figure 8 shows the trend of actual line speed versus target speed, and compares this with the operating
time for the line. TrakSYS™ can quickly present this comparison in a single report or dashboard, which is
invaluable in terms of reducing rate loss and optimizing line speeds.
As demonstrated, timely and non-disruptive involvement of the operators is a critical factor in the
successful execution of continuous improvement programs and Lean initiatives. TrakSYS™ accomplishes
this offering configurable visualization and interactive dashboards for key production area operators and
alerts them to recent and ongoing production events such as stoppages, quality problems, and
slowdowns. These events can be selectively viewed, categorized, annotated, and acknowledged by
operators. TrakSYS™ also informs operators of KPIs and other relevant production information in real
time, which may also be used to manage quality tasks, SPC measurements, and maintenance activities.
Summary
Real-time data collection tools, coupled with web-based distribution of critical food and beverage
manufacturing information related to downtimes and efficiencies, are allowing users of these tools to
focus the manufacturing team on improving overall efficiency.
Providing accurate data which will cost-justify targeted improvements in the existing lines without
burdening the operator will be key to:
▪ Minimizing process variability.
▪ Maximizing asset utilization and productive capacity.
▪ Verifying maintenance intervals (tie into CMMS- Computerized Maintenance Management
Systems).
▪ Justifying equipment upgrades with hard data.
Figure 8- TrakSYS™ Real-Time vs. Operating Time
12/20/2013 12/20/2013
Effectively Improve Operational Efficiency Page 15
All print and electronic rights are the property of Parsec Automation Corp. © 2014
▪ Establishing your plant as a least cost producer.
▪ Tapping your plant’s hidden extra capacity.
Taking steps to automate the tracking of line efficiencies and downtime data will represent the next major
step in the evolution of food and beverage plant floor automation. By implementing TrakSYS™, this
approach provides the technology for innovative partnering approaches with equipment and
consumables vendors that can result in higher line output rates. TrakSYS™ also provides the accurate,
real-time data that can be used on a continuous basis as part of a TPM program to make and maintain,
major advances in overall equipment effectiveness.
Effectively Improve Operational Efficiency Page 16
All print and electronic rights are the property of Parsec Automation Corp. © 2014
ABOUT PARSEC
Parsec Automation Corp. (Parsec) is the developer of TrakSYS™, the leading real-time operations and
performance management software. Manufacturing companies worldwide rely on Parsec for flexible and
configurable tools to execute manufacturing operations across the value stream more effectively.
Without production disruption, TrakSYS™ helps manufacturers to significantly improve asset utilization
and efficiency, increase capacity with no new capital equipment, reduce production costs, decrease lead
time, and improve profitability. With measurable ROI, TrakSYS™ delivers the bottom-line results that
manufacturing companies are looking for. For more information about Parsec, please visit the corporate
web site at www.parsec-corp.com.
TrakSYS™ is a flexible, scalable, and powerful software application that is specifically designed to improve
the management and execution of manufacturing operations. TrakSYS™ is designed to measure, control,
and improve process capability and performance throughout the value stream regardless of
infrastructure. TrakSYS™ makes it possible to define KPIs specific to each area of operations for meaningful
insight into constraints and their root causes. This makes performance an enterprise initiative instead of
an isolated endeavor. By prioritizing bottlenecks by impact, TrakSYS™ helps to streamline continuous
improvement efforts to get the best ROI in the shortest time possible, and TrakSYS™ makes it possible to
reduce the lead time throughout the value stream.
TrakSYS™ is Designed to Effectively Help Manage Manufacturing Operations and
Their Performance in Real Time
Effectively Improve Operational Efficiency Page 17
All print and electronic rights are the property of Parsec Automation Corp. © 2014
TERMS AND CONDITIONS OF USE
Upon receipt of this electronic publication, it is understood that the user will and must fully comply with
the terms and conditions of use as stipulated herein.
This publication is protected by United States copyright laws and international treaties. Unless otherwise
noted, the entire contents of this publication are copyrighted by Parsec Automation Corp., and may not
be reproduced, stored in another retrieval system, posted on any website, or transmitted in any form or
by any means without prior written consent of Parsec Automation Corp. Unauthorized reproduction or
distribution of this publication, or any portion of it, may result in severe civil and criminal penalties, and
will be prosecuted to the maximum extent necessary to protect the rights of Parsec Automation Corp.
The trademarks and registered trademarks of the corporations mentioned in this publication are the
property of their respective holders. All information contained in this report is current as of publication
date. Information contained in this publication has been obtained from sources Parsec Automation Corp.
believes to be reliable, but is not warranted by the publisher. Opinions in this publication reflect judgment
at the time of publication and are subject to change without notice.
THIS DOCUMENT IS FOR ELECTRONIC DELIVERY ONLY
The following are prohibited:
Transmittal via the Internet
Reproduction for sale
Posting on any web site
© 2014 Parsec Automation Corp. All rights reserved. TrakSYS™, LOGICTrak™, MODELTrak™, INTELLITrak™,
GLOBALTrak™, EVENTTrak™, ALERTTrak™, SENSORTrak™, LEANTrak™, PRODUCTTrak™, WEBTrak™, HISTORITrak™,
AUDITTrak™, IMPROVETrak™, SPCTrak™, BATCHTrak™, and any other Parsec products and services mentioned
herein as well as their respective logos are trademarks or registered trademarks of Parsec Automation Corp. All other
products and service names mentioned are the trademarks of their respective companies. Data contained in this
document serve informational purposes only.