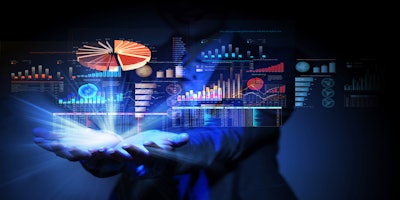
ERP in Food and Beverage
Tracing the Path to Success
December 2013
Nick Castellina
This document is the result of primary research performed by Aberdeen Group. Aberdeen Group's methodologies provide for objective fact-based research and
represent the best analysis available at the time of publication. Unless otherwise noted, the entire contents of this publication are copyrighted by Aberdeen Group, Inc.
and may not be reproduced, distributed, archived, or transmitted in any form or by any means without prior written consent by Aberdeen Group, Inc.
December 2013
ERP in Food and Beverage: Tracing the Path
to Success
Of all of the types of manufacturers out there, food and beverage
manufacturers may be subject to the most unique business pressures and
requirements of them all. These organizations deal with materials and
finished goods that can spoil, may become hazardous, or are subject to a
variety of regulations. Mistakes can cost the organization greatly in fines and
public perception. At the same time, these organizations have similar
requirements to other manufacturers when it comes to the business
systems that are used to manage operations and give business leaders
visibility that can enable informed decisions. Therefore, food and beverage
manufacturers need a business solution that can manage the front and back
office from end-to-end, as well as provide detailed visibility into materials
and finished goods in order to meet their requirements. As such, according
to the 2013 ERP Benchmark Survey, 94% of leading food and beverage
manufacturers have implemented Enterprise Resource Planning (ERP). This
report, based on two Aberdeen surveys, uncovers the pressures that food
and beverage manufacturers face as well as the ways in which they address
these pressures through ERP.
A Need for Something More
The H1 2013 Aberdeen Business Review identified the top pressures facing
food and beverage manufacturers (Figure 1).
Figure 1: Top Pressures in Food and Beverage
Source: Aberdeen Group, June 2013
Fifty-eight percent (58%) cited an inability to predict demand. When
organizations cannot accurately predict demand, products either sit on the
shelf or the organization is unable to sell as much of its product as it could
have. These problems are compounded in food and beverage where
products or materials could spoil. Therefore, organizations need better
36%
38%
58%
0% 20% 40% 60%
Inadequate business systems
Market perception of your
organization / competitors
Decreasing / Unpredictable demand
Percentage of Respondents, n = 53
Sector Insight
Aberdeen’s Sector Insights
provide strategic perspective
and analysis of primary
research results by industry,
market segment, or geography.
Aberdeen Methodology
In this report, Aberdeen groups
respondents into two maturity
classes:
√ Leaders: Top 35% of
respondents based on
performance
√ Followers: Bottom 65% of
respondents based on
performance
ERP in Food and Beverage: Tracing the Path to Success
Page 2
© 2013 Aberdeen Group. Telephone: 617 854 5200
www.aberdeen.com Fax: 617 723 7897
visibility into their supply chain, their customers, and their operations in
order to be more accurate in demand planning and make smarter
investments.
Thirty-eight percent (38%) of food and beverage manufacturers noted
market perception as a top business pressure. While this is important for all
organizations, food and beverage manufacturers are uniquely susceptible to
public relations nightmares if their products make people sick. These
organizations need to do a better job of keeping track of the status of their
materials and being able to track where they end up, in case a recall is
needed.
As a result of the above pressures, and many more, the third biggest
pressure in food and beverage is “inadequate business systems” (36%). Not
only do some of the business systems they utilize not enable accurate
demand planning, or provide good visibility into the status of materials, but
these solutions may not contain functionality that enables the business to
run efficiently and effectively in a modern environment. These requirements
call for a full-fledged ERP solution that can meet the unique needs of a food
and beverage manufacturer, but also contain functionality inherent to
running a business.
ERP’s Impact on Food and Beverage
According to the 2013 ERP Benchmark Survey, food and beverage
manufacturers are attempting to combat the above pressures through a
variety of strategic actions that are aided by ERP (Figure 2).
Figure 2: Top Strategies in Food and Beverage
Source: Aberdeen Group, June 2013
The top two strategies of food and beverage manufacturers are streamlining
and standardizing processes. Through ERP, organizations can communicate
best practices across the organization and ensure that processes are
completed as intended. This also ensures that regulations are adhered to.
ERP is also used to streamline processes by connecting people with the data
they need to perform. Through ERP, employees can plan and execute more
18%
19%
25%
32%
49%
0% 20% 40% 60%
Optimize the use of current capacity
Reduce the number of disparate enterprise
applications / Integrate business applications
Modernize technology infrastructure and
applications
Streamline and accelerate processes to improve
efficiency and productivity
Standardize business processes
Percentage of Respondents, n = 68
ERP in Food and Beverage: Tracing the Path to Success
Page 3
© 2013 Aberdeen Group. Telephone: 617 854 5200
www.aberdeen.com Fax: 617 723 7897
effectively. A key component of this is optimizing the resources that are
already available to organizations.
In order to enable standardized processes that are streamlined, food and
beverage manufacturers look to modernize and simplify their business
systems. A food and beverage manufacturer that is running their business on
spreadsheets (or on paper!) cannot provide real-time data that is essential
to guiding the business. It would be virtually impossible to track materials
through to their final destination. Even with significant technology purchases,
a food and beverage manufacturer may not be in the clear. Disparate
systems can be complicated and lead to employees utilizing old or
redundant data. Therefore, food and beverage manufacturers look for one
single source of truth to run their business from end-to-end. This is
evidenced by the fact that 25% of food and beverage manufacturers note
“modernizing technology infrastructure and applications” and 19% note
“reducing the number of applications” as top two strategies.
Modernizing and Simplifying Business Systems
In alignment with the strategies of modernizing and simplifying business
systems, Leaders attempt to create business systems that can provide all of
the functionality that a food and beverage manufacturer needs in one place
(Figure 5). Unsurprisingly, 94% of Leaders have implemented ERP. This is
why Leaders are 47% more likely than All Others to have integrated
business systems that are a complete and auditable system of record. No
matter which process an employee is trying to complete, the data is at their
fingertips. Those food and beverage organizations that have implemented a
solution, such as ERP, that can run their business from end-to-end see
substantial improvements (see sidebar).
Figure 3: A One Stop Shop for Data
Source: Aberdeen Group, June 2013
To understand the functionality that may come with a full-featured ERP
solution for food and beverage manufacturers, examine the key modules
that Leaders implement in the February 2013 report, ERP in the Process
94%
63%
31%
44%
79%
43%
17%
39%
0%
20%
40%
60%
80%
100%
Enterprise Resource
Planning
Integrated business
applications serve as a
complete and auditable
system of record
Process flows that may
span different
applications can be
completed without
consciously switching
between multiple
enterprise applications
Data appears to be
shared across
applications seamlessly
and transparentlyP
er
ce
nt
ag
e
of
R
es
po
nd
en
ts
, n
=
6
8
Leaders Followers
How Do You Compare?
Food and Beverage
respondents to the 2013 ERP
Benchmark survey were ranked
on the following criteria:
√ Days to close a month:
Leaders – 6,
Followers – 6.6
√ Complete and on-time
delivery:
Leaders – 96%,
Followers – 87%
√ Internal schedule
compliance:
Leaders – 96%,
Followers – 87%
√ Inventory accuracy:
Leaders – 97%,
Followers – 90%
Direct Benefits of ERP
Both Leaders and Followers
report benefits received as a
direct result of their ERP
solution. Here is how Leaders
compare to Followers:
√ Reduction in operational
costs:
Leaders – 16%,
Followers – 9%
√ Reduction in
administrative costs:
Leaders – 17%,
Followers – 16%
√ Improvement in
schedule compliance:
Leaders – 12%,
Followers – 11%
ERP in Food and Beverage: Tracing the Path to Success
Page 4
© 2013 Aberdeen Group. Telephone: 617 854 5200
www.aberdeen.com Fax: 617 723 7897
Industries: Functional Ingredients to Create a Good Mix (Table 1). These
modules can aid in planning, execution, and resource allocation. Forecasting
and demand planning enable organizations to understand how much of a
certain material or finished good they will need to maintain profitability.
Material Requirements Planning and Purchasing ensure that the organization
will have the materials they need to meet forecasted demand. Lastly,
Capacity Requirements Planning and Master Production Scheduling are used
to ensure that operations run smoothly. All of these modules are
implemented at a higher rate in Leading organizations.
Table 1: Modules of ERP
Module Leaders Followers
Purchasing 90% 84%
Material Requirements Planning 79% 68%
Master Production Scheduling 69% 48%
Forecasting / Demand Planning 59% 38%
Capacity Requirements Planning 41% 29%
Source: Aberdeen Group, December 2012
Crucial Capabilities
But an effective ERP solution is more than just the modules that it contains.
An effective solution enables capabilities within the organization that
improve performance across all functions. Aberdeen’s 2013 ERP Benchmark
Survey illustrates some of the capabilities that leading food and beverage
manufacturers have enabled when it comes to managing manufacturing
operations and the supply chain (Figure 4).
Figure 4: Managing the Shop Floor and the Supply Chain
Source: Aberdeen Group, June 2013
For example, 59% of Leaders have standardized enterprise-wide procedures
for production planning and execution compared to 38% of Followers.
59%
69% 65%
31%
38%
56%
35%
16%
0%
20%
40%
60%
80%
Standardized
enterprise-wide
procedures for
production planning
and execution
Manufacturing
operations are
integrated and
coordinated with
customer service,
logistics, and delivery
organization
Ability to do demand
planning and
forecasting
Ability to share and
integrate data with
the extended
enterprise
P
er
ce
nt
ag
e
of
R
es
po
nd
en
ts
, n
=
6
8
Leaders Followers
How Do You Compare?
In the report ERP in the Process
Industries: Functional Ingredients
to Create a Good Mix,
respondents were ranked on
the following criteria:
√ Reduction in inventory
levels:
Leaders – 14%,
Followers – 6%
√ Inventory accuracy:
Leaders – 95%,
Followers – 91%
√ Days to close a month:
Leaders – 3.9,
Followers – 6.7
√ Manufacturing schedule
compliance:
Leaders – 94%,
Followers – 87%
√ Complete and on-time
shipments:
Leaders – 97%,
Followers – 89%
ERP in Food and Beverage: Tracing the Path to Success
Page 5
© 2013 Aberdeen Group. Telephone: 617 854 5200
www.aberdeen.com Fax: 617 723 7897
Through ERP, organizations can communicate best practices to ensure that
products achieve consistent quality no matter which plant they are
produced in. This also ensures that regulations are adhered to. Further, 69%
of Leaders have integrated and coordinated manufacturing operations with
the customer service, logistics, and delivery organizations. These functions
neighbor each other and should be connected to ensure collaboration and
efficiency. These two capabilities, enabled by ERP, help organizations to
achieve their goals of standardized and streamlined processes.
One of the most important processes that a food and beverage
manufacturer needs to excel at is demand planning and forecasting. Spoiled
products and materials will do them no good. Accurate demand plans are a
key to maximizing profits. Therefore, Leaders are 86% more likely than
Followers to have the ability to forecast and plan for demand. Further, to
plan for demand effectively, a food and beverage manufacturer must be privy
to data that originates outside of the organization. For example, how much
demand are its customers forecasting? Also, how much material will
suppliers be able to provide? As such, Leaders are almost twice as likely as
Followers to be able to share and integrate data with the extended
enterprise. It should be noted that the extended enterprise includes
regulatory bodies, of which a food and beverage manufacturer should be
acutely aware.
Regulations and compliance is just one of the reasons that food and
beverage manufacturers need ERP for visibility into their operations. Leading
food and beverage manufacturers are more likely to enable visibility with
ERP for a wide range of capabilities (Figure 5).
Figure 5: Visibility Enables Traceability
Source: Aberdeen Group, June 2013
Leaders are 85% more likely than Followers to have enabled real time
visibility into the status of all processes. This visibility enables decision-
makers to alter shipping schedules or production runs due to changes in
conditions. It also enables better analysis of how operations are impacting
50%
65%
56%
38% 38%
27%
60%
35%
12%
32%
0%
20%
40%
60%
80%
Real time
visibility into
status of all
processes from
quote to cash
Ability to track
product costs
Ability to monitor
regulatory
compliance
Automated
notifications
based on pre-
defined
conditions
Ability to do a
mock or real
recall
P
er
ce
nt
ag
e
of
R
es
po
nd
en
ts
, n
=
6
8
Leaders Followers
Fast Fact
√ Fifty-three percent (53%) of
Leaders are able to schedule
preventative maintenance for
assets in comparison to 40%
of Followers
√ Seventy-one percent (71%)
of Leaders are able to
combine planned warehouse
orders in comparison to 60%
of Followers
ERP in Food and Beverage: Tracing the Path to Success
Page 6
© 2013 Aberdeen Group. Telephone: 617 854 5200
www.aberdeen.com Fax: 617 723 7897
the bottom line. For example, 65% of Leaders have the ability to track
product costs. They can then purchase alternate materials or alter
processes to drive costs down if they become unprofitable.
Where visibility really impacts a food and beverage manufacturer is in
compliance. Non-compliance can create nightmares for a food and beverage
manufacturer. Through ERP, Leaders are 60% more likely than Followers to
have the ability to monitor regulatory compliance. Further, food and
beverage manufacturers really should know the minute their products are
deemed noncompliant. This can be enabled through automated alerts, which
is a capability that Leaders are more than three times as likely as Followers
to have. In crisis situations, recalls may become necessary. Through ERP,
Leaders are more likely than Followers to have the capability to trace
materials and recall only the goods that are affected.
Key Takeaways
In order to run their business efficiently and effectively while maintaining the
traceability necessary to maintain compliance and avoid public relations
blunders, leading food and beverage manufacturers modernize and simplify
their technology infrastructure. This means a complete and integrated ERP
package. In fact, 64% of Leaders have an integrated business system that
creates a complete and auditable system of record. These systems provide
the following benefits, alongside many others:
• Standardization. Leaders are 55% more likely than Followers to
have standardized procedures for production planning and
execution. This ensures that best practices are followed and
compliance is maintained.
• Enhanced planning. Leaders are 86% more likely than Followers
to have the ability to forecast and plan for demand. This ensures
that orders can be met and that product does not sit on the
shelves.
• Visibility and traceability. Leaders are 85% more likely than
Followers to have enabled real time visibility into the status of all
processes. They can track orders, costs, and materials. By being able
to track materials, organizations can understand which shipments
must be called in the case of crisis.
Food and beverage manufacturers that consider implementing these
capabilities and technologies can trace a path towards success.
For more information on this or other research topics, please visit
www.aberdeen.com.
ERP in Food and Beverage: Tracing the Path to Success
Page 7
© 2013 Aberdeen Group. Telephone: 617 854 5200
www.aberdeen.com Fax: 617 723 7897
Related Research
ERP in Wholesale and Distribution: A
Logical Solution to Logistical Challenges;
September 2013
ERP in Manufacturing: Creating a Hub
for Visibility, Collaboration, and
Innovation; July 2013
The Case for Cloud ERP in
Manufacturing: Alleviating Outdated
Concerns; March 2013
ERP in the Process Industries: Functional
Ingredients to Create a Good Mix;
February 2013
Author: Nick Castellina, Senior Research Analyst, Business Planning and
Execution ([email protected])
For more than two decades, Aberdeen’s research has been helping corporations worldwide become Best-in-Class.
Having benchmarked the performance of more than 644,000 companies, Aberdeen is uniquely positioned to provide
organizations with the facts that matter — the facts that enable companies to get ahead and drive results. That’s why
our research is relied on by more than 2.5 million readers in over 40 countries, 90% of the Fortune 1,000, and 93% of
the Technology 500.
As a Harte-Hanks Company, Aberdeen’s research provides insight and analysis to the Harte-Hanks community of
local, regional, national and international marketing executives. Combined, we help our customers leverage the power
of insight to deliver innovative multichannel marketing programs that drive business-changing results. For additional
information, visit Aberdeen http://www.aberdeen.com or call (617) 854-5200, or to learn more about Harte-Hanks, call
(800) 456-9748 or go to http://www.harte-hanks.com.
This document is the result of primary research performed by Aberdeen Group. Aberdeen Group’s methodologies
provide for objective fact-based research and represent the best analysis available at the time of publication. Unless
otherwise noted, the entire contents of this publication are copyrighted by Aberdeen Group, Inc. and may not be
reproduced, distributed, archived, or transmitted in any form or by any means without prior written consent by
Aberdeen Group, Inc. (2013a)