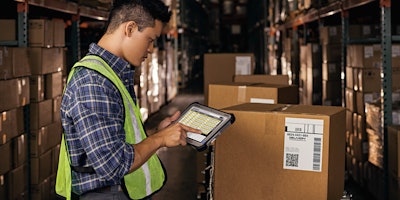
Panasonic
1Farm
-to-Table: Track & Traceability
MANUFACTURING REPORT:
Enabling Farm-to-Table Track &
Traceability with Mobile Technologies
TRACK &
TRACEABILITY
2Farm
-to-Table: Track & Traceability
Executive Summary
New data capture solutions can
increase insight into the supply
chain—from farm to table—
helping to ease the regulatory
compliance burden.
The FDA Food Safety Modernization Act (FSMA),
signed into law in 2011, is the most sweeping reform
of U.S. food safety laws in more than 70 years.
It aims to ensure that the U.S. food supply is safe by
shifting the focus from responding to contamination
to preventing it.1 These new standards aim to help
reduce the effects of foodborne illnesses, which affect
48 million Americans each year—including 3,000
deaths and 128,000 hospitalizations.2 Under the FSMA,
the Food and Drug Administration has new rules and
oversight responsibilities for implementing the new
food safety system, specifically in the areas of
prevention, inspection, compliance and response.3
While the overall benefits of the FSMA are clear, the law
does significantly impact the entire food supply chain,
creating compliance challenges for manufacturers and
their suppliers. These new regulatory challenges further
compound manufacturers’ existing concerns, such as
maintaining product quality, lowering costs to increase
profits and meeting the distribution demands of
retailers—all while satisfying consumers’ evolving tastes.
Now, the food industry is required to adopt more
reliable, accurate and robust track and trace processes
up and downstream—from sourcing to delivery. As a
result, food producers, manufacturers and distributors
are quickly working to modernize their operations and
tackle the subsequent technology challenges that arise.
A critical component to achieve FSMA compliance is
the integration of rugged and reliable enterprise-grade
mobile devices with automatic identification and data
capture (AIDC) systems, such as barcode or RFID
technology. This hardware and software solution
enables increased insight into the supply chain
through all stages of food production—from farm
to table. Once U.S. food manufacturers understand
the technology considerations and how to address
the challenges associated with implementing an
integrated mobile data capture solution, they will be
equipped with an efficient solution that not only helps
to achieve regulatory compliance, but also improves
other business challenges.
3Farm
-to-Table: Track & Traceability
A Fully Integrated
Automated Track and
Trace Process
For many food producers, manufacturers and
distributors, an automated track and trace process
that is fully integrated with the supply chain will
address existing business challenges and new FSMA
regulations. Ideally, this solution will contain several
key elements:
Automated data collection via rugged mobile
devices using barcode or RFID technology.
Data aggregation to provide supply chain
intelligence.
Integration into existing processes or
redefining processes to incorporate
track and trace.
One of the major challenges for many U.S. food
organizations is the lack of visibility across the supply
chain. As food supply chains grow increasingly
complex, it becomes more difficult for each element
of the supply chain to remain visible to other
elements in a single, comprehensible view.
Many agriculture and manufacturing organizations’
data collection methods rely on legacy systems and
paper-based processes. While some are decades old,
the industry continues to use these systems due to
costs associated with developing and implementing
new approaches or reluctance to change standard
operating procedures. These legacy processes can
contribute to inaccuracies during data transcription
and make real-time auditing nearly impossible.
With the FSMA’s impending compliance deadlines,
the U.S. food industry can no longer afford to delay
in re-evaluating legacy systems and must modernize
their technology infrastructure. While the individual
regulations vary based on product category, nearly
every juncture in the food supply chain—from
farms to retailers—will be subject to increased
and improved record-keeping standards.
Organizations implementing a fully automated track
and trace process along the supply chain must be
prepared to address additional complications
introduced by this process.
Automating data collection will increase available
data. This data overload can result in data mining
issues where stakeholders cannot find, analyze or
report on relevant data. An automated data
management system can help address these
problems. However, to be truly effective, it must
meet three key requirements:
1. Automated data capture must take
place across the food supply chain in a
consistent, secure and reliable manner.
2. Data capture and delivery must be
accessible anywhere and in all conditions,
from the farm field, to the factory floor,
to a distribution center, retailer or
corporate boardroom.
3. Data must be processed in real time.
These challenges require a robust data management
system consisting of rugged data capture hardware
and track and traceability software. Some
organizations may be forced to invest in a technology
overhaul to implement an automated track and trace
process, while others may need to simply upgrade
pieces of their existing infrastructure.
The food industry supply chain—
from farmers to retailers—must
be prepared to address challenges
created by data overload from
new traceability systems.
4Farm
-to-Table: Track & Traceability
For example, those using classic keyboard-based
devices or Windows CE devices will want to update to
touch-based hardware to increase mobility and ease
of use. No matter how data collection is currently
managed, electronic systems will need to be updated
to integrate new technology that will better
accommodate new regulations.
Mobile Solutions Enable
Better Traceability
Some food producers, manufacturers and
distributors may feel overwhelmed by the new
traceability requirements, but understanding the
possible solutions can help organizations know
how to start. The concept of traceability is better
understood when broken down into two parts:
Track follows a specific product through
the supply chain, primarily helping with
logistics and inventory management.
Trace, on the other hand, identifies the
origin of a specific product or ingredient.
This is essential for product recall and
investigation.
Traceability allows organizations to consistently,
accurately and quickly identify product origins in
order to better manage product integrity. This
ability then helps organizations identify areas to
improve process quality, which in turn helps them
deliver products that are both superior in quality
and lower in price.
With manual-based systems, accurately tracking
if ingredients were sourced from an affected
batch was difficult. Spreadsheets and other
documents would have to be carefully reviewed,
and the process could be so time-intensive, the
tainted ingredients could have found their way
onto store shelves or consumers’ kitchens. With
traceability solutions, however, information on
ingredient sourcing for specific lots can be
instantly retrieved from a database. This data
allows food manufacturers to intervene earlier on
and prevent the cost and bad publicity of a recall.
A successful track and trace system for the food
supply chain should consist of rugged mobile devices
implemented alongside software technologies such
as radio-frequency identification (RFID), barcodes and
Internet of Things (IoT).
The winning combination of these technologies is
proving to provide great advantage, and the food
industry is rapidly integrating it. According to Allied
Market Research, traceability technology sales are
on pace to reach $14.1 billion by 2020 with annual
growth of nearly 9%.4
Mobile traceability technology
sales are expected to reach
$14.1 billion by 2020 with annual
growth of nearly 9%.4
Consider the example of a batch of
tomatoes contaminated with listeria.
5RFID
RFID devices provide many advantages for food
traceability. They can be read from a great distance
and do not require a line of sight between the RFID
tag and sensor. Up to 40 RFID tags can be read at
once, allowing data to be gathered in bundles rather
than one at a time. This speed delivers a much
faster read rate than other approaches.
RFID tags can also use read/write technology, making
them even more versatile. Information about an
object can be stored on its RFID tag, then read later by
a different user. Data can also be encrypted or erased
as needed, adding extremely high security to RFID.
For example, RFID tags could be used with pallets to
track shipments of foodstuffs. Adding data about the
ingredients’ source could be written to the RFID tag,
thus enabling specific pallets to be easily located in
case of recall. Because data about ingredients is
tracked along the entire supply chain, only affected
shipments would need recalling. This insight helps
significantly minimize the total cost of recalls and can
even eliminate the need to pull unaffected products
from store shelves.
Finally, the physical RFID tags are quite rugged, with
the result that they are far more reusable than
barcodes. All these advantages mean that using RFID
for traceability and data management requires only
minimal human participation, resulting in less error
and more real-time reporting. Like any technology,
RFID does have disadvantages. Any liquid or metal
between the RFID tags and the reader can weaken
the signal (such as in very moist environments),
making accurate readings difficult in these scenarios.
A RFID system is also more expensive than some
other solutions.
Barcode
Barcode technology brings many advantages and
provides a cost-effective option for FSMA compliance.
Barcodes are small, imperceptibly light and
inexpensive. They are also widely used, helping to
reduce implementation costs, training and the cost of
cross-system integration. Barcode scanners can be
built to include good ergonomics, such as angled rear
scanners for easier barcode scanning at different
levels and screen viewing, so long-term use by workers
is comfortable. Unlike RFID, barcodes have no privacy
implications due to stored data.
One way barcodes enhance food manufacturing is
by improved inventory management. Whenever a
product is stored, moved or shipped, a barcode scan
can record storage location. This provides an accurate
snapshot of current inventory data for production
Farm
-to-Table: Track & Traceability
6Farm
-to-Table: Track & Traceability
and sales. This data can also be used to automatically
generate manifests during shipment to customers.
Though barcodes provide many benefits, the
technology also has its limitations. Barcodes are only
one-way communication; they can be scanned, but
additional information cannot be written into barcodes
as they move along the supply chain. Another
limitation is that barcodes require a direct line of sight
between the code and the scanner. Scanners must
be close to the barcode and they must be scanned
individually. This means deploying barcode solutions
requires additional human labor as compared to RFID.
Internet of Things (IoT)
IoT, the newest approach to traceability, offers the
food industry the ability to monitor multiple
information sources in real time. Handheld devices
that provide IoT data enable instant logging, readings
and consequently faster decision making. For example,
ingredient sourcing, manufacturing and final delivery
to retailers can all provide IoT data and create a
real-time, holistic view of manufacturing operations.
Many businesses are taking interest in this approach;
Gartner reports IoT spending for vertical-specific
business is expected to reach $911 billion by 2020.5
Data collected by employees through IoT devices
can be combined with neural network technology,
instantly providing analysis based on the most
relevant data. This ability is especially useful for
fresh foods and cold chain manufacturing, where
real-time information about temperature and other
environmental conditions can prove crucial in ensuring
and documenting quality. It can also help organizations
make real-time changes to help reduce spoilage
or contamination.
Of course, IoT is still an evolving technology. In its
current iteration, implementing IoT is too expensive
to deploy for individual product tracking like RFID or
barcode technology. However, it excels as a way to
gather data from the devices scanning individual
products. This data can then be used to create
real-time dashboards and give actionable insights
into the supply chain.
Rugged Mobile Devices
Most consumer mobile devices are not fit to be
used in the field or in manufacturing. Rugged
hardware purpose-built for these challenging
environments is essential to enabling track and
trace technologies along the entire food
supply chain.
On the Farm
Agricultural field workers need bright devices that
are visible during daylight, weather-resistant screens,
long battery life, locking controls, network connectivity
and the ability to physically wash off dirt, dust and
grime. Devices in these settings also need security
measures to prevent accidental or intentional harm.
By deploying rugged devices based on enterprise
versions of the Android or Windows operating
systems, workers in the field could gather FSMA
compliant data with minimal training. It’s also critical
to use enterprise-grade mobile devices in agricultural
operations where hazardous conditions are present.
For example, the environment in and around grain
silos is highly flammable due to the fine particles that
are in the air. Having rugged mobile devices that
conform to iSafe/ANSI standards provides a level of
protection from sparking or electromagnetic
discharge that could cause an explosive event.
At the Plant
Manufacturing plants, on the other hand, need devices
that can be customized for line workers, operation
managers and other shop floor employees. In these
environments, fully-rugged tablets and handhelds,
especially those with long battery life and low failure
rates, can reduce costly downtime and boost
efficiency. In addition, food manufacturers often need
to consider sanitization requirements when selecting
mobile devices. For example, a facility that produces
7Farm
-to-Table: Track & Traceability
products with and without nut ingredients needs to
be extremely diligent in sanitizing the production
lines as they switch from one product to the next.
Not performing this type of maintenance on the
equipment can cause cross contamination issues that
create potentially life-threatening allergic
consequences for the consumer. This maintenance
process typically involves hot water and/or additional
chemicals for wipe down. Having devices that can
survive repeated exposure to water and chemicals is
a must for these environments.
In the Warehouse
In shipping and receiving or distribution centers,
workers need to access critical stock and location
information in real time and in the most effective
way. From receiving and moving, to ordering and
dispatching stock items, rugged handheld devices
with an angled rear barcode reader ensure the
smooth running of warehouse operations. In
addition, look for mobile devices that forklift
operators can use and easily detach, allowing
for a single device on and off a forklift.
At the Store
Responding to a recall notice quickly is critical for food
retailers. Not only do they need to determine whether
affected shipments arrived in their stores, they need
to compare what is left on the shelf with what has
already been sold. Through handheld devices, food
retailers can quickly scan existing stock and learn
how much affected stock is in the hands of consumers.
Individual recalled food items can be identified in a
matter of moments, even if they are intermingled with
non-affected items. This reduces the amount of time
and potential risk to consumers faced during a recall.
Fortunately, rugged mobile devices are available
in multiple form factors, including smartphones,
laptops, tablets, 2-in-1 convertible tablets and
handheld barcode scanners, so any organization
requiring track and traceability can benefit from
this technology. Organizations in the food industry
should select a technology partner who can offer
the correct form factor, level of ruggedness and
associated peripherals which best suit the job
and environment at hand.
Farm
-to-Table: Track & Traceability
8Farm
-to-Table: Track & Traceability
The Benefits of
Mobile Devices for
Food Manufacturers
Rugged mobile devices that are purpose-built to
withstand the specific requirements of food
manufacturers offer several benefits.
1. Production costs decrease and operational
efficiencies improve when automating data
collection. Data collected from barcode and
RFID technologies can be automatically used
to inform supply decisions, thereby decreasing
delays due to sourced material shortage.
This real-time information allows food
manufacturers to optimize existing processes
and maximize resource allocation.
2. Using track and traceability technologies
improves safety and quality control. Good
traceability systems minimize the production
of unsafe or poor quality food products,
ensuring public health and decreasing
liability. The systems also help maintain food
authenticity by verifying ingredient sourcing.
3. These technologies improve customer
satisfaction as seen through traceability’s
effect on recall management. Because the
exact source of affected ingredients can be
traced during recalls, the recall accuracy,
timeliness and costs are improved, helping
to preserve brand perception. According to the
Grocery Manufacturer’s Association, an average
recall costs $10 million, takes 14 days to identify
and 34 days to enact. By the time product recalls
are enacted, only 40% of affected products can be
collected.6 Enacting recalls more quickly enables
organizations to improve the public perception of
the brand’s responsibility and also remove more
affected product. A quicker response means that
fewer customers will have a low-quality experience.
Deploying purpose-built devices can benefit the entire
food supply chain—from farm to table. Combining
traceability technologies with rugged purpose-built
mobile devices allows companies to have the exact
hardware for their specific production processes,
improving operations and minimizing downtime.
9Farm
-to-Table: Track & Traceability
Food manufacturers seeking to improve track and traceability
through mobile technologies should contact Panasonic today.
us.panasonic.com/Toughbook
(888) 245-6344
[email protected]
Sources
1. http://www.fda.gov/Food/GuidanceRegulation/FSMA
2. http://www.fda.gov/Food/GuidanceRegulation/FSMA
3. http://www.fda.gov/downloads/Food/GuidanceRegulation/FSMA/UCM379984.pdf
4. https://www.alliedmarketresearch.com/food-traceability-tracking-market
5. http://www.gartner.com/newsroom/id/3165317
6. http://www.gmaonline.org/downloads/research-and-reports/WP_RecallExecution.pdf
7. VDC Research – 2016 Mobile’s Place in the Connected Factory
Specializing in purpose-built devices for manufacturing needs,
Panasonic delivers solutions in a variety of accessible form factors,
including handheld barcode scanners, tablets, convertible 2-in-1 laptops
and laptops in screen sizes ranging from 4.7 inches to 20 inches.
Panasonic Mobility and Traceability
Whether employees collect data from a remote field
or a distribution center, the rugged performance of
Panasonic Toughbook devices is unmatched.
According to VDC Research, the most important
criterion for a manufacturer purchasing mobile
devices to support their workforce is quality/
reliability.7 As a core manufacturer, Panasonic sets
the industry standard for reliability with a less than
2% failure rate. Panasonic Toughbook computers,
tablets and handheld devices remain functional and
connected in the harshest environments, such as in
extreme inclement weather, hostile field conditions
and around heavy machinery and equipment.
Loaded with enterprise versions of Windows 10 or
the Android operating system, security never
compromises ease-of-use.
©2016 Panasonic Corporation of North America. All rights reserved