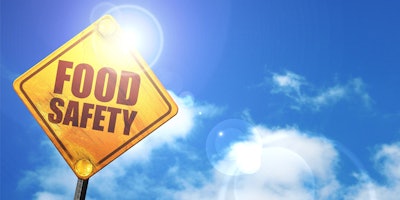
AIRPORT BAGGAGE IDENTIFICATION (ID) SOLUTIONS
World’s smallest 5MP stand-alone
vision system
Powerful Cognex vision tool library
including new PatMax RedLine™
and JavaScript support
High speed communication with
Gigabit Ethernet
Airport baggage handling systems (BHS) depend on reliable barcode reading solutions to help minimize luggage
processing times and enhance system efficiency.
1
Failure to read a bag tag sends that bag through a
manual encode process, which requires additional
processing time, extra manpower, and additional
conveying equipment and tracking of each bag.
Baggage processing times are critical to the
operational success of both the airline and the airport.
Overall customer service is critical to all stakeholders in
airport operations, and efficient handling of every bag is
paramount to the profitability of each BHS operation.
Baggage tag identification challenges:
• Baggage orientation and tag position can vary
greatly
• Optimal reader position is challenging due
to varying baggage heights, BHS rights-of-
way, building space constraints, and barcode
perspectives
• Bag tag readability is easily compromised
throughout each step of the handling process;
transfer bags often present the greatest tag reading
challenge
Cognex vision technology offers:
• Industry-leading read rates—fewer read failures
• Image archiving—saves a color image of every bag
processed associated with each discreet tag
• Lower cost of ownership—DataMan® barcode
readers have no moving parts
DataMan 300/360 series barcode
reader features:
• Three resolution options: 800x600,
1280x1024 and 1600x1200
• 60 reads per second
• Up to 400 ft/min (2.0 m/s)
transport speed
• Customizable to any application
ID Reader redundancy
Overlap in the coverage area of each DataMan reader in the system means multiple
readers will read each bag tag. Having a low ‘exclusive read rate’ means that an
exceptionally low number of bags are read by only a single camera. This assures the BHS
operator that if any single reader in the array fails to read, the decrease in the overall read
rate of the system will be minimal. Our superior reader coverage insures that each tag has
a very high likelihood of being ‘seen’ and then decoded by more than one reader.
www.cognex.com/300
AIRPORT BA I I LUTIONS
orld’s smallest 5MP stand-alone
vision system
Powerful Cognex vision to l library
including new PatMax RedLine™
and JavaScript sup ort
igh speed communication with
igabit Ethernet
Airport ba gage handling systems (BHS) dep r ing solutions to help minimize lug age
proce sing times and enhance system effici .
1
Failure to read a bag tag sends that bag through a
manual encode process, which requires a d tional
processing time, extra manpower, and a d tional
conveying equipment and tracking of each bag.
Bag age processing times are critical to the
operational success of both the airline and the airport.
Overall customer service is critical to all stakeholders in
airport operations, and efficient handling of every bag is
p ramount to the profitability of each BHS operation.
Baggage tag ident fication challenges:
• Bag age orien ation and tag position can vary
greatly
• Optimal reader position is challenging due
to varying baggage heights, BHS rights-of-
way, building space constraints, and barcode
perspectives
• Bag tag readability is easily compromised
throughout each step of the handling proce s;
transfer bags often present the greates tag reading
challenge
Cognex v sion techn logy offers:
• Industry-leading read rates—fewe read failures
• Image archiving—saves a c lor image of every bag
processed associated with each discr e tag
• Lower cost of ownership—DataMan® barcode
readers have no moving parts
i arcode
r
• r ti : 00x600,
0
• r
• t . / )
tr
• t lication
I
rl i r of each DataMan reader in the system means multiple
r r t g. aving a low ‘exclusive read rate’ means that an
ex ti r f bags are read by only a single camera. This assures the BHS
o r t i l r der in the ar ay fails to read, the decrease in the overall read
r t f t ill i i al. Our superior reader coverage insures that each tag has
a r i f i g ‘seen’ and then decoded by more than one reader.
www.cognex.com/300.c .c /XXX
IMPROVE FOOD SAFETY AND QUALITY
WITH MACHINE VISION
In no other industry are the incentives to guarantee product safety, quality and packaging integrity as great as they are in the
food and beverage industry. The negative effects of recalls and damage to brand reputation are so acute that food and beverage
manufacturers have been on the leading edge of successful deployment and use of machine vision technology to ensure product
s fety. As the hallenges b come greater and the stakes higher, food and beverage manufacturers need even more sophisticated
machine vision h rdwar an tools to stay compliant with new regulations, ensure customer confi dence and mitigate risks. At
the same ti e, these tools need to be easy to use and deliver even more reliable and repeatable results. In this expert guide, we
will familiarize you with current provisions and regulations around the world that govern food and beverage manufacturing and
id n fy the ore challenges faci g the industry today. Finally, we will tell you about machine vision solutions that will help you
produce and distribute the safest and highest quality products possible.
Regulations worldwide drive the need for Optical
Character Recognition (OCR)
In 2014 the United States Food and Drug Administration (FDA) issued nearly 400
recalls, market withdrawals and safety alerts for reas ns ranging from salmonella
to undeclared ingredients like milk, soy, and nuts. And it isn’t just happening in
US markets. The International Standards Organization (ISO) includes tracking and
labeling requirements for most agricultural products, while Japanese law includes
documenting everything from agricultural chemicals to slaughterhouse operations
(Abattoir Law).
Food producers and packagers are looking at how they can use track and trace
technologies to document food production automatically and give their management
team better insight at all levels of the supply chain in real time. Barcodes are a
traditional solution to track and trace operations, but consumers cannot read
barcodes. As a result, many producers are turning to optical character recognition
(OCR) technology using vision systems that can read alphanumeric text, as well as
1-D and 2-D Data Matrix codes, to track food and beverages from raw materials to
packaged product at high speeds and with greater accuracy than manual inspection
or barcodes alone.
Allergen Management
Mislabeled allergens cause expensive food product recalls because packaged foods
are required to list common food allergens such as milk, eggs, and peanuts that are
in the product or may have come in contact with the product.
Primary allergen management applications include:
• Verify the correct label and check position
• Detect errors on rolls of labels
• Match package to product
• Read codes and verify text on fl exible
fi lms and packages
• Read 1-D and 2-D (Data Matrix) codes
and text on labels
• Read barcodes and text on fl at, curved
or shiny surfaces
• Read and verify 2-D codes
printed direct on a product
or container surface
Food Safety Modernization Act: US
Gets Serious About Food Safety
The US Food Safety Modernization Act includes 19
new provisions that will impact the food-processing
industry. Several of those provisions are expected to
increase demand for machine vision to help ensure
that companies are preventing food contamination
rather than responding to it. Upon request, the FDA
will gain expanded access to food production facility
records. The agency may obtain records for tracking
purposes or if there is reason to suspect a potential
public health risk. In addition, the FDA, in coordination
with the produce industry, will create a new
method of effectively tracking and tracing fruits and
vegetables to ensure that any contaminated produce
is located and recalled in a safe nd timely m nner.
These new regulations apply to both domestic and
foreign food producers selling food in the US.
To fi nd out more visit the U.S. Food and Drug
Administration website: www.fda.gov
Food Traceability, Brand Protection, Code
Quality, Compliance, and Recall Management
Improve food safety and reduce liability exposure
Existing and pending food traceability legislation in many global regions
require that facilities have systems in place to provide a trail
of information that follows each food item through the supply chain.
To ensure food safety and effi cient recalls, manufacturers must be able
to identify and locate any item in the food supply chain and quickly
trace back its source “one step”, and trace forward to its destination
“one step.”
To achieve this, many companies are implementing 2-D barcodes, vision
systems, and image-based ID readers as key components in a simple yet
robust one up/one back database process for traceability.
Data Matrix has been adopted as standard in many applications. It
allows the storage of more information such as manufacturer, product
ID, lot number, expiry, and even a unique serial number on virtually any
fi nished good.
Brand Protection
Serial number aggregation for supply chain security and product
authentication at the point of sale can help prevent counterfeiting,
diversion and sale of product through unauthorized channels.
These applications generally seek item-level serialization on every
package and Data Matrix has been adopted as standard.
Code Quality and Package Compliance
As you prepare for compliance with global barcoding requirements, it’s
important to keep in mind that compliance requires much more than
simply reading a code on a label or package.
To support traceability, it is fi rst essential to verify code quality and
validate that all of the encoded data is accurate and correctly formatted.
Cognex verifi ers and vision systems can be used to grade code quality
and create a complete identifi cation and data verifi cation solution for
food and beverage labels and packages.
2
© Copyright 2015, Cognex Corporation. All information in this
document is subject to change without notice. All Rights Reserved.
The Cognex logo, Cognex.com, and Cognex are registered
trademarks of Cognex Corporation.
Lit. No. FSMV-2015-06
www.cognex.com
Corporate Headquarters One Vision Drive Natick, MA 01760 USA Tel: +1 508 650 3000 Fax: +1 508 650 3344
Companies around the world rely on Cognex vision and ID to optimize quality, drive down costs and control traceability.
Americas
Americas +1 508 650 3000
Europe
Austria +49 721 6639 393
Belgium +31 403 05 00 43
France +33 1 4777 1551
Germany +49 721 6639 393
Hungary +36 1 501 0650
Ireland +0808 168 3001
Italy +39 02 6747 1200
Netherlands +31 403 05 00 43
Poland +48 71 776 07 52
Spain +34 93 445 67 78
Sweden +46 21 14 55 88
Switzerland +49 721 6639 393
Turkey +90 212 306 3120
United Kingdom +0808 168 3001
Asia
China +86 21 5050 9922
India +9120 4014 7840
Japan +81 3 5977 5400
Korea +82 2 539 9047
Singapore +65 632 55 700
Taiwan +886 3 578 0060
AIRPORT BAGGAGE IDENTIFICATION (ID) SOLUTIONS
World’s smallest 5MP stand-alone
vision system
Powerful Cognex vision tool library
including new PatMax RedLine™
and JavaScript support
High speed communication with
Gigabit Ethernet
Airport baggage handling systems (BHS) depend on reliable barcode reading solutions to help minimize luggage
processing times and enhance system efficiency.
1
Failure to read a bag tag sends that bag through a
manual enc de process, which requires additional
processing time, extra manpower, and additional
conveying equipment and tracking of each bag.
Baggage processing times are critical to the
operational success of both the airline and the airport.
Overall customer service is critical to all stakeholders in
airport operations, and efficient handling of every b g is
paramount to the profitability of each BHS operation.
Baggage tag identification challenges:
• Baggage orientation and tag position can vary
greatly
• Optimal reader position is challenging due
to varying baggage heights, BHS rights-of-
way, building space constraints, and barcode
perspectives
• Bag tag readability is easily compromised
throughout each step of the handling process;
transfer bags often present the greatest tag reading
challenge
Cognex vision technology offers:
• Industry-leading read rates—fewer read failures
• Image archiving—saves a color image of every bag
processed associated with each discreet tag
• Lower cost of ownership—DataMan® barcode
readers have no moving parts
DataMan 300/360 series barcode
reader features:
• Three resolution options: 800x600,
1280x1024 and 1600x1200
• 60 reads per second
• Up to 400 ft/min (2.0 m/s)
transport speed
• Customizable to any application
ID Reader redundancy
Overlap in the coverage area of each DataMan reader in the system means multiple
readers will read each bag tag. Having a low ‘exclusive read rate’ means that an
exceptionally low number of bags are read by only a single camera. This assures the BHS
operator that if any single reader in the array fails to read, the decrease in the overall read
rate of the system will be minimal. Our superior reader coverage insures that each tag has
a very high likelihood of being ‘seen’ and then decoded by more than one reader.
www.cognex.com/300