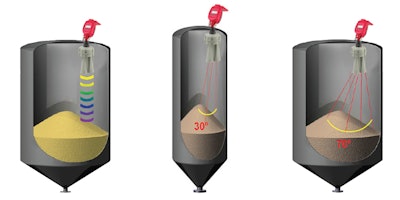
Measuring Volume in Bins, Tanks and Silos
If your operation requires storing materials in bins, tanks or silos containing ingredients, finished goods, or waste
materials, chances are monitoring the inventory in those silos is important to continuous manufacturing operations and
timely replenishment activities. An acoustics-based inventory management system has many advantages for food process-
ing operations and offers a variety of sensors that can meet the accuracy requirements and budgetary parameters for any
type of operation that routinely manages powders, granular and bulk solid materials. Commonly referred to as a 3DLevel-
Scanner or generically a scanner, this technology has revolutionized inventory management by taking the data
available to operations personnel from a simple, single point of level measurement to a complex volume
estimation with a very high level of accuracy.
Non-Contact for Food Safety
One of the many advantages of scanner technology is that there is nothing that comes into contact
with the material, so there’s no risk of contamination, making it safe for use in food processing operations.
The technology works by sending very low frequency acoustical signals to the surface of the material.
Scanners are proven to work in light powders like flour, fine granular material
such as sugar, all types of grains, and even hard to measure materials like
the waste of blood and feathers from poultry processing operations. It is
recommended for any material with a bulk density greater than 12 lb./ft.3
Reliably Penetrates Dust
Perhaps one of the greatest benefits of acoustics-based versus other level
measurement technologies is its ability to measure reliably in high levels of dust. Many
food processing operations routinely handle excessively dusty materials that can be
difficult to measure. Dust particles are prone to confusing the signals of some types of level sensors that won’t
measure at all or provide inaccurate data when dust is present. Scanners will perform reliably in high dust environments such
as soybean meal, providing highly accurate inventory data.
Self-Cleaning Reduces Maintenance
Due to the nature of acoustic pulses that “chirp” and send an almost imperceptible vibration through the device, the
sensor stays clean. This means it will perform consistently and reliably over a long period of time and require virtually no
maintenance. For excessively sticky, clingy materials, a Teflon® coated option can be used to further prolong the preventive
maintenance cycle. Other types of sensors may require routine maintenance at short intervals or an air purge for cleaning,
which can be expensive to run to the top of a tank. Some scanners also have the
ability to track the topography of the material in the silo, making it possible to detect
sidewall buildup, so removal of the buildup can be scheduled in a timely fashion.
Multiple-Point Measurement Accuracy
Most every device for monitoring materials in silos measures only a single fixed
point repeatedly in the same location. The scanner has the ability to measure
multiple points within the silo, which enables the software to calculate a much
more precise volume of material contained in the silo. Plus, these measurement
coordinates can be used for three-dimensional mapping of the contents to create
a visual representation of the material topography. It can be valuable to know if
buildup exists or if a cone is up or down when planning maintenance or replenish-
ment of inventory.
Multiple-point mapping and 3D visualization
indicate irregular topography in the silo.
800.278.4241 • 402.434.9102 • www.binmaster.com • [email protected]
© 2014 BinMaster. ®All Rights Reserved.
No Climbing Enhances Safety
No one likes risking an accident or OSHA violation and
all of the hassles, time and money that they present. By
eliminating the need for climbing silos to check inventory
levels, acoustic sensors make the workplace safer by
preventing accidents. As inventory data is sent from each
silo to a personal computer, the data can be viewed from
the safety of an office. OSHA regulations for climbing or
entering silos require compliance with stringent rules and
complicated paperwork that can be avoided using an
automated measurement system.
A Model for Better Accuracy
Scanners come in a variety of models to address the ac-
curacy desired, the vessel size, the behavior of the material,
and the budgetary parameters of an operation. The most basic
model – referred to as an RL for detecting reliable levels – will
measure material within a narrow beam directly below the
device. It is recommended when the level of material in the
vessel needs to be monitored continuously and is well suited
to materials that flow freely and are less prone to buildup.
When an estimation of volume is also needed, more com-
plex processing of data is performed by an S model that de-
termines average volume based upon an average level in the
vessel determined by multiple measurements taken within
a 30° beam angle. This model is ideal for smaller diameter
silos up to 16 feet in diameter and up to 200 feet tall.
For very high levels of volume accuracy, the M model
measures material within a wider 70° beam angle and
is appropriate for larger silos or silos with highly irregular
topography. The M model provides high, low and
average levels, plus a very accurate volume estimation
based upon multiple measurements across the material
surface.
The addition of visualization of the material surface is
provided by an MV model that measures and maps the
surface and displays a graphical representation of the
topography of the material in the silo on a computer screen.
This can be used in the detection of cone up or down condi-
tions or to identify where there may be buildup in the vessel
that may need removal. This model is most often applied
in powders or other materials prone to buildup or in larger
vessels with multiple filling and emptying points.
Although any scanner model can be used in any size
vessel, a thorough understanding of the desired level of
accuracy will determine which model will provide the best
performance.
Acoustic level sensors are revolutionizing inventory
management in bins, tanks and silos by providing more
accurate, continuous, real-time information to help make
operations safer and more efficient. Plant managers report
that they are able to buy smarter, replenish when needed,
reduce safety stock and keep their employees out of harm’s
way with a scanner system.
The RL detects level in a narrow beam
and is ideal for silos of all sizes where a
single measurement point is adequate.
The S model measures multiple
points within a 30° beam angle
and is ideal for smaller silos.
For larger silos, the M model measures
multiple points within a 70° beam angle
to accurately calculate volume.
30°
70°