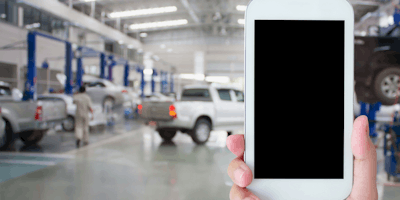
IFS
W
H
IT
E
PA
PE
R
WHAT ONE ERP FAILING
COULD HAMSTRING
YOUR AUTOMOTIVE
LEAN INITIATIVE?
CONTENT
PACKAGING OVERLOOKED ........................................................................................... 2
ERP challenge: packaging management .................................................................. 2
FLOW OF GOODS AND FLOW OF PACKING MATERIAL ARE CLOSELY CONNECTED ........... 4
THE PACKAGE FLOW MUST BE EXACTLY TRACKED ....................................................... 5
THE WHOLE IS MORE THAN THE SUM OF ITS PARTS ..................................................... 6
ABOUT IFS ................................................................................................................. 7
1WHAT ONE ERP FAILING COULD HAMSTRING YOUR AUTOMOTIVE LEAN INITIATIVE?
WHAT ONE ERP FAILING
COULD HAMSTRING YOUR
AUTOMOTIVE LEAN INITIATIVE?
BY STEFAN ISSING
GLOBAL INDUSTRY DIRECTOR, AUTOMOTIVE
IFS AB
Tight supply chains—such as those found in the automotive industry—require highly
integrated enterprise resource planning (ERP) software designed specifically for the
automotive sector.
Because ERP has its origins in the automotive industry, repetitive manufacturers
in the automotive sector are particularly well-served by many established software
offerings. But there is one gap in these solutions that will put even the most sophis-
ticated automotive manufacturer at risk.
What is this gap? Packaging. A perfect Just-In-Time (JIT) automotive environ-
ment, that manufactures every part right when it is needed, will still grind to a halt
if the packaging necessary to ship this part is not available. The overwhelming
majority of ERP software products fail here, and this can be an expensive failure for
automotive manufacturers:
• Manufacturers often need to license and implement a stand-alone system to
handle packaging and packaging structures. This brings increased costs to
license the solution, train users, write interfaces with the incumbent ERP and
then uplift the integrations during ERP upgrades.
• Packaging is an intimate component of the manufacturing process, and touches
purchasing, production, shipment processing and other parts of the business.
This means it is very hard to handle with a point-to-point integration between
ERP and third-party packaging software.
• Non-value-added work is created because, for the vast majority of tasks, users
will need to switch back and forth between ERP and packaging software. These
silos of information will also create blind spots that will come back to bite
executives when unanticipated problems arise, causing product deliverability
issues.
2WHAT ONE ERP FAILING COULD HAMSTRING YOUR AUTOMOTIVE LEAN INITIATIVE?
Once we consider the central role that packaging plays in the automotive manufacturing
value chain, it becomes a fourth pillar in the organization. Instead of just labor,
machine and material … we are now also centrally concerned with packaging. How
much sense does it make to produce the goods in time when you lack the package to
send it to the customer?
PACKAGING OVERLOOKED
As we have discussed, an often overlooked requirement for this type of comprehensive
ERP system is fully integrated packaging management, which can also of course be
applied in other industry sectors. The demanding requirements of automotive supply
chains mean that packaging management is of intense concern, though. Logistical
processes depend more and more on the availability and proper handling of elements
necessary to bring the product to market—including packaging.
Supply chains in the automotive industry have four specific flow structures:
• Flow of demand
• Flow of goods
• Flow of money
• Flow of packing material
The flow of packaging describes packaging structures consisting of auxiliary and
main packaging, customer- or supplier-specific packaging structures, filling strategies
and structure-dependent labeling. Furthermore, it involves packaging management
with automatic account setup by goods disposal, processing of incoming reconciliation
information from the partners and automatic comparison between the packaging
material movements.
ERP challenge: packaging management
The packaging management complexity ERP must deal with in a sector like the
automotive industry is considerable. The starting point is the identification of empty
packages. In most cases, it is enough to typecast a package with generic descriptors
… a euro pallet, for instance, with specific dimensions and material. At this level,
uniform dimensions, reusability and quantity in stock can be managed. Sometimes, it
is necessary to individualize certain characteristics, such as exact weight, integration
into Kanban circuits, etc. so that the package can be identified even after several
cycles.
3WHAT ONE ERP FAILING COULD HAMSTRING YOUR AUTOMOTIVE LEAN INITIATIVE?
Of course packages are not only used individually, but also in combination as
complete packaging structures. In particular, predefined customer-specific packing
structures can become very complex. Besides the structure, which defines the number
of layers and sub-packages, the accessories also play an important role. Therefore,
rules within an ERP system must describe not only the product depending on the
degree of filling of the single package, but also the degree of filling of the layer with
full or empty packages. Labels help to identify the packages, and RFID (Radio
Frequency Identification) is gaining importance in many organizations for this
purpose.
Mixed packing in non-pure product containers is not only an issue for Just in Time
(JIT) or Just in Sequence (JIS). The reduction of the package volume is becoming
more and more important in nearly all areas to optimize the required transport
capacity. The number of possible package options is limited because the downstream
processes usually determine the possible alternatives of further packaging structures.
Sometimes, manufacturers face a variety of different demands connected to several
rules, and this increases complexity exponentially. For instance, there may be unique
packaging per article, per customer, per unloading point, per demand quantity etc.
This is challenging, and ERP must have the business rules and wherewithal built in
to handle very specific and diverse packaging structures.
Within IFS Applications, Packaging Aid provides basic data with technical, financial, stock etc. information. It can be
connected to an inventory part, so the relationship between the packaging and the part is reflected in the system.
4WHAT ONE ERP FAILING COULD HAMSTRING YOUR AUTOMOTIVE LEAN INITIATIVE?
FLOW OF GOODS AND FLOW OF PACKING MATERIAL ARE CLOSELY
CONNECTED
Each flow of goods entails a flow of packing material. Therefore, these two areas are
often closely intertwined from the product development standpoint. Together with
incoming goods, the received packages are already declared with the received delivery
notification. If the supplier can support the process, the relabeling and/or repackaging
are unnecessary. Once the goods are received from the supplier, each inventory
record is connected with the specific package structure and the degree of filling of
each handling unit is recognizable in the ERP system. In production, the empty
packages are delivered and labeled according to the package instructions within the
ERP system so that shop floor operations can be reported, for example by scan of a
barcode. It is possible to have customer-specific labels already in production to
streamline shipping to the correct customer location. The correct customer address
and destination is defined at the customer master document level, and flows all the
way to final packaging. So even if you have an order for 10,000 pieces from a single
customer, and that order is to be shipped to three different locations, that shipping
process is automated and you can meet or exceed customer expectations.
Within IFS Applications, Packaging Instruction provides customer- or supplier-specific instruction that can be used in
production or shipment.
5WHAT ONE ERP FAILING COULD HAMSTRING YOUR AUTOMOTIVE LEAN INITIATIVE?
THE PACKAGE FLOW MUST BE EXACTLY TRACKED
Customers oftentimes want clarification about what was shipped to them and when.
And ERP needs to allow you to track the used packages and to know where and
when they were sent. Within IFS Applications, for instance, this is done by the
management of empty and filled packages. Bilaterally-agreed package accounts are
set up in the relationship with business partners, which are then checked by periodic
exchanges of package statements and adjusted if necessary. ERP must support the
user to recognize imbalances between orders and shipments so difficulties can be
spotted and rectified. A well-designed package accounting system is therefore a
central point for advanced packaging management. Furthermore it helps to reduce
the annual packaging material inventory discrepancies.
ERP functionality that tracks the disposition of package material helps the user
to answer questions like, “when do I need how many packages,” and “what do I need
to do to meet those demands.” The demand flow already ensures the availability of
packages. The package requirements are determined by the material demand of all
production levels – and functionality that addresses this must take into account any
and all related package regulations. It needs to provide visibility into and facilitate
fulfillment of the demand of packages already packed goods (used package material)
and empty packages are considered. Also existing empty package requirements for
returnable packages (manually or automatically from a package cycle) or purchase
orders are available and support this process.
Within IFS Applications, ASC Shipment automatically generates the predefined packaging instruction. It an be changed if
necessary.
6WHAT ONE ERP FAILING COULD HAMSTRING YOUR AUTOMOTIVE LEAN INITIATIVE?
Furthermore different disposition methodologies support the order of one-way
packages. For returnable packages it must be defined whether the explicit creation of
empty packages should be set up or not. In this case, the suppliers must be provided
as business partners to identify an appropriate balance according to the related
package accounts.
THE WHOLE IS MORE THAN THE SUM OF ITS PARTS
As a result, the package material is established as an equivalent resource type along
other resources like labor, machines and materials, and must be considered as such.
ERP that does not encompass the flow of materials—all materials—does not deliver
on the promise of a unified enterprise environment. What is packaging but another
material essential to deliver a product? After all, “the whole is more than the sum of
its parts.”
Likewise, an ERP solution that has embedded packaging structure functionality
is greater than the sum of its parts. Unless ERP addresses packaging management, a
substantial and critical element of the business will be invisible to executives using
ERP … just as if a portion of the business has disappeared into a black box. This is
a core part of your product and ability to serve your customers in the automotive
industry.
Stefan Issing is the global director for automotive industries at IFS AB. Stefan holds a master’s
degree in computer science from the University of Wuerzburg. In his eight years with IFS, he
has been involved with automotive and supply chain management consulting, sales and
marketing, and presales for IFS Applications.
En
24
30
-1
P
ro
du
ct
io
n:
IF
S
Co
rp
or
at
e
M
ar
ke
tin
g,
N
ov
em
be
r 2
01
3.
ABOUT IFS
IFS is a public company (OMX STO: IFS) founded in 1983 that develops,
supplies, and implements IFS Applications™, a component-based
extended ERP suite built on SOA technology. IFS focuses on agile
businesses where any of four core processes are strategic: service
& asset management, manufacturing, supply chain and projects.
The company has more than 2,000 customers and is present in
50+ countries with 2,800 employees in total.
More details can be found at www.IFSWORLD.com.
For further information, e-mail to [email protected]
www.IFSWORLD.com
THIS DOCUMENT MAY CONTAIN STATEMENTS OF POSSIBLE FUTURE FUNCTIONALIT Y FOR IFS’ SOFTWARE PRODUCTS
AND TECHNOLOGY. SUCH STATEMENT S OF FUTURE FUNCTIONALIT Y ARE FOR INFORMATION PURP OSES ONLY
AND SHOULD NOT BE INTERPRE TED A S AN Y C OMMITMENT OR REPRESENTAT ION. IFS AND ALL IFS PRODUCT
NAMES ARE TR ADEMARKS OF IFS . THE NAMES OF ACTUAL C OMPANIES AND PRODUCT S MENTIONED HEREIN
MAY BE THE TR ADEMARKS OF THEIR RESPECT IVE OWNERS.
IFS AB ©2013
AMERICAS. . . . . . . . . . . . . . . . . . . . . . . . . . . . . . . . . . . . . . . . . . . . . . . . . . . . . . . . . . . . . . . . . . +1 888 437 4968
ARGENTINA, BRAZIL, CANADA, MEXICO, UNITED STATES
ASIA PACIFIC . . . . . . . . . . . . . . . . . . . . . . . . . . . . . . . . . . . . . . . . . . . . . . . . . . . . . . . . . . . . . . +65 63 33 33 00
AUSTRALIA, INDONESIA, JAPAN, MALAYSIA, NEW ZEALAND, PHILIPPINES,
PR CHINA, SINGAPORE, THAILAND
EUROPE EAST AND CENTRAL ASIA . . . . . . . . . . . . . . . . . . . . . . . . . . . . . . . . . . . . . +48 22 577 45 00
BALKANS, CZECH REPUBLIC, GEORGIA, HUNGARY, ISRAEL, KAZAKHSTAN,
POLAND, RUSSIA AND CIS, SLOVAKIA, TURKEY, UKRAINE
EUROPE CENTRAL . . . . . . . . . . . . . . . . . . . . . . . . . . . . . . . . . . . . . . . . . . . . . . . . . . . . . . . . . +49 9131 77 340
AUSTRIA, BELGIUM, GERMANY, ITALY, NETHERLANDS, SWITZERLAND
EUROPE WEST . . . . . . . . . . . . . . . . . . . . . . . . . . . . . . . . . . . . . . . . . . . . . . . . . . . . . . . . . . . +44 1494 428 900
FRANCE, IRELAND, PORTUGAL, SPAIN, UNITED KINGDOM
MIDDLE EAST AND AFRICA . . . . . . . . . . . . . . . . . . . . . . . . . . . . . . . . . . . . . . . . . . . . . . . .+971 4390 0888
INDIA, SOUTH AFRICA, SRI LANKA, UNITED ARAB EMIRATES
NORDIC . . . . . . . . . . . . . . . . . . . . . . . . . . . . . . . . . . . . . . . . . . . . . . . . . . . . . . . . . . . . . . . . . . . . .+46 13 460 4000
DENMARK, NORWAY, SWEDEN
FINLAND AND THE BALTIC AREA. . . . . . . . . . . . . . . . . . . . . . . . . . . . . . . . . . . . . . . +358 102 17 9300
ESTONIA, FINLAND, LATVIA, LITHUANIA