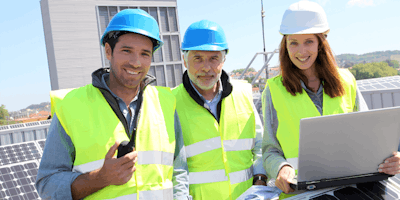
Epicor
M a r k e t M o n i t o r r e s e a r c h s e r i e s
Adapting to a
Multi-Generational Workforce:
Practical Tips on How to Evolve and Innovate
Within Your Manufacturing Enterprise
Presented by:
ANUFACTURING
sPonsored by:
M a r k e t M o n i t o r r e s e a r c h s e r i e s
2
Table of Contents
introduction .....................................................................................................................................3
section 1: What the state of the american Workforce Means for Manufacturing ..........................4
by the numbers .........................................................................................................................5
one size does not Fit all ..........................................................................................................6
section 2: best Practices for Fostering a culture of innovation across Generations .....................7
Utilize the talent you already have ...........................................................................................8
continuous education ...............................................................................................................8
collaboration is key ..................................................................................................................9
Flexibility Matters .......................................................................................................................9
section 3: Looking toward the Future ..........................................................................................10
M a r k e t M o n i t o r r e s e a r c h s e r i e s
3
Introduction
a major shift is currently taking place within the american workforce.
the good news is that americans are living longer now than ever before. While no one’s exactly com-
plaining about a national increase in life expectancy, it does lead to more complicated and unprecedent-
ed questions surrounding how this affects the workforce.
in short, this trend means that americans aren’t just living longer but also working longer.
the manufacturing industry is one of the first to experience this shift in workplace dynamics. the “skills
gap” conundrum that’s been so widely discussed the past decade or so supports this sentiment.
What’s less clear is how manufacturers are seeking to evolve to curb both short-term and long-term pain
points on the plant floor.
Manufacuring.net recently surveyed its readers to better understand
how manufacturers are seeking to adapt to an increasingly multi-gener-
ational workforce. specifically, we wanted to know how older and newer
generations of workers are being cross-trained simultaneously and how
this reflects manufacturers’ desire to both evolve and innovate within
their changing workforce.
according to our results, over half of survey respondents report be-
ing “very affected” to “somewhat affected” by this shift in workplace
dynamics. When readers were asked if their manufacturing enterprise
was “currently seeing a shortage of younger skilled workers entering the
workplace,” 50% answered “yes.”
this report takes a thorough look at these survey results and provides
a blueprint for manufacturers as they seek to cross-train and adapt to
a multi-generational workforce, while also creating a more efficient and
innovative enterprise.
Is your manufacuturing facility currently
seeking to cross-train both an older and
newer generation of workers?
Yes, all
employees
49.7%
Very affected
12.7%
Yes, just
younger
employees
15.0%
Not at all
affected
9.5%
Yes,
just older
employees
1.1%
M a r k e t M o n i t o r r e s e a r c h s e r i e s
4
Section 1:
What the State of the American Workforce Means for
Manufacturing
Look around your manufacturing enterprise. survey the plant floor closely, and what do you see?
if you’re anything like most manufacturers in the country, you’re seeing at least three or perhaps even
four generations of workers collaborating together toward a common goal: keeping your plant running
efficiently and effectively.
however, and as any experienced manager can attest, leading a multi-generational workforce is
complex, at best.
craig Mccollum agrees. as the executive Vice President of the americas for the business software
company epicor, he says that inter-generational tension is a common occurrence.
“one recent statistic shows that almost 70% of workers view the work
environment to be tense because of clashes between these two different
generations,” says Mccollum.
“the question is, how do we optimize the environment so it’s
conducive to both and, as a result, get them to engage and hopefully
be more productive?”
according to Manufacturing.net’s recent survey (as referenced above),
54% of respondents said that they were “very affected” to “somewhat
affected” by the shift in workplace dynamics within their manufacturing
enterprise.
additionally, a combined 64% of respondents said that their
manufacturing enterprise was “currently seeking to cross-train both
an older and newer generation of workers.”
before we delve into the operational challenges of adapting to a
multi-generational workforce that is simultaneously juggling
day-to-day production, let’s take a closer look at the scope of this
national workplace trend.
How affected is your manufacturing enter-
prise by this multi-generational shift currently
taking place in the American workplace?
Somewhat
affected
42.9%
Very affected
12.7%
Not very
affected
30.2%
Not at
all affected
9.5%
I haven't really
noticed
4.8%
M a r k e t M o n i t o r r e s e a r c h s e r i e s
5
By The Numbers
Four generations of employees working together under the same roof is common for manufacturers
across the country, especially for larger segments of the industry that employ 1,000-plus workers.
the number of americans working past the age of 65 is among the highest ever recorded and growing.
For example, the United states bureau of Labor statistics predicts that by 2020 around 22% of americans
over 65 will still be working.
additionally, a recent report from the Pwc says that Millennials will account for about 50% of the american
workforce as early as 2020.
however, the seismic shift occurring in the workforce isn’t just because older americans are working
longer. For decades, the national birth rate has also been in decline, which means our workforce is slowly
diminishing.
so, statistically speaking, when the older generations of workers do even-
tually retire, there won’t be as many educated, skilled young workers to
replace them.
this is a problem that has already affected a diversity of manufacturing
industries across the United states.
When asked if their “manufacturing enterprise was currently seeing a
shortage of younger skilled workers entering the workplace, 50% of
Manufacturing.net’s survey respondents responded in the affirmative.
although this shortage of skilled workers might not be as apparent on
every plant floor in the U.s., there’s no denying that manufacturers need
to be prepared to face this inevitable problem.
Whether you’re a manufacturing leader already in the crosshairs of this
issue or not, one thing’s for sure: it’s not a question of if or when you
need to act but how.
Is your manufacturing enterprise currently
seeing a shortage of younger skilled work-
ers entering the workforce?
Yes
50.0%
No
34.6%
I don't
know
15.4%
M a r k e t M o n i t o r r e s e a r c h s e r i e s
6
One Size Does Not Fit All
Millennials have a bad rap within the manufacturing industry. and, in the spirit of avoiding ugly “us vs.
them” stereotypes, it’s fair to say (and studies prove) that different generations of workers respond to
and are motivated by dissimilar sets of values.
although this paper isn’t designed to deal with strategies to recruit a younger workforce, the above point
regarding generational stereotypes and driving motivations is imperative when considering how to cross-
train and adapt to three or four generations of workers.
For manufacturing leaders and management, a simple awareness that differing
intricacies and contexts could affect any overarching workplace strategy is vital.
according to Mccullum, there is a definite awareness problem when it comes to
forming a well-formed workplace management and training plan.
“We need to make a concerted effort to make sure there is an awareness of what
being a part of any manufacturing company actually means, and the value that it
brings to customers,” says Mccullum.
so, while the old maxim “one size does not fit all” is vital, what’s equally signifi-
cant is that each team leader, general manager and ceo stay consistent in their
approach to engaging and collaborating with a multi-generational workforce.
“We need to
make a concerted effort
to make sure there is
an awareness of
what being a part of any
manufacturing company
actually means,
and the value that it
brings to customers.”
M a r k e t M o n i t o r r e s e a r c h s e r i e s
7
Does your manufacturing enterprise offer training
and development opportunities, schooling reim-
bursements or any on-the-job learning initiatives?
Section 2:
Best Practices for Fostering a Culture of Innovation Across
Generations
Manufacturing thrives on innovation; in fact, consumers demand it.
For manufacturing industries to stay relevant, any enterprise’s workforce needs to be primed and ready
to collaborate across generations, contribute to the company’s mission and be the driving force behind
those “next big ideas.”
First, however, managers need to “future-proof” their organizations by creating positive work environ-
ments for workers across generations.
in Manufacturing.net’s reader survey, 40% of respondents said that their company wasn’t “doing enough
to foster positive relationships among its multi-generational employees.”
below are some best practices for manufacturers seeking to better adapt to their multi-generational
workforce while simultaneously fostering a culture of innovation.
The Top Reasons Why Some Manufacturers Fail To
Implement Mentorship Or On-Site Training Initiatives
1 Companies don’t have the time or management
required to buid these types of programs
2 Wouldn’t improve overall job satisfaction or
employee retention
3 Don’t feel programs are necessary within their
manufacturing enterprise
4 Belief that these programs are ineffective
5 Lack of desire
Yes
76.8%
No
18.4%
I don't
know
4.9%
M a r k e t M o n i t o r r e s e a r c h s e r i e s
8
Utilize the Talent You Already Have
Mentorship and peer training programs are focused and relatively simple ways to engage all generations
of workers within a plant or factory.
however, this is one effective tool that manufacturers have yet to utilize and implement within their work-
space.
according to Manufacturing.net’s survey respondents, only around 40% said that their manufacturing
enterprise offered any sort of mentoring program.
regarding mentorship programs, Mccullum says, “try to take the folks who have extensive and deep
domain expertise in a given area.”
“Match them up with someone who is coming in – who’s probably more tech savvy and innovative – and
have them work together so they both see the value the other person brings.”
Continuous Education
another tool that could be utilized, depending on the size and space of the specific company, is the
development of on-the-job learning initiatives.
although most manufacturing facilities offer some form of continuous learning, school reimbursements
or even mentorship programs, multi-generational workers (especially younger and less skilled employ-
ees) still require the encouragement to make participating in these opportunities a priority.
in fact, 76% of Manufacturing.net readers said that their “manufacturing enterprise offered training and
development opportunities, schooling reimbursements or on-site learning initiatives.
additionally, a whopping 92% of respondents said that mentorship programs or other employee training
and learning initiatives were important to their company’s long-term health.
M a r k e t M o n i t o r r e s e a r c h s e r i e s
9
Collaboration is Key
as mentioned above, one common mistake most manufacturers make is failing to utilize the talent pool
they already have.
by actively choosing to harness the collection of skilled minds already at your disposal, the chances of
driving innovation and success from the plant floor increase exponentially.
Find creative ways to get your multi-generational workforce to collaborate, collectively address efficiency
or production problems and solve them.
When asked if their manufacturing enterprise saw any improvements or benefits from training initiatives
or mentorship programs, the number one response was “improved communication across the work-
force.”
other benefits included, “boosted employee morale,” “improved employee retention” and “improved
engagement across the enterprise.”
Flexibility Matters
technology is a driving force behind changes on the plant floor but also behind innovation.
With a wide diversity of workers in your facility (age not being the least among them), there’s something
to be said for some degree of flexibility in the overall management of a workforce.
even if resistant to change in the day-to-day plant floor operations,
employers and management leaders need to take advantage of new
technology at their disposal.
consider making use of apps recommended by the more digitally
adept members of your team. engage in at-home conferencing,
email and other content-management sites that might enable you to
appeal to part-time or contractual employees.
The Top Reasons Why Some Manufacturers Fail
To Implement Mentorship Or On-Site Training
Initiatives
1 Companies don’t have the time or management
required to buid these types of programs
2 Wouldn’t improve overall job satisfaction or
employee retention
3 Don’t feel programs are necessary within their
manufacturing enterprise
4 Belief that these programs are ineffective
5 Lack of desire
M a r k e t M o n i t o r r e s e a r c h s e r i e s
10
Section 3:
Looking Toward the Future
adapting to a multi-generational workforce is a challenge that demands patience and, more than likely,
some degree of trial and error.
remember that context matters. no plant floor is the same, nor are the generations of employees who
work to keep it functioning with efficiency and care.
connectivity in any manufacturing enterprise isn’t just limited to the internet of things; perhaps even
more importantly, manufacturing leaders must work to create the kind of employees they want.
the ideal worker will likely never just walk onto your plant floor, and a magically aligned and motivated
workforce of multi-generational employees won’t appear out of thin air.
however, if manufacturers choose to adapt their workplaces and take advantage of the tools at their
disposal, they can then train workers to do more than meet the status quo. in fact, the opportunity is
there to train workers to be innovators.
0 5 10 15 20 25 30 35
Boosted employee morale
Created a more symbiotic relationship within the manufacturing enterprise
Fostered a more innovative workplace environment
Improved communication across the workforce
Improved efficiency
Improved employee retention
Improved engagement across the enterprise
Improved overall workplace environment
I have not seen any improvements
N/A My company doesn’t offer any
Have you seen any improvements/benefits from training ot mentorship initiatives
offered at your company? (Check all that apply)
29.3%
20.7%
24.5%
33.0%
27.7%
26.6%
23.9%
28.7%
17.0%
19.2%
M a r k e t M o n i t o r r e s e a r c h s e r i e s
11
Market Monitor Research Series:
advantage business Media’s Market Monitor research series presents fresh research and analysis on
compelling and timely industry topics. “Adapting to a Multi-Generational Workforce: Practical Tips on
How to Evolve and Innovate Within Your Manufacturing Enterprise” was prepared by Manufacturing.net
editor abbey dean. the data presented in this report is based on the results of a survey of Manufactur-
ing.net subscribers, comprising of ceos, presidents, owners, engineers, managers, and directors across
the manufacturing industries.
About Manufacturing.net:
Manufacturing.net has served as a leading resource for manufacturers for the past 30 years, and its
longstanding readership in the manufacturing marketplace makes it a respected source on the latest
technologies. Manufacturing.net is a prime information source for decision-makers in operations,
information technology, automation, and the supply chain.
For more information visit
www.manufacturing.net.
About Advantage Business Media:
advantage business Media (www.advantagemedia.com) is a data-driven marketing solutions company
leveraging content, technology, and business intelligence to match its audience’s job performance needs
with its clients’ solutions. With a diversified portfolio of highly focused websites, e-newsletters, print
publications, specialized directories, vertical search databases, conferences, ancillary media vehicles,
and associated web-based services, advantage serves more than one million industry professionals in
the manufacturing, science, and design engineering markets.
For more information visit
www.advantagemedia.com.
©copyright 2016, advantage business Media. all rights reserved.