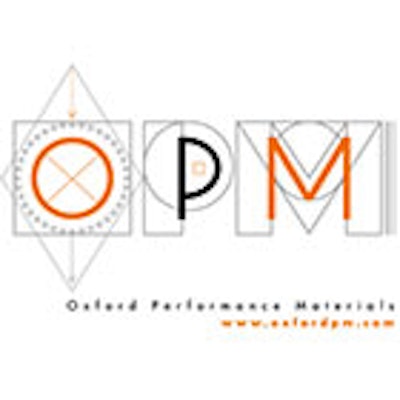
SOUTH WINDSOR, Conn. (GLOBE NEWSWIRE) -- Oxford Performance Materials Inc. (OPM) has announced the launch and availability of the first two grades of its OXFAB 3D printing technology for aerospace and industrial applications – OXFAB-N and OXFAB-ESD. OXFAB is OPM's proprietary technology platform and formulation of poly-ether-ketone-ketone (PEKK), an ultra-high performance polymer with exceptional strength, chemical resistance, low and high temperature performance, radiation resistance, superior wear properties and ultra-low outgassing – all of which are critical to aerospace and industrial applications.
OPM Aerospace & Industrial utilizes OXFAB technology to deliver lightweight, high performance, cost-competitive, 3D printed thermoplastic parts for commercial and military aircraft, spacecraft and other industrial markets, including the transportation, energy and semiconductor sectors. The company's additive manufacturing technology produces very complex parts that equal the performance of a range of traditionally manufactured aluminum and composite components at lighter weight and reduced cost.
OXFAB-N is composed of unmodified neat PEKK, a best-in-class material with a very low microwave dielectric constant and is well suited for radomes and other unique electrical applications. OXFAB-ESD is a carbon filled PEKK compound with superior mechanical properties well-positioned for demanding structural applications in the aerospace and industrial markets. OXFAB is a robust and repeatable production process with other advanced material grades currently under development to meet unique market requirements.
"We believe that OXFAB will fundamentally improve the way the world's aircraft and industrial components are manufactured," said Paul Martin, President of OPM Aerospace & Industrial. "OPM's OXFAB products are ideally suited for end market applications where functional complexity and weight reduction can have a substantial and positive impact on performance, while also yielding cost and energy savings – creating sustained value for our customers."
Martin added, "While additive manufacturing with commodity polymers has been taking place for some time now, this is the first time PEKK is being used for 3D printing in aerospace and industrial applications. Supported by extensive mechanical test data, PEKK is the highest performance thermoplastic available for 3D printing fully functional, end-use parts and components. We are fulfilling critical development contracts for 3D printed parts in a range of applications in commercial and military aircraft, space and industrial products to deliver significant weight and cost savings – a central focus and benefit for our aerospace and industrial customers."
"OXFAB's strength to weight ratio is superior to that of cast aluminum, magnesium and nylon," said Larry Varholak, Vice President of Programs, OPM Aerospace & Industrial. "Due to its inert behavior, OXFAB is highly chemical and heat resistant with the ability to tailor electric properties, which is critical for high-performance aerospace and industrial parts."