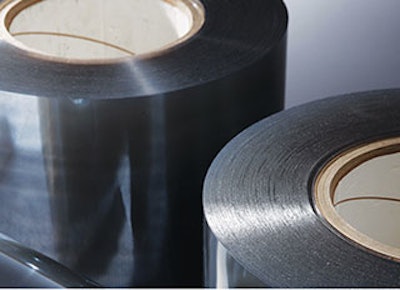
[[{"fid":"160763","view_mode":"media_original","type":"media","attributes":{"height":232,"width":320,"style":"float: right; margin-left: 5px; margin-right: 5px; border: 1px solid black;","alt":"New DPET Process","title":"New DPET Process","class":"media-element file-media-original"}}]]The new, unique, direct-to-sheet (DPET™) process as used by PET producer OCTAL (Dallas, TX) eliminates five energy-intensive stages of the conventional sheet production process (pelletizer, SSP, compactor, dryer, and extruder), says the company. Through this methodology, PET melt can arrive at the calendar stack heated to the proper temperature and therefore does not have to be dried and re-melted from the granular form. It ensures a finished polymer that is fully devoid of moisture and all moisture-related defects. Furthermore, there is absolute traceability as the resin is constrained to one source, providing origin of the resin and quality. The uniformity of the sheet has allowed OCTAL to design a winder that constructs precision rolls with unnoticeable weave and near perfect formation. This minimizes side trim requirements at the thermoformer, providing a direct material savings.
See more at www.octal.com.