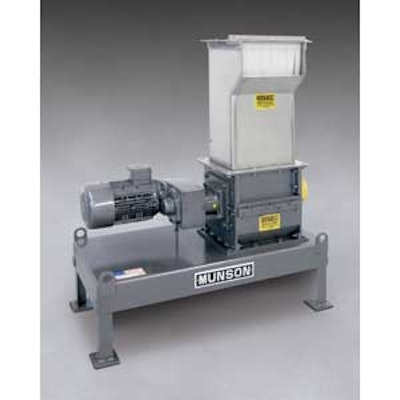
title
Munson Machinery introduces its SCC-15-SS high-torque, low-speed screen classifying cutter to reduce hard materials and friable products into controlled particle sizes. The company believes that this cutter is also characterized by:
- A rotor comprised of cutter bits (which are attached to a helical array of staggered holders called “interconnected parallelograms”) that continuously cut and crush oversize materials against twin stationary bed knives.
- A direct-coupled, gear-reduced drive that rotates the shaft at speeds down to 10 RPM to cut or crush tough materials using low shear, and/or to minimize fines when cutting friable materials.
- Positioning of the bits along the entire shaft, with no frontal gaps, to reduce material into uniform pieces with minimum imperfections or fines, and little to no generation of heat.
- Cutter bits, which are available in stainless steel, tool steel and tungsten carbide, that can be slid onto holders and secured with 1 retaining socket-head screw to facilitate rapid replacement.
- Perforations of the bed screen ranging from 1/32 to 1-1/2 inches (0.79 to 38 mm) in diameter and up to 3 inches (76 mm) square, permitting the reduction of materials into uniform particles in sizes from 20 to 30 mesh.
- Material fed through the top of an adjustable double-baffled intake chute or directly into the front of the chute through a hinged door.
- A 15-inch (381-mm) throat width on the cutter that accommodates up to 30 parallelograms with 60-bit inserts.
- An independently powered variable-speed pinch roller for horizontal feeding of material.
- Discharge via gravity, pneumatic transition, or an independently powered belt or screw conveyor.
- Suitability for a diversity of chemical, mineral, foundry and plastics materials.