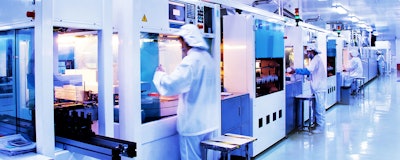

Bringing jobs back to America has been a hot topic of discussion and debate in U.S. news cycles since President Trump began his campaign for office, and one of particular interest in the manufacturing space. While statistics vary, the idea that manufacturing industry employment has been on the decline for many years is undisputed. In fact, according to a CNNMoney article, since 2000, the U.S. has shed 5 million manufacturing jobs.
While these numbers are sobering, they only tell part of the story. From trade agreements to global wage disparity, there’s still plenty left up to interpretation as to the reason behind the decline. For instance, globalization and increased competition have driven many U.S. manufacturers to relocate jobs to lower labor cost countries. In addition, accommodating U.S. trade policies, high corporate tax rates, and an emphasis on lower unit purchase costs by supply chain professionals have also contributed to the decline.
Reversing the Trend
Despite these hurdles, there is some good news on the horizon as the manufacturing industry has started to show signs of investment and potential growth. Several studies and surveys, for example, have begun to suggest that the trend of offshoring is slowing and potentially reversing. And the Trump Administration has presented numerous policy proposals that seek to promote job growth in U.S. manufacturing. I doubt it’s a coincidence that quite a few companies, including General Motors and Bayer AG, recently announced plans to invest billions in U.S. factories and new jobs.
While this news definitely brings promise to the U.S. manufacturing economy, we aren’t out of the woods yet. It’s critical we ensure these reinvestment plans are not just isolated examples, but rather are more reflective of a renewed focus on domestic manufacturing growth.
Based on my experience in leading and building successful U.S. middle-market manufacturing firms, I believe there are three critical success factors necessary to drive growth and competitiveness in U.S. manufacturing:
- Claim the industries where we can create jobs and grow the economy
- Strengthen the integration between design and manufacturing, and focus on innovation and speed as differentiators
- Build a skilled careers workforce that meets the need of the new manufacturing economy
Let’s take a moment to dig deeper into the current state of each and determine next steps moving forward.
Staking Our Claim
In order to create jobs and grow the economy, the U.S. needs to finds its niche and identify where we can succeed in today’s global manufacturing environment. This means owning industries that do not require highly labor intensive processes and, thus, cannot be at least partially automated.
For this reason, we need to focus on areas with higher skill requirements, where unskilled labor is a smaller cost component of the overall product. This can involve the integration of automation where possible, reducing the reliance on unskilled labor while playing into the strengths of skilled laborers.
In fact, with increasing automation, the manufacturing industry is becoming more productive. From 1998 to 2012, all sectors experienced a productivity growth of 32 percent when adjusted for inflation — the production of computer and electronic products rose 829 percent. In addition, Ball State University researchers calculated that if 2000-levels of productivity are applied to 2010-levels of production, the U.S. would have required 20.9 million manufacturing workers instead of the 12.1 million actually employed.
By shifting focus to skilled laborers, we’re able to more greatly utilize robotics and shop floor automation, increase MTM technologies for heightened throughput and efficiency, and concentrate on industries and processes where direct labor content adds significant value to the product. Doing so drives job creation and economic growth while establishing a strong foundation for the re-emergence of manufacturing.
Tightly Integrate Design and Manufacturing
Another success factor in driving growth and competitiveness in U.S. manufacturing is to unify the design and manufacturing process. Many companies still tend to approach these stages as two separate processes, but our experience has shown that the companies who link these processes consistently meet speed-to-market objectives.
Elongated supply chains, coupled with other time and space challenges, make collaboration difficult, particularly on highly engineered products due to the number of components involved. In fact, according to a 2015 BCG survey, overly long development times were the most-cited obstacle to generating returns on innovation and product development; 42 percent of global innovation executives said development times are too long — a 6 percentage point increase over 2014.
But there is good news for innovative companies who master the early integration of manufacturing considerations: they benefit from drastically improved design, speed-to-market and quality. Specifically, manufacturability concerns that can be addressed early in the design cycle greatly increase the likelihood that cost and pricing parameters on a product can be met without unnecessary delays in launch.
Building a Skilled Careers Workforce
If predictions hold true, manufacturing jobs are returning to the U.S., but of the estimated 3.5 million manufacturing jobs needed, 2 million will go unfilled because of a skills gap. That’s in addition to the 80 percent of manufacturers who currently report a moderate or serious shortage of qualified applicants for skilled and highly-skilled positions.
In my opinion, our primary challenge is that today’s environment solely focuses on the importance of a college degree while neglecting the importance of trade/skill education. This creates an even bigger problem when you look at the current trade workforce, as about 53 percent of the workforce is over 45. With Baby Boomers making up over 50 percent of the skilled labor workforce, this market is going to be ripe with jobs, but short on qualified applicants.
The good news is that only 66 percent of high school graduates go to college, suggesting we have an untapped market for skilled labor. Given this, it’s critical we stress the importance of skilled labor, especially among the younger generations. This translates into foregoing a college education in favor of attending a trade school for a specialized degree.
Doing so will not only help the industry attract, train and retain talent who may not have previously considered such a career, but also meet the needs of the new manufacturing economy.
Keeping America Competitive
Over the last several months, it’s been encouraging to hear discussion of ideas that promote growth in U.S. manufacturing and, more importantly, to see action on ideas that are driving investment and employment in the sector. The three success factors mentioned above are critical to ensuring U.S. manufacturing remains competitive while still staying true to our long-term commitment to free and fair trade.
If we work together to strengthen the industry and the workforce, we’ll re-establish manufacturing as an integral industry in the American economy.
Greg Chesnutt is president and CEO of Prime Technological Services.