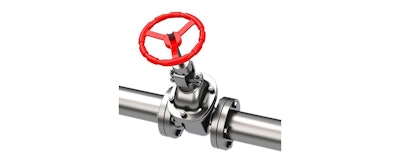
Several things need to be considered when choosing a valve for a specific application. At times, this can make valve procurement a confusing and time-consuming process. While valve procurement can be confusing and time-consuming at times, you can make selection easier by understanding the application requirements and then finding a suitable valve that can fulfill them.
Choosing the correct valve for your application is important because it can help you to maximize the function and outcome of your system. A useful component, valves help to limit, control or a shut-off flow in a system. While no one can deny the importance of valves, choosing the right valve for your need can be tricky.
With so many valve types, sizes, and construction materials to choose from, selecting the right valve for your application can be confusing, to say the least. However, you can better your odds of finding the right valve for your specific needs with the following best practices for valve procurement.
Best Practice No. 1: Understand the Different Types of Valves and What They are Best For
If you want to procure the right valve for your needs, then a good way to start would be understanding the different types of valves and what they are best for. While many different types of valves are manufactured today, we will discuss only the most commonly used ones. Used in a variety of applications, the following are the most common valve types and their best uses.
- Gate Valves—Simple on-off valves, gate valves allow or block flow in a system through a sliding ‘gate’ mechanism. Considering their function, gate valves are best suited for materials that flow in a straight line. They are also useful for isolating a part of the system. Some popular uses for this valve type include fibrous suspensions, neutral liquids, corrosive liquids, and lubricating powders.
- Ball Valves—While they have the same on-off function as gate valves, ball valves use a ball structure through which channels pass. The channels allow fluid to pass through when the ball is rotated. Rotating the ball also causes the channels to block the flow. This valve type has the same uses as gate valves.
- Butterfly Valves—Valves that can be used for regulating or shutting off flow, butterfly valves allow fully shutting off flow or restricting flow by keeping it partially open. A butterfly valve is mostly used for its seating surface and flow isolation.
- Check Valves—Also known as a non-return valve, check valves constantly keep the flow of fluid in one-direction to stop back-flow in the piping. A major advantage with check valves is that they can be operated automatically. Check valves come in many different forms. However, the most common types are swing check valves and ball check valves.
- Plug Valves—Having an on-off function, plug valves use a cylinder with channels and are rotated like a ball valve to operate. Their uses are also identical to ball valves.
- Diaphragm Valves—Also known as membrane valves, diaphragm valves can be moved up and down to allow or block flow. In addition to having an on-off function, diaphragm valves allow you to regulate/control flow by keeping it partially open.
While the valve is being used, only the diaphragm is exposed to transient materials. This means that the valve can be used in applications which require a non-contaminating environment. Examples of this are food, beverage, and pharmaceutical industries. However, these valves can also be used for fibrous suspensions, neutral liquids, corrosive liquids, and lubricating powders
Best Practice No. 2: Determine Suitable Materials of Construction
Once you have decided on a type of valve for your application, the next step would be choosing an appropriate material of construction. The most important thing in this regard would be determining the chemical compatibility requirements. This means that materials used for constructing the valve need to be compatible with the liquids or gases that flow through it. You can choose from plastic, brass, and stainless steel. To determine the chemical compatibility requirements, you can look up a chemical compatibility chart for valves available online.
Best Practice No. 3: Understand Performance Requirements
One of the most important steps in the procurement of valves is determining your temperature and pressure requirements. Find out the ranges for both where the valve will be installed. Generally, metal valves such as stainless-steel valves are better equipped to handle extreme pressures and temperatures than plastic valves. They are also a great option for pressurized gases. However, the point is that you need to choose a valve that can easily handle your temperature and pressure requirements. Go for nothing less.
Best Practice No. 4: Determine the Need for Ongoing Maintenance
One of the key things that many procurement teams fail to consider when sourcing valves is the need for ongoing maintenance. Like any other component, valves require maintenance from time to time. However, the frequency of maintenance varies from valve to valve. Therefore, decide how frequently you can maintain the valves before sourcing a valve for your application.
Often, it can be difficult for procurement teams to find a suitable valve for a specific application. However, using the above best practices for procurement of valves can make selection easier at the very least.
Ismail.Y. Bhola (Director) is a procurement leader and consultant. Using a sustainable and effective approach to procurement, he has delivered the best products and cost savings to the company he has been associated with. Currently, Bhola is applying his procurement expertise and knowledge to bring cost and revenue benefits to SealExcel.