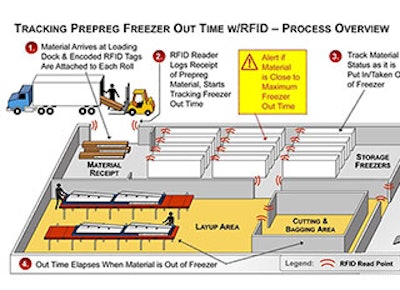
Within the aerospace and defense segment, four trends are driving the adoption of RFID to achieve improved process automation, efficiency and traceability. These include an upward trend in aircraft manufacturing, the use of advanced composites and additive manufacturing, a greater interest in traceability by aftermarket logistics/MROs, and an increased focus by CFOs on capital asset inventory.
Aircraft Manufacturing
Despite a varying economy, we are seeing a consistent upward trend in aircraft manufacturing, the only defense sector to show consistent growth during the recession. With that have come large-scale aircraft projects that require additional resources and more tightly managed processes, as stakeholders demand transparency throughout the program, not just at program completion, to mitigate risk.
As new aircraft are developed, money is pouring into research & development programs, new manufacturing plants, processes, materials, equipment, etc. Because the stakes have never been higher, there is increased scrutiny on Tier 1 and Tier 2 suppliers by OEMs to provide more transparency, showing details about every step in the work process, because serious delays or mistakes can result in lost contracts. In fact, many OEMs now have representatives onsite at suppliers’ plants full time.
In effect, we now have customer-facing processes in manufacturing plants. This mean that there’s nothing to hide — for a helicopter manufacturer that provides custom variations like medical equipment for EMS services, or specialized avionics, there’s no component substitution. End customers are increasingly requesting visibility into work-in-process, well before a product is scheduled for final assembly and delivery. Precise work order tracking with RFID helps keep work orders on schedule, locating and pre-staging raw materials, components, tooling and conveyances prior to each process step, and providing WIP visibility to the end-customer. This also provides cost savings for the manufacturer, since on-time delivery helps prevent rework, discounting and contract issues.
Advanced Composites and Additive Manufacturing
We are also seeing an increased use of advanced composites and additive manufacturing. These new or retooled manufacturing processes have required higher levels of predictability and transparency. In addition, there is a higher level of scrutiny from OEMs, including more frequent audits and an increased emphasis on quality and safety, and operational risk.
Manufacturers increasingly use advanced composite materials for their light weight and fuel efficiency. These new materials create a mini process manufacturing environment within a discrete manufacturing operation, since they require completely different assembly processes, materials management and tooling. An aero structures manufacturer has begun automatically tracking perishable composite material with RFID to reduce material costs and quality risk. It uses composite prepreg (pre-impregnated composite fibers), a perishable material that must be transported, stored and monitored at sub-zero temperatures, for fabricating curved structural components. Prepreg must be discarded once it has been out of the freezer beyond a rated time (usually 350-400 hours), and tracking out time is time-consuming and error-prone, often leading to any questionable material being discarded as scrap.
On the additive manufacturing side, 3D printing is being used to enable manufacturers to machine more quickly and to exact specifications. The use of 3D printing has brought about the use of perishable polymers that require specific handling. RFID has been used here to track materials, reduce product use and ensure the quality of polymers used.
Focus on Traceability
Third, aftermarket logistics/MROs have a greater focus on traceability. As more MRO firms consolidate and more aircraft models/variations enter the market, inventory management of spares becomes more daunting. There is a greater need for documentation to be standardized to ensure part traceability and greater emphasis on quality and safety, as well as focus on operational risks.
With airline consolidation has come a more complex mix of aircraft models, configurations and component parts to maintain. Unlike newer, Low Cost Carrier (LCC) airlines that standardize on only a few aircraft, airlines that inherit aircraft seldom obtain the same models already in service. This means that when new aircraft are added to the mix, airlines may need to double or even triple the number of spare parts and tracking histories of aircraft and associated parts. Being able to track diverse mission-critical components that are in inventory can have a major impact on flight turnaround.
Moreover, overhauling engines is, in effect, rebuilding them — a classic manufacturing process. For engine overhaul, MROs increasingly use sophisticated manufacturing facilities, where they need to track work in process for each part and maintain traceability to understand when an engine was last serviced, what individual components comprise the engine, if there are any recalled parts, etc. Imagine the size of a log book that tracks the history of a 30-year-old engine. Tracking this information via RFID versus manual methods can be an enormous time and money saver.
Capital Asset Scrutiny
And finally, there has been increased CFO scrutiny on working capital allocation. Billions of industry dollars are spent on work-in-process, redundant inventory and non-working equipment in capital manufacturing. With this comes an opportunity to increase asset allocation by automating inventory management and maintenance cycles. CFOs are putting capital asset inventory under scrutiny since working capital allocation is a prime component of operating profit.
RFID can have an impact on every aspect of working capital performance, from optimizing inventory of raw materials and finished goods to informing performance metrics. An Accenture study found that although most working capital reduction programs were focused on the financial side (extending payables, getting aggressive on receivables), the lasting improvements came from operations transformation and process improvement, which can all be automated with RFID.
Consider the costs of aircraft or even parts. A Boeing 737 may cost upwards of $30 million while a single rotor blade on a helicopter can cost $1 million or more. Aircraft are typically built in different facilities with separate inventories of equipment and supplies, so factoring in capital costs for composites, tools, paint, etc. mean enormous monetary outlays. And with materials filling each warehouse, it isn’t surprising that expensive parts may go missing, there is redundant inventory or that half-built aircraft are further disassembled to finish others that may be missing parts.
In other cases, parts may be shipped between facilities and if there isn’t enough time to receive parts properly or they don’t match what was expected (or aren’t high priority), they go into quarantine, where they may be added to other parts piled to the ceiling — because no one can remember what they were meant for. These examples of poor inventory allocation are the sort of things that create unhappy CFOs, who want only to use or write off capital assets. By automating part movements with RFID, deliveries are automatically scanned and verified against shipping manifests, and employees are alerted only for exception handling.
The advent of these four trends has brought forth new challenges for aircraft OEMs and their suppliers. But through the use of RFID, experience has shown that they can achieve improved process automation, efficiency, traceability and cost savings.
Su Doyle manages Industry Programs at OATSystems a division of Checkpoint Systems. She can be reached at [email protected].
To read more manufacturing and technology news, sign up for our newsletter. You can also follow Manufacturing Business Technology on Twitter @MBTwebsite.