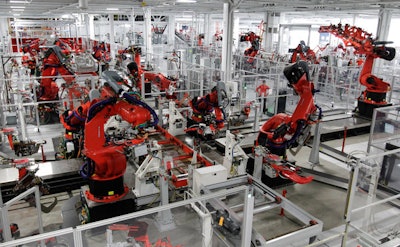
Manufacturing has changed drastically in the past decade, and much of this change is due to advancements in technology. Here is a look at a few of the technologies that are having the largest impact.
Government-funded manufacturing hubs
One of the most impressive changes in manufacturing is the renewed awareness of government officials and economists that manufacturing is the real engine behind a robust economy. President Obama has commissioned and funded various manufacturing hubs around the country to focus on advancing the state of the art in manufacturing and many new and promising manufacturing techniques.
The manufacturing hubs are consortiums of private businesses, public officials and university-led researchers all focused on a particular promising manufacturing technology. To date, several manufacturing hubs have been opened, including:
- The National Additive Manufacturing Innovation Institute in Youngstown, Ohio
- The Next Generation Power Electronics Manufacturing Innovation Institute at North Carolina State University
- The Lightweight and Modern Metals Innovation Institute in Detroit, Michigan
- The Digital Manufacturing and Design Innovation Institute in Chicago, Illinois
- The National Network for Manufacturing Innovation which oversees general manufacturing research
These institutes are spread across the country and serve as centers of excellence for manufacturing innovation. In addition, these institutes are helping to increase the respect for manufacturing as an industry and a profession while advancing the underlying technologies.
Additive manufacturing mania
Additive manufacturing, also known as 3-D printing, has been gaining a majority of the publicity devoted to manufacturing over the past year. From appearances on popular television shows to packed booths at trade shows, 3-D manufacturing has captured the imagination of manufacturing professionals and the general public.
Far from being a novelty, 3-D printing is proving itself to be a true game changer. No longer relegated to printing ungainly plastic components, 3-D printing has rapidly evolved to the point where it can produce items made of metals, mixed materials and even human tissue. The result is shorter lead times, improved quality because of fewer components, reduced waste and the ability to produce complex shapes without complicated machining. Additive manufacturing is causing changes in the way engineers and designers think about creating products and components, and it is changing the way we will educate and train future generations.
Cold spray improves longevity of parts and equipment
While 3-D printing gets most of the press, another additive manufacturing process known as cold spray, or “3-D painting,” is shaking up traditional manufacturing as well. Cold spray involves pushing metal powder through a nozzle under pressure. Cold spray can be used to create parts from scratch or to apply coatings to traditionally formed items, but one of the most interesting uses is to repair or refurbish used components by filling in worn spots using materials that meet or exceed the original material specs. This repair process can extend the life of machinery and equipment, tooling, dies and components by years. Restoring worn items using cold spray results in greater return on investment, less downtime, faster return to production for down equipment, and overall longer mean time between failure or necessary replacement.
Nanotechnology
While nanotechnology doesn’t have its own government-sponsored innovation institute yet, it does have a government-funded initiative and it is one of the most interesting technologies to come along in years. These tiny machines have been enlisted for such diverse purposes as delivering cancer-fighting medications directly to the site of a tumor, repelling stains on clothing, and extending the life and efficacy of lubricants. Long the subject of science fiction, nanotechnology is coming into its own and reaching the stage where results are repeatable and commercially viable.
IoT
IoT, otherwise known as the Internet of Things, is the growing ability for devices to communicate automatically with one another over the Internet without requiring input from people. This new communication ability has been the subject of late-night gags about the refrigerator calling its own repairman, but in reality IoT is having a profound effect on manufacturing.
Equipment now monitors its own status and not only notifies repair and maintenance teams when regular updates or PMs are due, it also continually checks its own performance and calls for repairs or recalibration when it notices reductions in its efficiency or throughput.
Sustainable manufacturing initiatives
Many manufacturers are trying to reduce their carbon footprint as well as energy use and overall environmental impact. These forward-thinking manufacturers work continuously to educate the industry on sustainability, innovative technology and best practices that produce high-quality, cost-effective products with less damage to the earth’s delicate ecosystem.
While these are not the only manufacturing technology trends that are changing the face of manufacturing, they are some of the more interesting and impactful trends. Taken as a whole, they show that the manufacturing industry is one of the most innovative areas as well as a strong driver for the economy. Watching these trends evolve and other innovations emerge will prove interesting over the next several years.
Christina Chatfield is the Marketing Communications Manager for HARTING USA (www.harting-usa.com) in Elgin, IL. HARTING Technology Group develops, manufactures and sells products such as electronic and electrical connectors and cables for your specialized manufacturing needs.
To read more manufacturing and technology news, sign up for our newsletter. You can also follow Manufacturing Business Technology on Twitter @MBTwebsite.