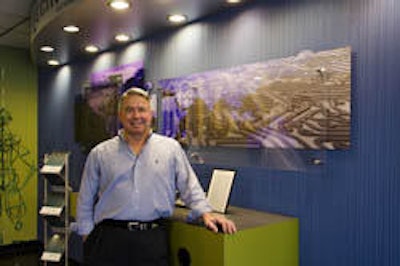
Founded in 2002, Saline Lectronics, Inc. is a printed circuit board (PCB) contract manufacturing firm located in Saline, MI that services a wide variety of clients in the medical, after-market automotive, aerospace, military, and oil and gas industries. It provides the latest manufacturing expertise including THT, SMT, BGA, microBGA, and different bottom terminated component capabilities, as well as other challenging mixed-technology assemblies.
Saline Lectronics specializes in mid-volume, high-mix electronics PCB assemblies that require thorough process and documentation control, as well as challenging opportunities for the production team. In addition to manufacturing, Saline’s other strengths include electromechanical assembly, design for manufacturing, project engineering, and new product introduction including the prototyping lifecycle.
With a strong emphasis on quality and customer service, Saline’s goal is to exceed customers’ expectations throughout the assembly process.
Q. Mario, we understand that you are expanding your state-of-the-art 110,000 ft2 static-controlled facility. Please tell us about the current expansion taking place on the production floor?
A. Even with the current economic climate, we have been quite fortunate over the last couple of years to continue growing — and even exceeding — our sales goals. To maintain the influx of consistent demand, it was pertinent to expand our facility to accommodate our customers’ requirements. We are not only allocating more space to crucial manufacturing areas such as surface mount and test engineering, but we also are expanding our mechanical assembly area to fulfill the increased demand for completed box builds. Many of our customers have chosen Saline to complete their pack-out requirements, so instead of manufacturing only the PCB, we actually build all the way to the completed unit with various housing, cable, and boxed requirements.
Q. As part of the expansion, you have added a FlexSolder W510 from Juki Automation Systems. The W510 marks the third selective soldering system in your facility. How have you benefited since the installation?
A. The new FlexSolder machine allows greater flexibility to our production demand. Generally, the selective soldering process is much more customizable to various assembly requirements, more so than the wave solder process. Many of the assemblies that we manufacture require selective soldering because of the specific components used on the boards, and this third selective solder machine allows us to accommodate those needs simultaneously without slowing the production process. The FlexSolder W510 is the latest in selective soldering technology and has improved our accuracy and throughput volume significantly.
Q. You also installed a new FX-3XL from Juki that is part of your second high-speed line. Tell us about the increased speed you have realized in the line with the newest addition?
A. The new high-speed FX-3XL from Juki allows us to process kits at faster rates than before because it places more than 60,000 parts per hour. The new machine is not only more efficient, but also boasts the latest technology for placing surface mount components. The addition of this high-speed line has offered increased flexibility within our surface mount area, and has afforded our manufacturing team with increased and more accurate throughput.
Q. Have you installed any other new equipment or do you have plans to within the next year? If so, what are your plans?
A. Currently, we are where we need to be as far as equipment requirements. Our current inventory fully supports our current customers and nicely matches our workload. However, as we continue to expand and take on new customers, we always are open to adding necessary equipment based on any requirements they may have. As technologies change and evolve, we also will move forward accordingly with any new equipment purchases as necessary.
Q. Please describe your new product introduction capabilities for volume production.
A. As an added value, Saline Lectronics’ production and engineering teams are well versed in transitioning prototype runs into full production. We work very closely with our customers during the prototype stage, suggesting needed manufacturing improvements as well as helping with any design or functional concerns that may arise. At our customers’ request, we provide feedback on the prototype runs throughout the manufacturing process, and the necessary changes that need to be made for production volumes.
Q. Saline Lectronics has an in-house IPC Certified trainer. Please describe the continuous training and certification that you provide for your production workers.
A. We currently have two IPC Certified trainers on our staff. Due to their formal training and certification, they hold training sessions for other employees throughout the year. All incoming employees are subject to training classes in order to identify their aptitude and place them in the most ideal position. Additionally, we provide ongoing sessions for current employees to keep current on their skill set as well as learn any new electronics standards.
Q. Can you offer any tips regarding making revisions to prototypes and reworking the electronics assemblies?
A. Due to the ever changing nature of the electronics world, revisions are a natural progression for most assemblies. We encourage our customers to include us during their decision making process for the required revisions, not only to keep us informed of how they may impact production, but also for us to assist in how they might affect the manufacturing end of things. Our talented team of engineers, buyers and technicians bring a wide range of perspectives to the table, which truly can enhance the revision process for our customers.