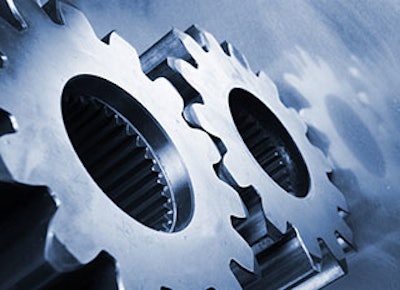
A successfully managed supply chain is based on a single premise — produce more high-quality products, consistently, in less time for greater profit. During the early 20th century, factory-floor automation revolutionized manufacturing with this same idea. Since then, process automation has taken over as the driving force to generate greater efficiency in every business. Much of this work takes place in the back office.
Over the last 20 years, Enterprise Resource Planning (ERP) systems have become the cornerstone for back office process management. Given their initial promise, many companies invested heavily in ERPs. However, to add much-needed flexibility and function, most organizations also invested a lot of time and effort in customizing their ERPs. Manufacturers typically spend an average of over $11M annually on ERP implementation and maintenance, typically overrunning their annual budgets by $3M[1].
Three Options for Improvement
With such large sums of money spent just to keep ERPs running, it’s clear that there’s room for improvement. Gartner predicts that highly customized ERPs will be relegated to “legacy” status by 2016[2], there are still options that can be used to energize and revitalize corporate ERP. There are three basic choices.
1. Rip and Replace
The first option is to rip and replace your legacy ERP system in favor of a new on-site implementation. While potentially effective in the long-term, this strategy can come at a very steep price in the form of lost man hours, business disruption, and, of course, monetary investment. It’s also risky. You could simply be replacing old problems with new ones.
2. Outsource
Alternatively, you could choose the other extreme and replace your physical ERP infrastructure completely in favor of an outsourced service. However, outsourcing ERP functions can be costly and can result in lost process efficiency and control. Sometimes, outsourcing simply relocates challenges rather than solving them. In many situations, outsourcing ERP functions simply isn’t an option.
3. Automate
The third option is a hybrid approach, which leverages your existing legacy ERP infrastructure as a process backbone while it employs automation to integrate and execute process steps across your enterprise. Below are two real examples of how this hybrid approach to process automation has revitalized the legacy ERP systems of some of the world’s leading global manufacturers.
End-to-End Visibility
Daikin Europe N.V. is a fully owned subsidiary of Daikin Industries, a global provider of advanced air conditioning solutions for residential, commercial and industrial applications. The company manufactures and sells air conditioning units for over 30 countries across Europe, the Middle East and Africa. To manage its extensive network of supplier and reseller partner relationships throughout the region, the company uses an Electronic Data Interchange (EDI) system designed to communicate financial data — such as orders, payment notices, shipment verification et cetera — between facilities in Europe and corporate headquarters in Japan.
To ensure mission-critical end-to-end delivery of the supply, production, distribution and logistics related business processes, Daikin developed an IT environment that interfaced with its business partners and IBM System i5-based applications. But this solution came with some challenges of its own.
One of the biggest challenges that Daikin’s IT administrators encountered was the need to manually patch its native component content management system (CCMS) tool across the enterprise, since it didn’t provide alert notifications or execute ERP processes in parallel. To recover its systems from any failed tasks, administrators needed to spend additional time performing labor-intensive manual recovery. With more than 33 percent of its daily tasks involving legacy tools and partners, the need to automate these processes was crucial to stay on time.
Using our system-agnostic automation solution together with Daikin’s existing legacy infrastructure and ERP, the company automatically integrated data from both legacy and EDI systems, allowing data in one system to trigger events in another. Today Daikin manages interface tasks in near real-time and uses automated escalation procedures to solve most process errors before they slow down business.
Daikin no longer struggles to manage the mission-critical sales, financial and tracking data from suppliers and partners. By automating its most critical back-office processes, Daikin was able to save significant time and resources, right alongside its existing ERP and infrastructure investments.
Sequential Accuracy Required
A leading manufacturer found that its existing system restricted its ability to properly scale supply chain operations. Each portion of the company's supply chain requires numerous steps to take place. If these don’t run or run incorrectly, they hold up the next business steps. With over 250,000 complex, sequential tasks taking place daily (over 8 million per month) the company placed a tremendous process burden on its ERP. In initial attempts to improve scalability, the company’s IT team deployed custom-developed modules to overcome these shortcomings. With five central SAP® ERP systems, 23 additional SAP systems and more than 2,000 servers in the company’s data center, these patches proved expensive to adapt and difficult to maintain. On more than one occasion, production was disrupted and workers didn’t receive the correct information to proceed.
After reviewing its process requirements, we worked with the company to automate and centralize the management and monitoring of the company’s entire supply chain. With automation, the company uses its existing ERP to successfully manage back-office processes faster and more reliably for improved efficiency and overall quality assurance.
Conclusion
These are just two examples of how process automation can profoundly energize “legacy” ERP for the supply chain in manufacturing. With the right automation in place, control, visibility and coordination become more manageable. Process automation scales growing complexity back down to human-size and your existing infrastructure works with significantly fewer limitations.
About the Author
Jeff Rauscher, Director of Solutions Design for Redwood Software, has more than 31 years of diversified MIS/IT experience working with a wide variety of technologies including SAP, HP, IBM, and many others. Rauscher has worked in operations management, data center relocation, hardware planning, installation and de-installation, production control management, quality assurance, and customer support.
[1] Panorama Consulting (2014). The 2014 Manufacturing ERP Report. Retrieved from http://panorama-consulting.com/resource-center/erp-industry-reports/the-2014-manufacturing-erp-report/
[2] Gartner, Inc. (2014) Gartner Says By 2016, the Impact of Cloud and Emergence of Postmodern ERP Will Relegate Highly Customized ERP Systems to ‘Legacy’ Status. Retrieved from https://www.gartner.com/en/newsroom