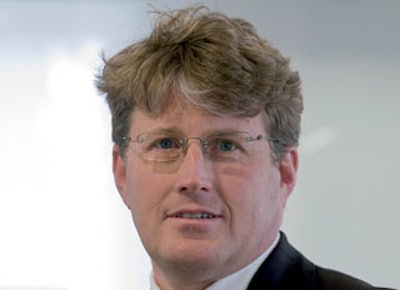
The world is changing rapidly and in the middle, if not even the driver of this process, is the automotive industry. Globalization and individualization megatrends set the pace, supported and ultimately made possible by innovations in information technology.
Only ten years ago the vast majority of suppliers were located in the vicinity of the OEMs to better provide the parts or assemblies necessary for production. Most Tier 1 suppliers were typically located with a just-in-sequence or just-in-time assembly plant near or at the customer site. For example, a local supply region in Europe made it possible to get parts within 24 to 72 hours of production.
Since the order processes were modeled using optional capacities, there was little to worry about. Whether the parts were in inventory or not, the shipping lead-time was on only 72 hours with a production order lead-time of around three to four weeks. It was enough for an assembly plant to know that 300 sunroofs could be delivered per day. The model or configuration choice was a secondary consideration because sunroofs came from a nearby supplier or from a sub-assembly within the final assembly plant. The supplier could deliver the desired sunroofs by assembling them shortly before they were installed and to the exact configuration for the specific sequenced vehicle.
Changed circumstances require a new methodology
In today’s automotive supply chain the situation has changed: when a customer configures and orders his vehicle at the dealer (or on the Internet), a growing proportion of parts come from distant regions, and the delivery may take several days or even weeks. The variety of parts has increased dramatically. A customer can now choose from a number of features which affect other part configurations leading to a high number of different options. For example, with high-end vehicles, the number of possible electronic control units has grown to more than 60.
Based on the selected features, such as engine, transmission, seats, onboard electronics, sound system, etc., the component requirements are usually calculated or generated from rule-based bills of materials. For each part, there can be one or more rules that are used to determine which part is required for a specific order. If a customer in the United States orders a vehicle from the BMW 5 Series with a navigation system, the chosen engine implies certain aggregates. From the rules, one can derive a particular navigation device for the local market.
The variance is based on regional differences. The Mercedes C-Class has several hundred rear axles, depending on engine size, right or left-hand steering, etc. The supply requirement must be chosen in the most economical way for the assembly plants whether they are located in Germany, South Africa or the United States. Given the great diversity, it is now almost impossible to keep all the variants in sufficient numbers at the assembly warehouse. Instead, OEMs request the needed variants in an order-oriented fashion from the supplier which may be several thousands of miles away resulting in long delivery times.
Global production networks have been created to accommodate the growing global supply chain. For some level one components, shipments to the OEM start from six to eight weeks prior to final assembly. In nearly all cases, six to eight weeks out prior to assembly the supplier plant is sending parts based on a combination of firm orders, forecast orders and component forecasts.
With parts in-transit based on a mix of forecast and real orders, the OEM must consider the mix of parts and their projected arrival time. Since OEMs no longer keep large part inventories, transparency and awareness of which parts are in the shipping pipeline is critical. Visibility cannot be limited to non-specific features such as “navigation system” and must include the specific components required based on the vehicle orders and rule-based bill of material.
Organizationally, there are two separate areas that must come together: the sales-oriented scheduling of orders and material scheduling which consists of supplier orders, material shipping requirements, part control, and transportation. With a global supply chain, it is necessary to merge the information between the order slotting or scheduling systems and the material scheduling systems. In order to get reliable and efficient planning parameters, an explosion and implosion of the bill of material for all orders is required down to the relevant level of detail.
The immediate benefits of the visibility gained from the merging of this information are savings on freight and expedite costs. Without the precise coordination of information in both areas part shortages are not discovered until very late in the supply pipeline. Traditionally, supply coverage is checked shortly before the assembly process to determine if all parts will be delivered on time. If parts are missing, it becomes a challenge for suppliers to provide the correct parts on time resulting in costly expedites. It is usually the responsibility of the supplier to create a flexible supply and organize their part flows accordingly.
However, with the growth of global sourcing, it is becoming more of the responsibility of the OEMs to optimize supply chains for flexible delivery in a timely manner. This is extremely challenging due to the push in flexibility with the large variety of parts while keeping little inventory buffers in the warehouse. Although many parts are supplied locally, a significant percentage comes from overseas. With high visibility, decisions can be made from both an order planning and material supply perspective to avoid shortages and suppliers can cost-effectively provide parts from great distances.
If the supply chain is not transparent and stable, supply shortages will ultimately cause production bottlenecks. Quick adjustments are possible but require expensive air-freight to fly in the missing parts. Because the need for such critical part air expedites are inevitable, OEMs are planning for these "special cases" by booking air freight capacity sometimes as much as months in advance. Ideally, with visibility during order slotting, one could check whether or not the necessary parts will be available before making commitments. Most of the systems used today, do not accommodate the use of part requirements in the planning process. In fact, it usually takes an overnight job to convert order scenarios into part requirements and for most, it is a manual process to backward translate part bottlenecks to the affected orders.
About the author:
Oliver Reisch. Oliver is the COO of flexis AG and member of the company’s board responsible for Professional Services. Oliver has been with flexis AG since 1998 and focuses mainly on topics related to Advanced Planning and Scheduling. He holds a master’s degree in aerospace technology and worked previously as a project manager at the Fraunhofer-Gesellschaft for five years. For additional information, please visit www.flexis.com.