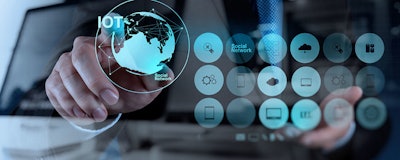
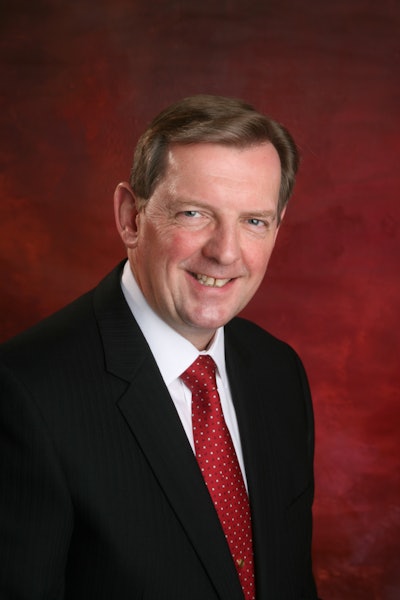
The Industrial Internet of Things (IIoT) offers tremendous potential for manufacturing and process enterprises seeking new drivers of growth. Leveraging data generated by production systems across the plant can generate insights that promise to transform manufacturing efficiency, productivity and agility.
But many manufacturing operations rely on production systems that may be years or even decades old, representing large investments and long depreciation cycles. Ditching it all and creating an entirely new infrastructure designed from the ground up for IIoT is just not a realistic option for most companies — especially in industries where margins are thin. In many cases, enterprises take the approach, “if it ain’t broke, don’t fix it.” Yet, they still want to reap the advantages of smarter, more automated production processes.
How can manufacturers create a bridge between their legacy automation systems and the technologies that enable them to reap the advantages of the IIoT? Based on our experience working with enterprises across diverse industries — from product manufacturing to food and beverage to the chemical and energy sectors — we believe there are some key success factors for achieving next-generation automation capabilities in legacy manufacturing environments.
No. 1 - Focus on Interoperability
Industrial environments are typically composed of discrete automation systems deployed throughout the organization over time. These systems are often not tied together, resulting in “siloed” data stores throughout the facility. Compounding the problem is the fact that older automation systems are likely based on proprietary technologies, making them difficult to integrate with other data stores. Yet sharing and consolidating data is the key to unlocking the benefits of the IIoT.
A key step toward IIoT is making sure any new systems added to the environment are based on industry-standard components to allow interoperability. That includes standard computing platforms, networking infrastructure and software running standard operating systems and applications from multiple vendors. While the value of industry-standard systems in terms of reduced hardware costs and increased flexibility is well recognized, it is equally critical to select systems that allow the easy extraction of data to a consolidated data pool. Does that new programmable logic controller collect useful data frequently enough and make that data available to a centralized data store? Such “back end” considerations are not traditionally top of mind for operational engineers, but are essential for enabling the “Big Data” analytics that are a crucial part of the IIoT.
No. 2 - Push Intelligence to the Edge
A key element of an IIoT infrastructure is distributed intelligence with data gathered throughout manufacturing facilities by sensors at “the edge.” The latest automated manufacturing equipment typically has embedded sensors for collecting data; something legacy automation systems clearly don’t have. However, it is possible to overlay legacy systems with a network of sensors. While these sensors may not provide the supervisory capabilities of embedded sensors — autonomously controlling device functions — they collect data from devices that can then be uploaded to a central database to drive analytics.
One way this delivers value in a production environment is by enabling “predictive maintenance.” Take the example of an automated production line. To minimize the risk of failures, components are often replaced on schedule, whether or not they actually need it. With a “smart” production line, data on component performance is gathered continuously from sensors, uploaded to an analytics engine which evaluates all system metrics against benchmarks to anticipate problems. Is a motor giving subtle signs of wear that require service or replacement? Operators are alerted and the component can be swapped out before it fails, avoiding unplanned downtime and maximizing productivity. That’s the most basic example; more sophisticated analyses can enable all manner of automated production optimization. Moreover, this insight from the edge can be made accessible across the plant or even remotely using a thin client strategy — another example of leveraging standard technology to improve productivity and efficiency.
No. 3 - Accept Greater Connectivity
Data sharing and connectivity are central to the IIoT. Yet many manufacturers equate connectivity with risk. And rightfully so, if they are still running legacy operating systems that are no longer supported and cannot be updated with security patches. It is surprising how many manufacturing systems run on versions of software more than a decade old. Enterprises implementing an IIoT strategy must accept that greater connectivity is inevitable and update critical points of vulnerability accordingly.
While many IIoT implementations upload data to a cloud-based data store, this is not essential. Indeed, we have seen successful IIoT deployments featuring heavily firewalled automated control systems linking to data stores and analytics via the corporate network. This requires a greater level of coordination and cooperation between operational technology (OT) and information technology (IT) teams. In this respect, moving to the IIoT requires cultural as well as technological transformation.
No. 4 - Prioritize Data Resilience
Any unplanned downtime in a manufacturing environment is bad news. But in an IIoT infrastructure where data is central to manufacturing operations, the risk of data loss is critical. The analytic programs that drive the kind of predictive insights described earlier are quite sensitive to the data they are fed. Any lost data can have a drastic impact on the accuracy and reliability of those analytics.
Manufacturers traveling down the IIoT path must view fault tolerance as a mission-critical priority. That means making sure no data is lost at any point — from the data source at the edge to the historian database where data is consolidated and made available to analytics engines. The closer to the source the data loss is, the greater the impact on the resulting analytics output on the back end. After all, if you lose data at the point of collection, it’s lost forever.
There are a variety of strategies for achieving end-to-end fault tolerance at scale in a distributed IIoT environment. This is particularly important in virtualized environments where potential points of failure are concentrated in a single machine.
Reaping New Value from Old Systems
The good news for manufacturers with legacy automation infrastructures is that you can reap the benefits of the IIoT without ripping-and-replacing existing systems. By moving towards standards-based architectures, deploying intelligent sensors, embracing secure connectivity, and focusing on fault-tolerance, organizations can unlock tremendous business value without discarding existing automation investments. Taking an incremental approach, manufacturing and process enterprises can begin to unlock the tremendous transformative value of the IIoT.
John Fryer is Senior Director of Product Management & Marketing at Stratus Technologies.