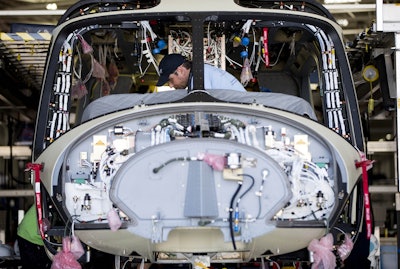
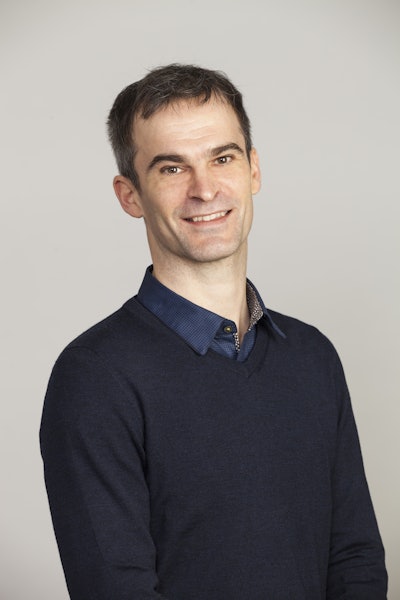
In an age of increasing technological sophistication in manufacturing processes, its people are the most important and valuable resource a company possesses. The human element is what dictates true operational efficiency – that is, if it can be optimally integrated into a business’ production practices.
Typically, Overall Equipment Effectiveness (OEE) is used to measure efficiency output. OEE data can be automatically created within a Manufacturing Execution System (MES). Automated data alone does not lead to improvement, a business must harness additional factors to ensure action is taken based on the data, and performance gains can be realized. MES solutions that focus heavily on automated data collection end up being difficult and unintuitive to use, leaving hard-working staff feeling disillusioned and ineffective. Obvious problems occurring on the factory floor remain unsolved, KPI metrics are not immediately available and there are no overall visualizations of performance meaning shop floor staff have no way of effectively measuring their productivity.
Fortunately, there is an alternative approach to MES that adds significant value to operating performance.
Uniting the people to the process
Having effective MES software is not just about trusting your staff to oversee the production processes; it is about empowering your staff with an MES that specifically spotlights their abilities and personal performance levels. This approach is known as ‘human MES’.
You can have state-of-the-art technology and top-notch talent, but if your people aren’t united to your process and intertwined within, your company may not achieve the competitive advantages required in today’s market. In a factory, it is the people that know ‘their’ machines best, and the people who are best positioned to inform management on work cycle improvements. With a strategically developed human MES approach, everyone within a company – from the factory floor through to mid and senior level management – can contribute their expertise to the benefit of production and, ultimately, profitability. Businesses should treat the human expertise with the value it deserves.
The Best Human MES
The best human MES solution gets operators involved from the start and makes it easy to use the system. Everyone understands the need for the system, and is in no doubt about “what’s in it for them”. Being a part of the MES solution removes any morale-sapping doubts that result from lack of transparency between factory floor and management. It also gives staff the personal satisfaction of knowing that their actions have made a sincere difference to the company.
The MES software itself should automatically:
- Collect and collate all data acquired form the production process
- Analyze it on a web-based platform
- Help staff address key performance indicators from the production process
- Provide readily available information to factory floor staff through easy-to-use terminals and mobile devices
- Allow operators to monitor current efficiency by accessing relevant KPIs at the touch of a button
- Provide instant staff motivation, enabling them to see if they are hitting targets while allowing them to monitor production schedules and immediately disclose any errors or disruptions
- Review and analyze the data on a frequent basis, and use it to effect change in-shift and keep production tracking on a targeted course.
More Than Software
A human MES solution is designed to be more than just a software system. It encourages a holistic approach to refining the manufacturing processes. A human MES encourages communication and operational optimization based on the intelligence achieved through the integration of the human and the machine.
In order to reach their highest potential, employees need to be empowered and educated during their every day jobs. The system does just that by giving workers the opportunity to incorporate their knowledge and experience into one IT-supported platform. By contacting a specialized provider of tailored MES solutions, your business has the chance to outperform the competition with its own human MES approach in as little as six to eight weeks – including complete software implementation and intensive staff training.
Often, a business without such an optimized solution does not realize the gains that can be achieved or the problems that currently exist. What is the result when you combine happy, motivated employees and sophisticated, tailored software? Efficiency, profitability and business longevity.
James Wood is Director of Factory & Activplant Product Lines at Aptean.