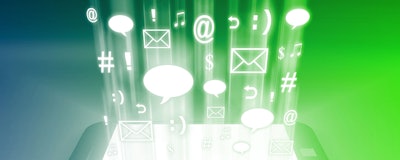
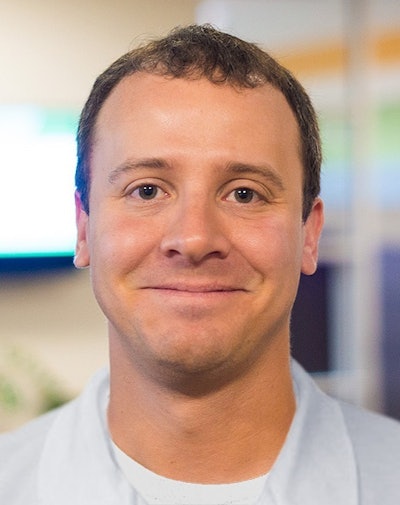
Virtually every industry and organization can benefit from better project collaboration. Manufacturing, in particular, has complex projects with many moving parts. Integrating the expertise of numerous people in various locations and sharing large amounts of data is difficult with traditional solutions, such as email and spreadsheets. Open collaboration is critical in bringing people, ideas, systems and data together seamlessly to complete projects on time, on budget and at a high quality.
Here are four manufacturing scenarios highlighting the need for more effective collaboration. The next section will describe how collaboration technology can help manufacturing organizations be more nimble, responsive and efficient.
Scenario No. 1: Product Development
A manufacturing company manages the creation and go-to-market of products. The project manager deals with multiple stakeholders both inside and outside the organization, including customers, product development and marketing during this process. Projects are freely structured with different schedules and durations. Numerous people are involved in the different project phases and lack visibility into status. Spreadsheets have become an inadequate tool to support the product development process, often causing product delays and missed opportunities.
Scenario No. 2: Implementing New Safety Regulations and Standards
A manufacturing company in the automotive industry is tasked with implementing new safety standards across multiple agencies. A single standard may involve dozens of agencies from around the globe working together, communicating remotely, and transmitting and sharing large amounts of data. This leads to a lack of visibility into implementation status and project complexity.
Scenario No. 3: Supply Chain Coordination
A biopharmaceutical manufacturing company distributes numerous products each year supported by a supply chain of internal and external stakeholders. The movement and storage of materials, work-in progress inventory and getting finished products from point-of-origin to point-of-consumption can be tedious to manage.
Scenario No. 4: Updating Systems, Software and Manufacturing Equipment
A European company responsible for a beverage production and bottling operation is faced with replacing its control systems and re-automating the entire processing section. The organization must work with 10 businesses from across Europe to develop and implement a software solution to control 12,000 valves and pumps. They must ensure that the production process is fully automated, 100 percent transparent, and safe for people, products and facilities. The challenge of complex collaboration across organizations, external suppliers, partners and national boundaries is exacerbated by a tight deadline.
How Collaboration Technology Can Help
What all four of these scenarios require is a common platform to simplify communication among internal and external members, and get work done. A cloud-based project collaboration solution would give teams access to the plans, deliverables, documents and people needed to execute these projects. Leveraging an online platform gives project managers and business leaders the ability to bring all the different stakeholders together in one place for design, planning, execution, control and monitoring of activities. With traditional project management tools and social media functionality embedded into these platforms, manufacturing organizations can keep everyone on the same page.
For instance, incorporating project management tools such as Gantt charting enables teams to plan and track projects using classic constructs, such as milestones, dependencies and due dates that are visible to everyone with the right permissions. Teams can also assign tasks and visualize progress using elements such as digital Kanban boards — made up of cards resembling online Post-it notes — that track individual activities.
Project managers can use Kanban boards to divide complex tasks and enable teams to self-organize, or assign work to different team members to speed completion and reduce resource overload. The cards not only represent the tasks that need to be done, but can also serve as work orders with documents, hyperlinks, videos and other content attached. Combining Gantt charting with Kanban boards and cards can provide a unified view into the progress of overall activities and milestones.
In addition, social media elements, such as message boards embedded into the common platform, help speed communication and keep everyone up-to-date on progress and issues. Some collaboration platforms even provide Web-based, video conferencing capabilities to bring everyone together in minutes, no matter where they reside.
With everyone constantly updating the system, project managers have unprecedented access into the progress and status of each initiative across multiple organizations. Everyone knows exactly who is doing what, when and how. Users from around the globe in different companies can log into the service to securely share documents and information in an organized and transparent way.
The ability to efficiently share detailed, up-to-date documents with the team is vital. This includes the capability to grant or restrict access to any data, including drawings, designs, technical specs, etc. New collaboration technologies offer full version control, locking and reviews, and relate back to project activities and tasks. Team members always have access to the latest version of a document, instead of it being hard to find in internal document and content repositories or lost in an email-based volley of “latest versions” and “final-finals.”
Working together in the complex manufacturing environment requires sophisticated technology. These are just a few of the elements that modern collaboration platforms offer. Choosing the right collaboration solution does not demand a deep technical understanding. It only requires a desire to equip the organization with the ability to set direction, communicate, execute tasks, track progress and ultimately achieve goals, no matter where team members work.
Jason Morio is a Projectplace Segment Manager at Planview.