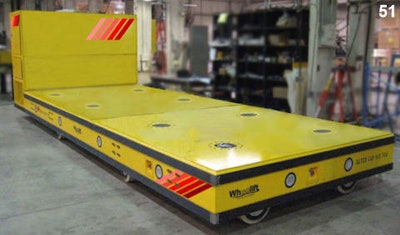
Mel Terry, the designer, developer and patent holder of the Wheelift heavy transporter system, has been quietly revolutionizing the way manufacturers get their work done. And from where he sits right now, Terry is anticipating a future in which his creation is being used — and abused — in transporting the heaviest creations of our various industries, such as submarine propellers that weigh 70 to 80 tons or large pieces of the F-35 fighter jet.
In the early 1990s, Terry was working for NASA, which needed a heavy-duty transporter to shuffle around massive pieces of an in-development rocket motor. When it comes to moving extremely heavy loads, there aren’t a lot of options — for NASA and typical manufacturers alike — with the most reliable choices being cranes or rails in the floor. Air bearings have always been a possibility, but they require extremely smooth floors — something that’s not all too common in theU.S.
NASA killed the project that Terry was working on, but that didn’t kill his desire to make a better heavy load transporter. He had been in contact with heavy car builders, and one asked if he could design the wheel assemblies for an automated roll changer. In 1992, the first production was brought on-line, and the company was pleased. Terry’s patent was issued a few years later.
For the next few years, Terry worked on other projects, but never could give up on his heavy-load transporter. In 1998, he returned to the plant where his first machine had been brought on-line years ago, not sure what to expect. He says, “The first thing I did was check the wheels. They were urethane wheels, and they had never been used to move those kinds of loads before. So, I figured they had damaged the wheel seriously. But the original wheels, other than being greasy and nasty—there was no damage. That was the first that I knew this on-center idea would work.”
From there, Terry needed a company to work with to bring the Wheelift into the big show. Terry says that “Doerfer took this on and decided it was a technology they wanted to do. It would allow them to build larger AGVs, so they licensed the technology and we began to pursue it vigorously.”
Bring On The Heavy Loads
Despite the capacity to deal with massive loads, the Wheelift system is rather elegant in design. The system uses an open center axle, with a vertical lift column that allows the assembly to turn on center. This is important, because the wheels needed to be omnidirectional, and they needed to move in coordination with the all the others in a modular fashion. All of the movements are done with a series of complex mathematical functions, so that the system always knows the location of all the axles and the centerpoint. Without these important requirements, the Wheelift system would have never been viable in the first place.
The second critical component of the wheel assemblies is a fluid suspension system that shares the load equally, no matter how many wheels have been tethered together to make the transporter. Pressure actuators are used in conjunction with a centralized pressure monitoring system so that unbalanced loads are compensated for properly, and that no single wheel will be forced to carry more than its individual limit. This is also what allows the transporter to tackle less-than-perfect flooring, which is commonplace on many plant floors, and often the status quo in Navy dry docks and other extremely harsh environments.
This connectivity is what helps the transporters move incredible loads. Terry says that the Wheelift has an unlimited capacity range due to its modular construction and the emphasis on omnidirectional, fluid suspended axles that can turn precisely on center. He says, “They can carry 10,000 pounds or 200 tons. It’s just a matter of how many axle assemblies are beneath it, and what size they are.”
That’s why the transporters have been popular in the aerospace and naval industries, where production lines have changed considerably in the last few decades. When building a plane, manufacturers used to construct them in place, ferrying over components as needed. Now, they can use a transporter like the Wheelift to move them down a massively-scaled production line. And for a lot of industries, that’s a game-changer.
While manufacturers of smaller goods have been automating large portions of their process — if not its entirety — for decades, the makers of extremely large objects have always required a greater human interaction for even simple actions, such as bolting together components. According to Terry, the Wheelift could help change that status quo. Because the motions are based on sophisticated calculations from a single point of origin, his transporters are, essentially, automatic guided vehicles (AGVs).
And an incredible degree of automated precision is exactly what defense contractors, among other industries, have been begging for. Terry says, “The advantage of the Wheelift system is that its sophistication allows a whole new range of how manufacturers can build products.”
The second half of this piece will be featured in tomorrow's Insider.