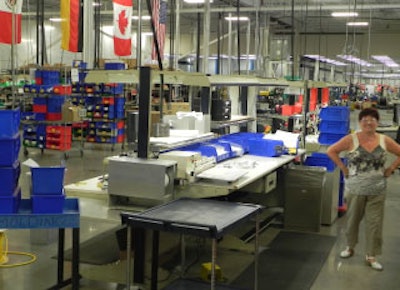
This article first appeared in IMPO's October 2012 issue.
News about manufacturing growth is usually well received. When that expansion relates to a European company growing its presence in the U.S., it’s even better. And when there are significant lessons that can be learned from this particular expansion, it warrants a closer look.
This brings us to Plymouth, Minnesota where Germany-headquartered TURCK recently doubled the size of a production and distribution facility that has played a key role in the company’s growth of cordset and connector products. TURCK is a name that most in manufacturing and product design will recognize due its prominent position as a supplier of sensors, interfaces, cordsets, connectors, and distributed I/O for the industrial and process automation marketplaces.
The need for expanding this particular facility, which is one of the company’s 25 global sites, stemmed from the usual culprits of growth and the need for greater production flexibility. In particular, is TURCK’s need to respond more quickly to a growing demand for customized wire lengths and colors for cordsets.
Markets where TURCK has seen significant growth include automotive, semiconductor production, and mobile communication devices. Each month 770 miles of cable are used in products assembled and shipped from the Plymouth location.
“Our business continues to grow, especially here in the U.S., and we hit capacity for this facility in early 2011,” states Karie Daudt, TURCK’s director of marketing. The building was initially constructed as a warehouse, which often challenged the establishment of ideal production flow. So while the initial constructs worked, a new and expanded space would allow for less obtrusive movement of both materials and finished product.
“In addition to adding more shipping docks to eliminate bottle necks and get more product out the door, there was an emphasis on opening up the facility to improve plant floor movement,” adds Daudt. So with those goals in mind, the expansion paid special attention to eliminating physical boundaries that could have isolated production, storage and shipping, as well as hinder more efficient work flow.
“No walls and no boundaries also leads to better communication and improved teamwork,” offers Daudt. “In addition to eliminating the visible barriers, the expansion seemed to help get rid of a few invisible barriers that might lead to people not working together based on perceptions of individual sections or responsibilities, as opposed to viewing things from a broader perspective.”
Ramping Up Without Slowing Down
Construction started in November of 2011 and was completed ahead of schedule in May of 2012. The total square footage was doubled to nearly 100,000 square feet. In addition to greater production, testing, and shipping space, TURCK was able to expand the tool shop and make major investments in new conveying equipment, as well as an inventory management system. In total, the company invested six million dollars in the Plymouth expansion.
The elimination of walls and addition of brighter lighting ensured the requisite “open” feel was realized. This re-design also allows for greater flexibility in adjusting to customer demands and industry trends via a more efficient work cell layout. From receiving through production and shipping, a U-shaped format has been implemented for greater overall efficiency.
Additional early improvements include greater worker safety via wider forklift lanes and smarter overall material handling strategies. Both raw materials and end products can now reach their destination within the plant more smoothly.
“Essentially, we’re reverse-engineering the entire facility,” offers Dee Comeau, the plant’s continuous improvement specialist. “We had to temporarily move some of our distribution operations to a different building to set production flow up the way we wanted it. As a result we did have some shipping delays, but only for a short time.” Comeau is quick to point out that after-hours moving ensured that even as sales increased, production never failed to keep pace with demand.
She adds that this type of piecemeal approach was utilized in other areas as well, to help ensure manufacturing goals were still realized throughout the entire expansion process. Currently, the time from custom order to delivery is about two weeks for the Plymouth facility.
“Basically, we’re in the stage of moving things around, trying it out and adjusting as necessary,” offers Comeau in how TURCK is working to fully utilize its new space. “The only permanent area is warehousing because with Minnesota winters you need to manage safety issues like snow and ice to ensure there are minimal opportunities for slips and falls.”
Some areas are intentionally being kept open to prepare for the future. “The right way to use this space now could change over time and we want to ensure we have continued capacity to grow,” adds Comeau.
“People were programmed to work in smaller spaces and make the most with what we had,” adds Keith Woods, production manager. “But now we have to look at whether the layout is right for the facility and the products being made — think about what could work instead of what has always worked in the past.
“We’re working towards changing the mindset and seeking out the unknown. Just because a layout looks good on paper doesn’t mean it will be flexible in adjusting to the changes we see in customer demands,” he adds.
Comeau adds that the more open layout also allows for implementing a number of Lean manufacturing practices that simply didn’t make sense previously. “Lean has always been there, but now we have a facility suited to making those improvements,” she states. “We’re fortunate in that we’ve always had management buy-in. Now we can take things to the next level in empowering people to make decisions at the lowest possible level and implement appropriate cost controls because we have more built-in production flexibility.”
“We have to change our planning approach slightly with this new facility,” states Wood. “Some of the things that used to make sense from an operational or work flow perspective no longer do. So there have been some growing pains in adjusting to this bigger space.”
Changing, Yet Staying The Same
“I think everyone in the plant is excited about the expansion, they’re embracing the changes and proud to be a part of TURCK,” offers Daudt. “But we do face some challenges as we grow in making sure we’re not losing a family-like culture that’s always been here. We have a lot of family members that work together here. So it’s a balancing act in managing the growth and making the right investments while preserving a culture that’s been such a crucial part of that success.”
The facility employs nearly 600, and has seen a lot of benefit from temp-to-hire programs that allow for a more deliberate pace in growing the workforce. The Plymouth location might also be one of the most diverse plants in the country, with 20 different languages being spoken by those on the production floor. To help prevent potential communication issues, photos have been implemented in assembly cells, storage, and as an element of fulfillment and replenishment strategies in identifying the correct component, part, or tool that is required for processing orders.
Another area where the benefits of expansion have created the need to balance the old with the new includes the mix of more highly automated equipment with a history of manual assembly and fulfillment approaches. The nature of the product, combined with a high level of customization and customer service that has been the foundation for TURCK’s success, had led to a great deal of assembly being done by hand. So there has been an adjustment period in dealing with new conveying and inventory management systems that remove some of the more manual aspects of production.
Ultimately, the improvements seen at TURCK’s Plymouth facility are not unlike many being realized by manufacturers across the country. While the investments result in larger facilities and enhanced equipment technology, the real return comes from providing workers with a greater opportunity to succeed, and along with them, their company and its customers.