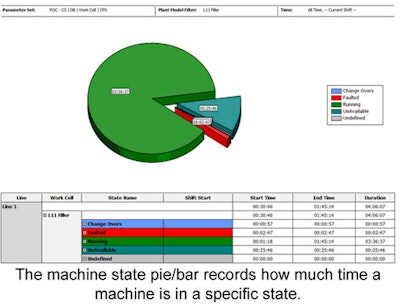
This is part two of a two-part piece. Part one can be found here.
Seeing Is Believing
In some cases, disparate data points alone aren’t enough to compel a manufacturer to action, especially when operators can’t physically see the problem identified by the data. Rather, it’s combining data in a way that defines root causes that offers compelling enough evidence to drive actionable improvements.
When a performance management software system at a large beverage manufacturer pointed to significant downtime in a tunnel heater machine, operators simply didn’t believe the data because they didn’t see the machine stop. Investigation into the process revealed the machine was stopping frequently because its heaters were undersized, an issue confirmed by monitoring the temperature inside the tunnel.
The heaters could not quite keep up with the flow of product entering the tunnel, so the conveyor stopped until the temperature increased — all within a split-second. Leveraging these objective, fact-based data points from the control system allowed the manufacturer to identify root causes and specific improvements to reduce costs.
How to Improve Efficiency
Implementing a system that will help improve efficiency and reduce costs requires not only collecting and storing the right data, but also analyzing it in a way that offers actionable, measurable process improvements. Following these easy steps can set a manufacturer up for serious savings:
- Collect and store performance data — Data should be collected from the control system and stored within a performance management software system database. Many manufacturers rely on clipboards and Excel spreadsheets to house this data, but leveraging an off-the-shelf software program will allow for deeper analysis and more impactful long-term insights.
- Collect the right kind of data — OEE data points alone can’t provide a manufacturer with adequate information to determine root causes. Manufacturers should also collect data that measures production counts, scrap rates, machine cycle times, downtimes and causes, unproductive time, machine states and quality problems.
- Analyze the data — In general, OEE calculations lead managers to compare machine performance to determine whether equipment is achieving maximum production. They don’t, however, answer the question of how to produce more. Analyzing a deeper level of control system data via a performance management software system allows manufacturers to begin answering questions such as: How are we doing? What are the real problems? What should we focus on first to make things better?
- Act on the data to make process improvements — A performance management software system can generate easy-to-understand dashboards that identify areas for improvement — but it cannot physically take action on the plant floor. That responsibility ultimately falls on the plant manager.
Bringing efficiencies into focus is a business imperative for every forward-looking manufacturer. Together with a sound strategy, a comprehensive performance management software system can reveal data needed to make informed — and measurable — operational improvements.
For more information, please visit www.rockwellautomation.com.