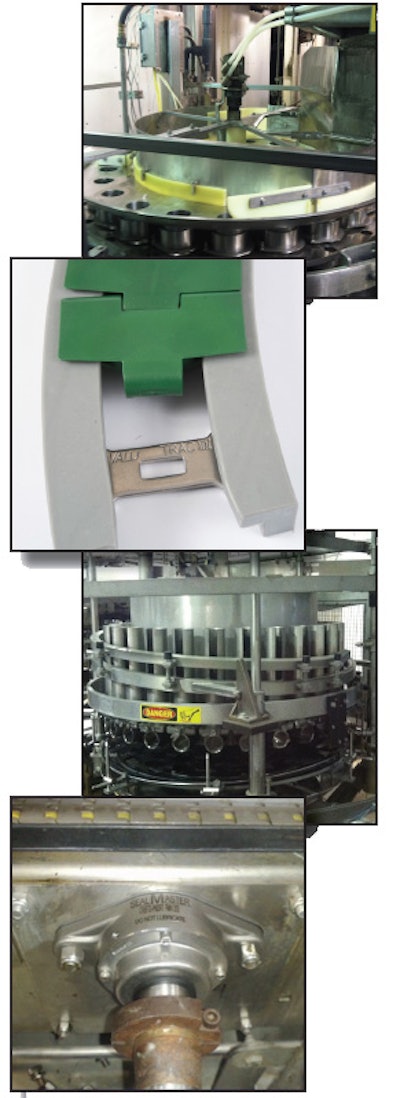
BDI Devises a Unique Tabletop Conveyor Solution, Saving a Vegetable Packing Plant Time and Money
The Problem: A national producer of canned fruits and vegetables had to halt production on its conveyor line whenever the type of product to be filled changed. For dry fill production, the setup uses gravity fillers, which are mounted under a vibrating hopper and rely on gravity to fill the cans. For wet fill production, the process requires a piston filler, which drops the partially cooked, pre-mixed fruits/vegetables into the cans. Every time production switched from dry fill to wet fill, there was a 36-hour shut-down period during which three employees would reconfigure the line.
The Solution: BDI worked with System Plast to design a tabletop conveyor system that combined both modes of filling into a single line. For dry fill, the cans enter the drum fillers first and then proceed to the wet filler for the brine. For wet fill, the cans now enter the conveyor beyond the drum/dry filler and go directly to the piston/wet filler.
The new conveyor incorporates System Plast chain with NG material and Valu Trac II with Nolu S material to reduce the amount of pull required. Other components include Sealmaster PN Gold bearings with stainless steel housing, a Skwezloc locking collar, and stainless steel end caps.
Success Made Easier: The new conveyor setup has enabled the plant to increase can production overall. Total annual profit (based on 50 extra cans per minute = $3,600 per day x 120 days of canning) is $432,000. Subtracting the cost of the new conveyor set-up ($6,280), the plant’s annual yield is $425,720.
In addition, the plant has eliminated the 36-hour periods throughout the year when production was halted and man-hours were wasted on reconfiguring the line (estimated to cost $37,800 in lost production and $900 in labor per changeover).
Contact BDI for more information on conveyor components and other BDI Solutions.