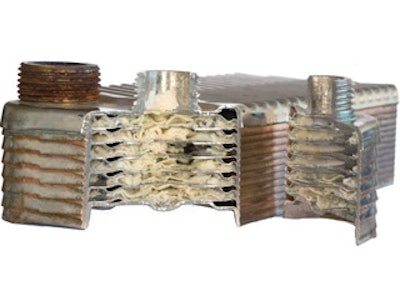
The deposition of material on heat transfer surfaces is called fouling which significantly impacts the thermal and mechanical performance of heat exchangers. Fouling increases the overall thermal resistance and lowers the overall heat transfer coefficient of heat exchangers as well as impeding fluid flow, accelerating corrosion and increasing pressure drop across the heat exchanger. The cleaning of fouled heat exchangers presents a significant challenge to maintenance and operation of heat exchangers in process industries.
The common fouling mechanisms are:
- Particulate fouling – resulting from sediment of dust, rust, fine solids, and other entrained solids.
- Crystallization fouling - Calcium carbonate is the predominant component of the hard and tenacious scale deposit from water and is particularly apparent in processes involving heat transfer. A concentration of dissolved solids by repeated partial evaporation of the water is the main factor that causes calcium carbonate scale. Even soft water will eventually become scale forming when concentrated numerous times, i.e. two, three, four, or even higher.
- Biological fouling – Occurs when biological organisms grown on heat exchanger surfaces. Problems arise from algae to other microbes such as barnacles and zebra mussels. At certain times of the year when microbes are said to bloom, colonies several inches thick may grow across the heat exchanger service affecting thermal performance.
- Chemical reaction fouling – This type of fouling occurs when the depositions are formed as a result of chemical reaction.
- Corrosion fouling - Results from a chemical reaction that involves the heat exchanger surface material.
Costs
Costs for extra fuel occur when fouling leads to extra fuel burning in boilers and furnaces or when other energy such as electricity or process steam is needed to overcome the effects of fouling. It is calculated that additional fuel and energy costs equate to billions of dollars each year.
Additional costs are attributed to maintenance charges for the removal of fouling deposits. Manufacturers of heat exchangers state that 15 percent of all factory maintenance costs are credited to heat exchangers and of that, 50 percent is due to fouling. Add to these costs of plant shutdown for days at a time and the effect of fouling is only too plain.
Cleaning:
There are now four popular methods of removing fouling:
- Mechanical cleaning which involves brushing and scraping
- Chemical cleaning which using solvent or chemicals
- High velocity cleaning using water jets
- Electronic water treatment
Electronic Scale Removal
Over the years, numerous white papers have been published around the world on the success of electronic water treatment in removing fouling in heat exchangers, including numerous white papers from Drexel University in Pennsylvania. Not only has this form of cleaning worked with rust and scale but also on biological fouling such as zebra mussels.
In process industries, it is common for chemicals to be added either because the water is being used for ‘scrubbing’ or cleaning, or to achieve a chemical mineral effect as part of the production process and thereby increase the scaling tendency. Scaling deposits are common in flowlines subject to changes of pressure or temperature. Regardless of how hard water effects are achieved, the outcome is the same. Scale formation results in reduced diameter or blocked pipes, reduced heat transfer efficiency, seized pumps, inoperarable valves, misleading meter readings and defective heating elements.
To explain the effect of electronic scale removal it is first important to understand the major factors that cause scale. Whilst scale can be a complex of many minerals, calcium carbonate is the most prevalent in industrial processes.
Super Saturation
Aqueous solutions can become supersaturated, which means that they contain higher concentrations of dissolved solute than their equilibrium concentration. Such solutions are not stable and are easily triggered into dropping back to saturation level, forcing the dissolved compound to precipitate. Even when a bulk solution is less than fully saturated, scale formation can occur spontaneously due to localized super saturation, at a surface for example.
pH Effect on Scale Formation
The pH of the solution is directly related to its acid content (typically carbonic acid). The higher the acid content, the lower the pH number. The solubility of calcium carbonate is directly affected by the pH of the water. If the pH of the water is decreased, more calcium carbonate solid can be dissolved. Conversely, if the pH of the water rises, it will force calcium carbonate out of solution and hence scale deposits will form.
Temperature Effect on Scale Formation
Gases in general, and specifically carbon dioxide, are less soluble in water at high temperatures. Therefore, as the temperature rises, the dissolved carbon dioxide decreases. This increases the pH of the fluid, reducing the solubility of the calcium carbonate and forcing the mineral to deposit.
Pressure Effects on Scale Formation
Carbon dioxide and gases in general are more soluble under higher pressure. Therefore, as the pressure drops, carbon dioxide gas will be forced out of solution, lowering the carbonic acid concentration. The rise in pH is associated with a drop in calcium carbonate solubility, leading to the formation of mineral scale deposits.
Electronic Water Conditioning
Electronic Water Treatment (EWT) is a non-invasive system utilizing a solenoid coil or coils wrapped around the pipework to be treated. A signal generator of which the frequency is continuously changed supplies current to the coils. The pulse shaped current creates an induced electric field, concentric around the axis inside the pipe. As a consequence to this arrangement, any charged particle or ion moving within the field experiences a so called Lorenz force generated by the interaction between charged particles and magnetic and electric fields. Research at a major University in Philadelphia confirmed that the Lorenz Force is unchanged, irrespective of flow rate. Generated magnetic fields have been measured and have been found to be below 1 Gauss, lower than the earth magnetic field strength. This technology overcomes one major disadvantage of permanent magnet devices, viz, that they work well only within a certain flow rate ‘window’ and that at higher and lower flows the performance drops to zero.
EWT products, such as the patented Scalewatcher, affect the formation of scale by increasing the homogeneous precipitation rate of calcium carbonate and certain other minerals. The ability to adjust power, frequency, and coil configurations on site enables performance to be optimized with no downtime and no pipe replacement.
Biological Fouling Is Also Successfully Treated With EWT
The impact of zebra mussels extends from the Great Lakes watershed to the mouth of the Mississippi River. The mussels affect industry by clogging pipes and intake structure. Crustaceans and zebra mussels are similar in the way they use calcium—a key component of pipe scaling. They both convert calcium in a free ion form to calcium carbonate to construct their shell or exoskeleton. A study undertaken by Aquatic Sciences, Inc. an international underwater inspection service, found that EWT technology was successful in removing calcium carbonate and thereby drastically reducing the level of zebra mussel infestation.
The fouling of heat exchangers in processing industries is a chronic operating problem. Costs due to additional fuel consumption and maintenance, loss of production, etc. have been estimated as 0.25 percent of the GNP of industrialized countries. EWT offers companies an environmental, effective, and cost saving method of reducing fouling on heat exchangers which can only prove a win, win, win scenario for all.
For more information, visit www.scalewatcher.com.