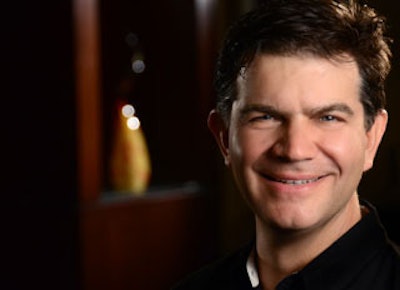
What if you could report to your board room that reducing scrap has increased your company’s profit by 10 percent? Or, what if you could show plant managers that exactly 15 defects occurred within a particular shift? Because quality affects every level of an organization — from the plant floor, to the C-suite, to the customer — it is far more than a cost of doing business; it is a game changer. However, not everyone in your company may understand the true value of quality, which may hinder your ability to justify investments in improvement projects.
To prove the value of quality, you need to increase the visibility of quality by providing the right quality metrics, to the right people, in the right format. When done properly, it is possible to turn manufacturing data into actionable information, or Manufacturing Intelligence, which can both demonstrate the value of quality improvement projects to upstream management, and result in ROI. Given today’s manufacturing challenges, quality metrics are more important than ever. For one, production is rarely a single-site operation and manufacturers rely on suppliers all over the globe to provide quality products. Other complexities, such as compliance with government regulations, siloed data, and the focus on customer satisfaction, lead manufacturers to rely on quality metrics to control and improve their products.
The first step in proving the value of quality is understanding what each department or staff member sees as valuable. To identify what data to collect, get input directly from each level of your organization, from the top down, and find out what metrics are important to them. For example, executives will want high-level summaries of data, such as percentages and raw data values, which help them determine areas of improvement, like waste reduction. On the other hand, plant managers require metrics such as Overall Equipment Effectiveness (OEE) or number of defects in a particular timeframe, which help identify costs and plant performance efficiencies. Lastly, operators also rely on OEE, as well as other more targeted metrics, like product-specific features and alarms for out-of-spec events.
Once you have gathered insights from the various departments, how do you know which data need to be measured? Metrics must be meaningful, and there are good metrics and bad metrics. Good metrics must be bi-directional, and serve customers both upstream and downstream. They should also be objective, customer-specific, and assist decision makers with real-time and historical data. Also, don’t worry about getting the perfect, high-end set of metrics right away – collect data, but make sure you challenge it. Identify where specific metrics fit in the process; if they are deemed no longer useful, there is no need to continue to measure them. Remember that just because something can be measured doesn’t mean it is important.
With the right blend of three things — people, process and technology — you can ensure the correct implementation of your quality system and quickly begin to realize ROI.
People: Be diligent in your efforts to demonstrate the value of quality to all departments of your organization; focus first on upper management and recruit the highest-level manager to be your champion. This person can help relay the importance of the quality systems to others at the company. Just as important, ensure buy-in and agreement from your plant operators. They are the ones who will deal directly with collecting the data on a daily basis, often before anyone else sees this information.
Process: It is important to remember that you won’t solve everything overnight, so focus on getting results within a manageable scope before expanding to other areas. Invest the time and resources necessary to set a standard for data collection up front and follow it. Identifying areas that will show fast, significant improvements will serve as quick success stories that add to your credibility.
Technology: Ideally, your quality system should be able to aggregate data from different sources into one, single location, or hub. With a centralized repository, rather than silos of disparate data, it is easy to collect, analyze, and report on meaningful, real-time quality data that delivers Manufacturing Intelligence. In addition, systems with mobile data collection and analysis capabilities offer extra value and convenience to executives on the go.
Because each department’s actions affect downstream successes, it can be beneficial to look for problems and areas for improvement beginning at the bottom, and work your way up to the top. Rather than focusing right away on corporate goals, look first at manufacturing processes. By capturing and promoting meaningful data and keeping it current, it is easier to “sharpen the saw” of quality and move these metrics up the chain to correlate with corporate goals. Showing upper management metrics that could help increase the organization’s overall profitability, such as cutting costs by preventing overfill, adds credibility to your quality program and proves the value of improvement projects for everyone involved.
Author Bio: Steve Wise is vice president of statistical methods at InfinityQS International (www.infinityqs.com), the global authority on real-time Manufacturing Intelligence and enterprise quality. A Six Sigma Black Belt, Wise focuses on ensuring proper use of statistical techniques within InfinityQS' software offerings and application in the customer base.