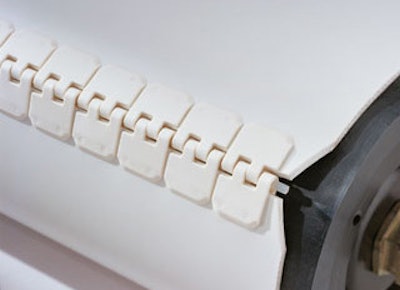
Still searching for ways to take your productivity to higher ground? One good way to do that is by getting all the uptime you can from the belt conveyors that carry materials, parts and finished/packaged products throughout your plant. Belt conveyors naturally demand a certain amount of downtime for maintenance and parts replacement, and keeping those events as seldom and brief as possible is what uptime is all about.
In most light-duty belt conveyor systems, one of the key factors in obtaining conveyor uptime is achieving the optimum belt splice. There are two major processes to choose from when splicing your belt: mechanical fasteners and endless splicing. Reviewing the available alternatives against the realities of your conveyor system will help you determine which type will serve your needs best.
Belting designed for light-duty applications has improved greatly in the past few decades, but has grown into many specialized variations. European influences have changed light-duty belting from the cotton plies and covers of the past to the synthetic belting of today. These styles offer higher efficiencies due to thinner, lighter construction with less drag and lower horsepower consumption. Generally built on polyester fabrics with binders or covers of various thermoset materials, today’s light-duty belting thicknesses range from about 1/4" (6.4 mm) down to an almost-paper-thin .030" (.76 mm), with working strengths from 20 to 200 P.I.W. (3.5 – 35 kN/m).
Endless splicing joins the two belt ends together either through heat or chemical activation, making the belt a continuous, endless length. The alternate method, mechanical fasteners, physically attaches a row of fasteners to each belt end. These fasteners are then meshed together and connected with a hinge pin.
Mechanical fasteners or endless splicing
Various types of mechanical fasteners are available, but all offer similar benefits when it comes to a quick repair. The splices are easy to install, long lasting, and reliable, requiring only basic mechanical skills and affordable tooling. Unlike endless splices, the wear on the splice is visually apparent, allowing maintenance crews to complete the repair during a scheduled downtime.
Mechanical belt splices also carry an advantage when it comes to splicing used belting. It is not wise to use endless splicing on a worn belt because the aging and wear of the belt make the splice susceptible to failure. With mechanical belt splicing, fastener splice strength is maintained without having to worry about contaminants like oils and dirt weakening the splice. In addition, mechanical splices offer the advantage of being hinged or separable. This feature allows the belt to be installed or replaced without having to disassemble the conveyor system or remove the belt from the conveyor structure. It also allows for easy cleaning of conveyor components by simply removing the hinge pin and pulling the belt ends apart.
An endless splice is very quiet in operation, will not mark the conveyed product, can operate over very small pulleys, and is a strong, long-lasting splice. Other than the fact that it is not recommended with worn belting, primary drawbacks are related to the downtime and cost of installing the splice with a traditional press. Unlike mechanical splices, which require only basic mechanical skills and simple installation tools, endless splices typically utilize a traditional press that requires highly-skilled personnel to install the splices with expensive equipment. Due to these factors, the vast majority of endless splices are installed by an outside crew — taking hours, if not days, to install a single splice. To avoid this lengthy downtime, many users will keep spare belts for emergencies. Since the belt is endless, the conveyor structure must be partially disassembled to install the belt, which again requires more downtime.
Newer technology, however, has made endlessing belts quicker and easier. Where traditional, water-cooled presses were large, bulky, and featured slow cycle times and multiple components, portable forced air-cooled presses (such as the Novitool® Aero™ Portable Splice Press) are just the opposite. The Aero Press, with everything integrated into the press, has truly revolutionized the marketplace by providing endless splicing in 7-12 minutes, without the lengthy set up and juggling of multiple components.
See part 2 of "Mechanical Fasteners or Endless Splicing: What Is Right for Your Belt Conveyor System?" here.