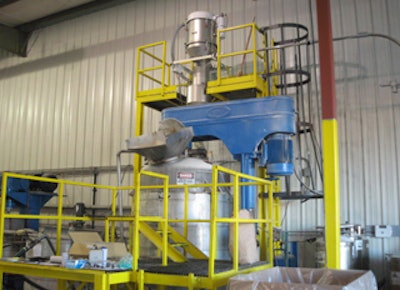
Explore the most common areas of increased profitability and safety when implementing a vacuum conveying system for the transport of bulk dry materials. Check out Part 1 here.
Using pneumatic conveying systems to eliminate ergonomic issues and potential costs associated with injury often results in increases in productivity. |
Back Injury
In the manufacturing arena, four out of five materials handling injuries affect the back and require a median of ten days for workers to recuperate. Using the $afety Pays worksheet, calculating with a five percent profit margin, a strain has indirect costs in excess of $33,000 and requires an additional $672,122 in sales to recoup those costs. Anytime organizations can eliminate the possibility of back injuries, injury costs should be taken into consideration when determining ROI.
While working on a major efficiency project that culminated in the building of new rooms for a blending area, a tea manufacturer wanted to also cut down the amount of lifting that the operators were doing manually in the production department.
Previously, the operators were manually weighing individual hundred-pound batches into barrels, using forklifts to transfer them to the top level, and then dumping them into hoppers by hand.
One of the biggest concerns for the tea manufacturer was the breakdown of the materials themselves. Pneumatic conveying is a very gentle way to move product and once that was proven to the manufacturer in the VAC-U-MAX testing facility; the system was designed to automate the process.
Now rather than operators using forklifts to bring barrels up to the mezzanine level, and manually scooping materials into the hopper, operators insert a wand into the barrels and product is pneumatically transferred from the wand to the blenders, eliminating all the forklift traffic and wear and tear of the workers’ backs.
In addition to eliminating ergonomic issues and potential costs associated with injury, the company had a 20 percent increase in productivity.
Fugitive Dust Control
Pneumatic conveying systems are fully enclosed, protecting materials from air, dirt, and waste. Because product does not escape from a pneumatic conveying system, particulates that can endanger workers respiratory health or settle on equipment and surfaces, posing an explosion hazard, are prevented from entering the environment.
Any time a pneumatic conveying system is employed, costs associated with housekeeping diminish as well as the potential for a dust explosion. Much could be written about combustible dust explosions and the benefits of pneumatic conveying systems; however, it should be made clear that the cost of employing even the most sophisticated pneumatic conveying system would be far less than that of a dust explosion.
Since the inherent nature of the pneumatic system prevents loose powder from becoming airborne, it makes for a cleaner and safer environment all around, and a greater number of organizations are looking at safety reasons for engaging a pneumatic conveying systems.
Several years ago, a manufacturer of cable faced a major materials handling problem – two of the fourteen ingredients used in its process were toxic. The ingredients were received in powder form in 50-pound bags, which were opened on the production floor, hatched on platform scales, and manually dumped into a mixer or blender. Despite extensive use of exhaust ducting and respiratory protection for the workers in the area, engineers were still concerned with the impact of toxic contamination on the environment and the threat of not meeting OSHA regulatory standards.
Indirect costs for a single dust disease, according the SP worksheet, are around $25,000 with an additional $509,000 needed in sales to recoup the cost. The worksheet lists other respiratory illnesses as well as illnesses associated that can be caused by dusty environments such as dermatitis. A single injury for dermatitis can result in indirect costs around $10,000 with over $200,000 of additional sales to make up for those costs.
A cable company eliminated the need to dump 50-pound bags of toxic material into a mixer manually by converting to a monorail-mounted hoist from VAC-U-MAX. The device lifts and positions semi-bulk bags to an unloader, which forms a dust-tight seal against the ring on the discharge opening. Agitator pads and an auger under the storage bin help to deliver material into a weigh hopper on the floor below at a controlled rate. The material is then conveyed to a blender on an upper floor.
The entire flow path is enclosed, resulting in a safer environment and because of the bulk packaging, the cost per pound of materials is lower. In addition, handling costs in receiving, storing, and discharging the materials are substantially lower.
Manual materials handling is the number one source of compensable injuries in the manufacturing sector. Many of those injuries could be avoided by employing a pneumatic conveying system – often for less than combined direct and indirect costs associated with those injuries. Nearly 100 percent of the time, solving a workplace hazard with a pneumatic conveyor system increases profit through production efficiencies.
To learn more about how VAC-U-MAX pneumatic conveying systems can improve efficiency, ergonomics, preserve product integrity, or reduce costs, write to 69 Williams Street, Belleville, NJ 07109; call 1-800-VAC-U-MAX (800) 822-8629 or (973) 759-4600; e-mail [email protected]; or visit www.vac-u-max.com.