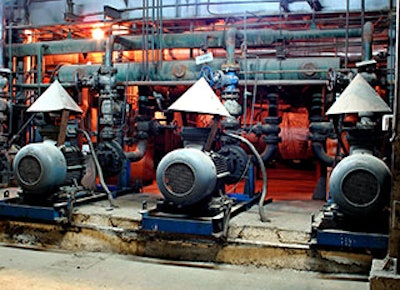
The electronic devices used to test and analyze electric motors and other equipment have become much more powerful than in the past. Yet, in many instances these sophisticated devices have also introduced a high degree of complexity for users, requiring that highly trained and experienced personnel perform the testing.
Many of today’s devices are feature-rich and capable of measuring and analyzing many factors, including surge comparisons, resistance, impedance and more. Unfortunately, not all of these potent systems are very user friendly, and some require a substantial investment – wth costs going as high as $100,000 for a winding analyzer, which also can be very complex and require highly trained personnel to operate and interpret.
Coal-fired power generation plants, hydroelectric plants, and other power generation facilities all require accurate motor testing. For municipal, commercial, and industrial generation and pumping equipment, a powerful portable winding analyzer and motor tester that is considerably lower in price, and is easy enough to use that highly trained specialists are not required to operate it can be a real boon.
Integrity Testing
For utility maintenance staff and motor shop staff – who all clean motors and install or service windings, an electronic analyzer is used to test the integrity of the motor windings to ensure that they will provide dependable performance.
Motors are often subjected to harsh conditions, including excessive heat, debris, or even occasional lightning strikes, all of which mean that windings have to be replaced. When a damaged or simply worn out pump and motor assembly is to be serviced, technicians disassemble and thoroughly inspect the motor. Windings are then cleaned, baked, and surge tested to make sure they are good. At this time, it is critical to be certain that all windings are good or six months later a motor could fail.
It requires a good analyzer to do a thorough test on the windings to make sure that they are sound. A unit that is user-friendly and can perform all needed tests is ideal, with varying options and output ranges from 4kV to 12kV, or even higher with additional power packs.
Using a reliable winding analyzer and motor tester is like an insurance policy; once a technician has run the tests and everything has passed, there is no doubt that the motor is good. After completing the tests, a good unit should be able to produce a printable report that can be used as documentation of what was found on the tests.
Power Plant Applications
From coal-fired power generation plants to hydroelectric plants and other power generation facilities, motor testers are a vital component for the repair and preventative maintenance of motors. Testers must be able to simulate or exceed usage conditions and parameters for accurate preventative forecasts.
Clark Myers, an electrician at Twin Oaks Power, L.P. (Bremond, TX) a division of Optim Energy LLC, has been using Electrom winding analyzers for several years at the coal-fired power generation plant. These testers use high-frequency 60Hz surge pulses eliminating ionization dissipation and thus better simulating what motors are subject to during operation.
“This is really the only testing and analyzing device we use for checking motors,” Myers says. “We also use it on the back of switchgear to ensure proper protection of the motor and the line. Typically this testing is done during a scheduled outage.”
Myers, a 35-year veteran of power plant construction and operation, adds that this tester is quite user friendly, and does not require engineering expertise or extensive training to operate it successfully. “I’m not what you would call an expert as far as instrumentation is concerned,” he says. “This particular instrument is pretty straightforward. Basically, the company just showed us how to use the device and ever since, it has been pretty much second nature.”
Friendly But Powerful
One of the big advantages of some of today’s most advanced instruments is that they are both easy to operate and interpret, but also contain powerful features.
They give users the ability to perform a variety of tests from the most simple low resistance tests to Megohm (also called insulation resistance), Hipot, and advanced Surge testing.
One of the key advantages is that they use a 60 Hz surge pulse frequency – the same frequency that many motors operate at. This high pulse rate provides a sufficient frequency to overcome ionization dissipation and can thus isolate insulation weaknesses with more sensitivity, predicting future faults before low frequency testers, and also better simulates motor operating conditions.
One of the most significant ease-of-use features is that they enable users to enter the surge test voltage, push a button, and let the machine run the test independently. Surge waveform ranges are automatically set for all models, which eliminates the need to specify configurations, push multiple buttons, or turn dials.
All-In-One Testing
All tests should be able to be done with one instrument, such as the iTIG II, and these should be available in manual or fully automatic models. No additional items should be required other than accessories, which can be added on at any time. Tests that can be performed should include Surge Comparison, DC Hipot, Step Voltage, Insulation Resistance (Meg test), Dielectric Absorption (DAR), Polarization Index (PI), Low resistance (Ohms), Impedance (Z), Phase Angle, Inductance (L), and Capacitance (C). Various models of the instrument need to have different features included, but all should be capable of being upgraded to any higher-level model.
For more information, contact Electrom Instruments, 1821 Lefthand Circle, Longmont, CO 80501; Phone: 800.833.1881 , 970.669.6609; email: [email protected] or visit www.electrominst.com.