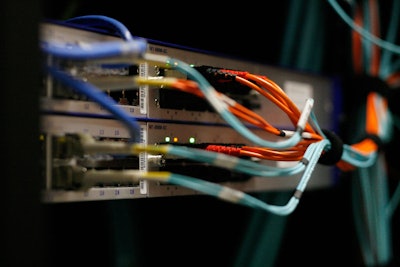
Johnson Controls’ Automotive Experience Group recently retooled its plant communications networks to improve responsiveness for its Just-In-Time (JIT) plants. A global diversified technology and industrial leader headquartered in Milwaukee, Wisconsin, the company decided it was time to upgrade its “one size fits all” flat network infrastructure, controlled by the corporate IT department, with a segmented system that addressed the separate needs of its IT department and plant engineers.
Joe Lavis, an IT manager in the Automotive Experience Group’s IT Process Office, together with Kevin Hooks (IT Director Manufacturing, Supply Chain & Quality Systems), proposed a new architecture that provided for separate office and plant networks, communicating through secure channels.
According to Lavis, the benefits of the new architecture are as follows:
- Higher availability through the a reduction of unplanned shutdowns
- Protection of production controls equipment from chatty office traffic and unannounced network scans, which have knocked devices offline in the past
- Complete production network ownership provided to the control engineers
- Reduction of line path costs (i.e. shorter runs to layer 2 infrastructure)
- Increased network efficiency through reduced bandwidth consumption by multicast traffic, thanks to switch management features
- Improved security and granular control of messages being passed between the IT and plant networks by using a firewall between the two networks
One Size Network Does NOT Fit All
Network strategies and objectives differ depending on the job. The IT department must place data integrity first. On the other hand, JIT production facilities live and die by keeping manufacturing lines up and running in order to meet production quantity, quality and delivery driven by electronic order requests sent by the customer. By maintaining separate networks, each group can operate at optimum potential.
There were three main challenges for the control engineers under the old network architecture:
- It was difficult to meet the “deterministic” requirements of a factory operation when IT “chatter” and network scans would consume needed bandwidth at just the wrong time. Unplanned shutdowns played havoc with tight schedules on manufacturing lines, particularly in a JIT facility. Factory systems do not tolerate randomness in the delivery of time-critical signals; an inopportune scan run by the IT department could provide just enough of a delay to knock a device offline. Manual intervention was required to reboot offline devices, causing further setback to the schedule.
- Network management was delegated to a 3rd-party operator. A Service Level Agreement (SLA) that suited the needs of the IT group governed the 3rd party’s response. When a port address or other network detail needed to be changed, the IT coordinators had to submit a change order. Sometimes equipment failed or lines went down while orders were in process.
- IT coordinators and controls engineers sometimes spent hours troubleshooting network interruptions, a costly exercise when there is a factory schedule to maintain.
Creating a Global Industrial Network Strategy
The isolated network strategy at Johnson Controls gives each plant its own control network infrastructure. Plants communicate with the corporate network through a firewall. This provides security for plant operations and keeps unnecessary or undesirable traffic (whether inadvertent or hostile) from affecting factory operations. Control engineers can add to, remove from or modify their infrastructure as capacity requirements change and can be more responsive to plant objectives. This is particularly important for meeting Just-In-Time customer requirements. Figure 2 shows the new control network architecture.
The plan included a consistent architecture for plants around the globe and required a global supplier and global access to technical support. McNaughton-McKay Electric Company in Madison Heights, Mich., and its partner, Belden Inc., were equipped to fill the bill.
In the new architecture, end devices or clients are directly connected to a Hirschmann switch on the ring. Rings are connected by fiber to a Hirschmann MACH 100 family device in the EDF cabinet, which in turn is connected to a fiber patch panel in the IDF that feeds directly to the MACH 100 switches in the Main Distribution Frame (MDF) with redundant fiber runs.
The actual costs of the hardware hardly changed; however, the accounting method did. The typical IT leasing model anticipates hardware refresh every three years or so. Industrial switches and routers are designed to operate in extreme environments for long periods of time. Changing them out every few years is not only unnecessary, but also an unwarranted expense. A hardened industrial network can be capitalized, and offer a rapid ROI.
Cabling expense and complexity were also reduced. The corporate network uses a star/tree structure, with direct runs from an Intermediate Distribution Frame (IDF) to client devices on the shop floor. This resulted in long cable runs and unwieldy cable bundles. The industrial network utilizes an EDGE Distribution Frame (EDF). This means shorter cable runs and the ability to use pre-terminated cables to connect Hirschmann switches and the end-devices. The result is lower wiring costs and easier troubleshooting.
The initial deployment is a part of the Northwood, Ohio, JIT plant expansion; future installations will be scheduled as new plants are built or when a major expansion with significant downtime is planned.
Turnkey Installation with Pre-Configured Kits
McNaughton-McKay brought in experienced field and R&D team members from Belden, along with its own resources, to assist in the first installation. The template designed for future deployments makes it possible for any group in the world to build out its own facility from a single parts list. McNaughton-McKay pre-configures kits that can be shipped directly to any plant. The kits contain Hirschmann switches and a firewall, and can include components all the way down to cabinet hardware and patch panels for delivery.
Maintenance costs have been reduced as well. Each site will have one of each switch flavor on cold standby, and McNaughton-McKay will ship kits and spares to their global distribution points. Technical support is supplied through a three-tiered structure. Tier one is conducted by locally-trained staff in each plant. A McNaughton-McKay support team makes up the second tier and escalates any intransigent challenges to tier three, a Belden support team.
Conclusion
Corporate IT and control engineers both have an overarching objective of making their company as efficient and effective as possible. Nonetheless, each group has different priorities and different network requirements. Defining and deploying an Ethernet-based industrial network system that integrates easily with the IT network through effective firewall protection can significantly improve plant performance and add to the corporate bottom line.