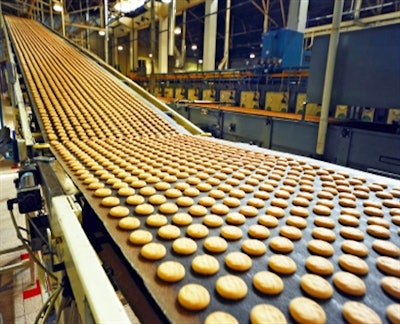
It is critical to plan for the future when designing your food processing plant’s mechanical systems. We find that many plants are now undergoing expensive retrofits because future needs were not appropriately considered. Not only are retrofits expensive, but if new equipment is not sized and sequenced effectively, it can significantly affect your energy costs. To avoid these issues, here are four budget considerations to address when designing your plant’s mechanical system:
- Plan for any future plant expansions during the initial design phase. Look at your business plan and consider future production needs, including additional and expanded product lines. Begin with an initial analysis of the building structure and allow for additional square footage to add new boilers, compressors and production space. You may also consider buying larger compressors up front that will provide additional capacity needed in the future. Using variable frequency drives (VFD) will allow you to manage energy usage during lower production periods.
- Consider long-term ROI during the initial design phase, not just upfront costs. Your mechanical engineers should be able to provide side-by-side analyses of the long-term operational costs for most of your machines. Consider pairing a chiller with your HVAC system for long-term cost savings. Gas is the most cost-effective fuel to run your plant’s processes. If gas is not available to your facility, consider making the investment to bring gas lines in. Retrofitting existing water heaters with gas later on can prove to be significantly more expensive.
- Choose the appropriate materials that will save you time and maintenance costs in the future.Stainless steel equipment may be more expensive but is often the preferred material to sustain harsh wash downs in a food processing plant. You’ll save in both replacement and maintenance costs in the long run.
- Ensure that you invest in the appropriate quality of water for your plant’s processing and sanitation needs. If the water in your area is hard or contains chlorine, you’ll want to install purification systems where the water enters the plant. Again, there will be an added upfront cost but treatment costs may prove to be more costly down the road.
More and more food manufacturers are developing energy management and resource conservation programs, focusing on water and heat as the two resources that offer the greatest opportunity for significant savings in the long run.
Water
Conservation – Water is the most important, and most wasted, resource in a food processing plant. It’s also one of the easiest resources to conserve. Most water loss occurs during the sanitation process. By installing flow restrictions, such as high-pressure, low-volume nozzles on spray washers, a plant can significantly reduce the amount of water used and lost during washdowns.
Purification – Installing water softeners or filtration systems is one of the easiest, most cost-effective solutions to purify water and reduce energy usage. In addition, the more you treat the water, the less makeup water required for most processes. Cleaner water also helps to minimize wastewater and the expense of treatment at municipal facilities.
Reuse – Steam is used to process most functions within a food plant. As a result, capturing and reusing this valuable resource can lead to significant cost savings. Low pressure waste steam from boilers can be captured and reused to power a number of processes within the plant. Water from many functions within the plant can also be captured, treated and reused.
Heat
Recovery – There are many waste heat sources within a plant from which useful heat can be recovered and reused. For example, waste heat from compressors can be captured and used to pre-heat make up water for the boilers.
Auditing your facility on a regular basis is the most important step you can take in effectively managing your resources. An energy audit can spot leaking water hoses, leaking pipes where compressed air may be escaping, and many other small fixes that offer huge paybacks.