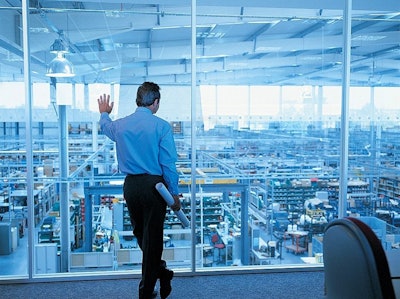
Manufacturing is a giant puzzle. The pieces are constantly moving, the regulations are constantly changing, and the challenges are constantly coming.
Every day, plant planners are expected to solve extremely complex puzzles – which operation will run on which line, how many of each part needs to be produced, how will each step happen at the right time – and they often lack the proper tools to do the job.
Quintiq is a company that was founded to help solve manufacturing, logistics, and workforce problems. The Quintiq supply chain planning and optimization software operates on a unique algorithm which was created under the vision and direction of CEO Victor Allis. “At the heart of what we do is single planning platform that allows us to solve real life planning puzzles for our customers,” he says.
Allis wanted to prove that their product was world-class, so they set out to break some world records. And they did – 98 world records to be exact.
The Flexible Job Shop Scheduling Project
As described by Quintiq, the Flexible Job Shop Scheduling Problem (FJSSP) is an extension of the classical Job Shop Scheduling Problem (JSSP). The JSSP is based on the assumption that only one machine is able to run a particular operation. The FJSSP, as its name suggests, assumes a more flexible setup. It reflects a production environment where it’s possible to run an operation on more than one machine. Though the specifications vary, the essence of the problem remains the same – you must assign all operations to machines in sequence (respecting the sequence of operations in each job) so that the total completion time (aka makespan) is minimized. Over the years, academics have published hundreds of iterations of this thought experiment.
“What academics have found many years ago is that these problems can get very complex very quickly because, for example, one of the machines may be a bottleneck, but all of them need to go through it,” explains Allis. Planners and academics started to make manual planning boards and Excel sheets to determine the optimal solution, but even with a small number of operations, the problem became too complex. So algorithms were created that took into account bottleneck theory, optimization techniques, and mathematical optimization to speed up the puzzle solving.
The Quintiq team applied their standard software to all of the FJSSP examples that they could find in literature. In 98 instances, the Quintiq optimizer set the world record for best solution.
While the FJSSP is an abstract puzzle, the Quintiq optimizers that were used to set the world records are used in real factories all over the world, solving these same problems every day. “We found that in actual manufacturing, you not only need to solve the puzzle once and then just execute, but you need to constantly revise your solution based on unplanned things that happen – the shop floor not starting up on time, a furnace burner not firing up as well, and all of these little deviations,” says Allis.
Their clients include some of the largest companies in the world. Some of the top global aluminum producers, including Novelis, Alcoa, and Hydro, use Quintiq software to keep their lines running efficiently and profitably. Walmart uses their software to coordinate all of their trucks in the U.S. (that’s about 7,000 trucks and 20,000 loads a day). And the FAA uses their software to ensure that air traffic control runs smoothly around the world.
How Good Is Your Plan?
Manufacturers are always trying to optimize their planning process to ensure greatest efficiency and minimal downtime. But how do you know how good your plan is?
“You should realize, that in most cases, when you make a plan for your factory, most people do not assess how good that plan actually is,” Allis explains. If you asked your plant planner today how their plans stacked up, would they know? Probably not, and they will likely feel challenged by your asking.
Many planners operate with very few tools and even less time, so the task of evaluating their plans may seem like a luxury that they don’t have. “Some companies have a very small plan and [the planner] is doing a great job and there isn’t much that he’s leaving on the table. But we’ve also seen cases where we’ve done similar assessments, and we find that [the planner], every single day, makes a bad plan simply because it’s too difficult to do with the tools that he has,” says Allis.
Allis uses a jigsaw analogy to explain this challenge. It’s as if the planners are asked to solve the jigsaw puzzle with only part of the pieces, the lights turned off, and no example picture. Giving the planner proper tools is like giving them back the rest of the pieces, turning the light back on, and handing them a template.
“It’s almost never that the planners aren’t smart enough, it’s that what we are asking them to do is solve a very difficult puzzle with very few tools,” says Allis. When the proper tools are given, “we can see that the same planner suddenly just makes better solutions.”
Where Should You Start?
To solve your own production optimization puzzle, you need to understand all of the pieces. Just like when you’re solving a jigsaw puzzle, it’s important to lay all of the pieces on the table. Start by looking at your inputs, your raw materials, what you’re trying to achieve (typically orders that you need to fill), what resources you have available, and what they can and cannot do. These pieces also include rules of business, like compliance regulations and what certain machines are allowed to do.
After you’ve laid out all of the pieces of the puzzle, you need to evaluate why it’s difficult. Where do you spend your time? What makes it complicated? How are you currently handling the problem? Is that the best option? Companies like Quintiq help evaluate these questions. Once clients are set up with the optimization software, they can run day-to-day operations self-sufficiently. But questions like these will continue to come up as a company expands, adds new machines, or changes product focus, so it can be beneficial to have a professional support team to help navigate these waters.
The Bottom Line
At the end of the day, better tools can help companies leave less on the table. Every company, no matter their size, should be evaluating their production plans. Having them reviewed by multiple individuals, including professionals if possible, can help optimize your process to ensure maximum efficiency and minimal downtime. Investing time and resources now to address these questions is a smart decision in the long run.
If you have comments or questions about this article, or would like to be featured in an upcoming article, please contact me at [email protected] or on Twitter at @TalesFromTia.