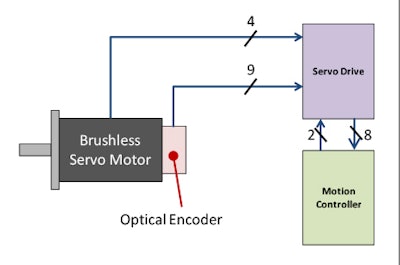
Over the past 25 years, improvements to motor feedback technology have allowed servo system manufacturers to reduce costs and provide products that are simpler, more reliable, and more accurate. New network communications technologies are now enabling the next set of breakthrough innovations in feedback device technology.
Advancements in Electronic Motion Control Systems
Prior to the late ‘70s, electronic motion control in factory automation was almost exclusively the domain of computer numerical controller (CNC) systems. It was at this time that builders of electronic motion control systems focused on robotic control and general motion control.
Position and velocity feedback for the early electronic motion control systems typically consisted of a tachometer for speed feedback and an optical encoder for position feedback. During the mid ’80s, hall-effect sensors were added to provide commutation information as brushless servo motors became popular.
However, since these motor feedback systems were extremely susceptible to electromagnetic interference (EMI), the end user was likely to experience faults and positioning errors if complex grounding and shielding techniques weren’t implemented
In an effort to minimize wiring complexity and noise susceptibility, several important innovations emerged, including:
- Use of differential line driver-receiver technology
- Integration of commutation tracks into encoders
- Use of higher encoder resolutions and digital signal processing to derive high-quality speed feedback
These technical advances resulted in the configuration shown in Figure 1.
Although an improvement over previous systems, the servo system in Figure 1 still has some important shortcomings:
- Machine uptime is reduced since encoder position information after power cycles is lost and machines have to be “re-homed”
- Higher encoder resolutions generate higher encoder signal frequencies, which are more susceptible to EMI
- Redundant position information is not available for systems requiring safe operating modes
- The servo drive interface consists of two multi-conductor shielded cables, which usually require expensive multi-conductor connectors at the motor
Inception of High-speed Serial Communication
Most recently, the availability of high-speed serial communications technology has enabled motor feedback encoder manufacturers to solve most of the problems previously described. Using high-speed serial communications technology, motor feedback encoders can reliably transmit the following information:
- Absolute multiturn position information
- Up-to-date high-resolution position information (at 10-20 microsecond intervals) synchronized with servo drive control loops
- Redundant position information for safe operating modes
- Motor “electronic nameplate” parameter data
- Motor rotor position and thermal sensor information
Since most servo drives are not designed to support pure serial feedback, encoders with high-speed serial communications capability typically provide incremental sine/cosine position feedback signals. Interpolation techniques are usually applied to these incremental sine/cosine signals to obtain a high position resolution.
Power Line Communication Eliminates Cables
Power Line Communication (PLC) technology is the transmission of communications data on power line conductors. It eliminates the need for specific cables by superimposing communications data on existing power conductors.
In the case of electric drive systems, there are two primary sets of power conductors: high-voltage 3-phase AC motor power conductors and low-voltage conductors for the encoder DC power supply. The reliability of today’s communications protocols and current cable shielding technology allow the serial communications encoder power/data signal to be placed in the same cable as the 3-phase AC motor power signals. By combining these technologies with servo drives capable of operating with serial data-only (no incremental feedback signals), it is now possible to completely eliminate motor feedback cables from electric drive systems (see Figure 2).
Separate Power and Communication Signals with 2-Wire Interface
In Figure 3, encoder power and serial communications are superimposed on the two conductors on the right-hand side of the circuit. This 2-wire encoder interface features an off-the-shelf pulse transformer and transceiver unit, which are used to separate the power and communications signals. These signals are then routed to the FPGA or ASIC that manages motor feedback and control loops.
The transceiver/pulse transform components replace the expensive analog-to-digital converter electronics previously required. The interpolation electronics are now located within the encoder so that high-resolution position information is available before it is converted to serial data.
Single-Cable Drive Systems Benefit Manufacturers and OEM Machine Builders
Servo system manufacturers will likely demand that encoders support 2-wire feedback technology and machine builders will likely demand that servo systems provide a single-cable connection between the servo drive and servo motors.
Advantages for the Machine User
- Reduces the machine cost
- Increases reliability by reducing the number of cables and interface connections
- Reduces the time to diagnose electric drive system problems and replace faulty or damaged cables
- Reduces the number of spare parts and cables to keep on hand
- Reduces the likelihood of errors when replacing cables and electric drives
Advantages for OEM Machine Builders
- Reduces the cost of the electric drive system
- Reduces the time required to cut cables to length and terminate at the electric drive
- Eliminates possibility of connecting feedback and power to different drive
- Reduces size of machine by allowing smaller cable tracks and cable troughs
- Increases reliability by reducing the number of cables, interface connections, and special tools required to terminate cables
- Reduces number of spare parts to stock
- Reduces time to identify and fix problems during start-up
- Reduces time to route cables into control enclosures
Advantages for Electric Drive System Manufacturers
- Reduces cost and size of electric drive (fewer signal connections and no A/D converter)
- Reduces cost of motor by eliminating feedback connector
- Reduces number of parts in inventory
- Increases reliability by reducing number of interface connections
The Future of Single-cable Electric Drive Systems
The technology to implement reliable single-cable electric drive systems is now available at an affordable price. By eliminating separate motor feedback cables, single-cable electric drive systems are able to provide a more reliable solution that reduces costs, inventory and installation errors. The advantages of single-cable technology will become increasingly important to electric drive (servo or VFD) manufacturers, OEM machine builders and machine users in the coming years.
For more information, please visit www.sickusa.com.