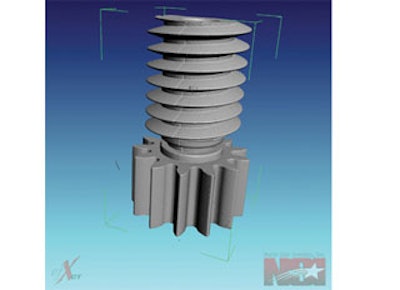
The performance of molded polymer gears continues to improve with new design solutions, improved materials, and higher accuracy molding.
Medical designers now use molded polymer gears more often to solve challenging product requirements, especially with regard to miniature and micro-miniature mechanisms. Plastic gears can provide a high torque, high speed, cost effective solution for a host of needs. Currently, Kleiss Gears produces miniature gears that spin at 200,000 RPM, gear trains of 1200:1 reduction ratio that are the size of a thumb tip, and metering devices for disposable delivery systems that are worn by the patient. A manufacturer may find it difficult, if not impossible, to achieve such applications with cut metal gears — and cost would be exorbitant.
Plastics have numerous advantages over metal for miniature gears. One significant advantage is that molded gears can be smaller with higher accuracy than metal gears. Cut gears reasonably reach only about 200 DP or .125 module. We have been able to achieve molded gears 50% smaller than that, with length-to-diameter ratios that would make cut gears cost prohibitive.
The molding process can also help solve problems associated with parts handling, inspection, and assembly, which become increasingly difficult the smaller the gears become. We integrate these subsequent steps into the manufacturing process as full automation to achieve the required accuracy and cleanliness. After the gear is molded a robot removes it from the mold. A camera detects part presence and confirms an approximate shape. A robot can then drop the gear in a bin, place it in a blister pack, separate it for further inspection, or present it to automated assembly equipment. This handling choice is very important, because micro-miniature parts can be very hard to re-register in an automated system once they have been released.
A gear manufacturer will likely discover that inspection of very small parts is technically challenging. For example, a gear tooth that is 0.25 mm whole depth should have approximately 2 µm flank accuracy. Physical scanning with touch probes (even very small touch probes of 0.2 mm in diameter) can still appear relatively large to such a very small gear. This translates to an inability to scan the root between gear teeth. Vision inspection systems measure some features quite well, but are not a complete answer. Molded edges are almost never sharp, and accurate inspection requires edge detection, because micro parts must have micro tolerances.
For additional reasons, measuring a 3D shape, such as a molded worm gear, can become an overwhelming challenge. One tool that is emerging as a possible solution is 3D computer tomography (CT) scanning. This technology provides a 3D image of the gear and can reveal a wealth of unique information:
- Voids and micro-voids can be detected.
- Physical attributes such as fiber alignment and surface finish can be determined.
- Although the present limits of accuracy are around 10 µm, the outside and inside surfaces of the part can be physically mapped and measured for general conformance.
CT scanning provides unique information, but to assure part quality, an inspector must use high-precision profile scanning and roll testing. Even a large plastic gear must be inspected carefully and the results considered judiciously. Plastic is a soft material, and the pressure of a small probe may easily indent the material and indicate a size smaller. For this reason, our company profiles gear teeth with small probes at very light forces to determine the actual physical size of the gear.
We then roll test the gear against a precision steel master gear by placing the two gears against each other with light force, and record the center distance between them during one complete revolution. We can see the result of the total form of the plastic gear in action against another precision form, as well as any deformation. We recognize flash or other anomalies on the gear. Misalignment of gear-to-axis will result in increased center distance. Then we move back to profile inspection and discover the cause of any increased center distance.
In metrology, a fundamental truth is that you cannot inspect what you are not looking for. Combining the two inspections of profile scanning and roll testing allows a search with more open eyes.
Another method of inspection is referred to as inspection through testing. Transmissions are by nature complex mechanisms with intense interactions between components. One could spend large amounts of time and energy inspecting individual components and still end up with a non-functioning device, because he/she never looked for failing features. Building the transmission and an automated tester for that transmission can readily solve the problem.
Drive the transmission with a calibrated motor; put on a regulated load; and sense the torque, speed, efficiency, and compliance under load. This produces a signature of the operating functionality of the unit. In the design phase, this will confirm or repudiate design expectations. In production, a continuation of the test on the product line will confirm system functionality.
Plastics and plastic gears bring a new opportunity to the medical device market, but they also bring challenges and new requirements for confirming accuracy and functionality — especially in the micro-miniature world of gearing. Although new tools for production, inspection, and testing are continuously being developed, the real challenge is being smart enough to use those tools effectively for smaller and stronger plastic-molded products.