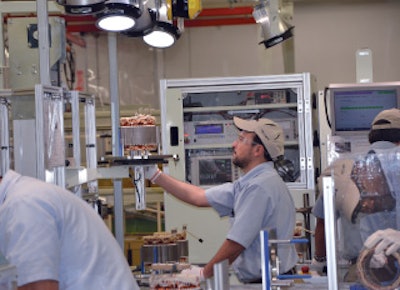
This article first appeared in IMPO's June 2013 issue.
Many don’t think of Toshiba as an American-made brand, especially when it comes to the U.S. automotive market. And for quite some time, that was true. Since 2003, Toshiba had manufactured hybrid electric vehicle (HEV) motors for Ford Motor Company at its Japan facility. But in 2011, under the weight of supply chain pressures and growing currency risks, Toshiba Industrial Corporation began manufacturing motors for Ford’s hybrid vehicles in Houston, TX. The U.S. HEV plant today produces 130,000 motors annually and employs over 100 American workers.
Planning Ahead
A wholly-owned subsidiary of Toshiba America Inc., Toshiba International Corporation (TIC) already had facilities in Houston, making it a “prime location,” says Matthew Bates, HEV plant manager. Other locations were considered, but TIC ultimately chose Houston for a variety of reasons. “Houston has one of the most talented and productive work forces in the country, and its strong economy and low cost of living helps businesses attract and retain top talent from across the country,” explains Bates. “This current environment makes Houston an ideal place for future business growth.”
While some American auto buyers are ‘buying American,’ TIC and Ford were also looking at the supply chain and examining risks when deciding whether to shift HEV production to the U.S.
Explains Kristina Adamski, Ford Manufacturing and Purchasing communications manager, “Ford’s strategy is to source from where we build. In this case, Toshiba had a footprint in Houston and it was faster for them to utilize their existing facility than to build a new plant. U.S. production of the hybrid motors and generators allows Ford a cost savings on logistics and helps with currency risk.”
Adds Bates, “Anytime you pick up and move your operation, especially one as complex as this, you take a chance of disrupting your supply chain due to focusing so many resources on the large move.” “Toshiba has very high standards and a very high quality product, and we took special care to make sure this was never affected.”
An American Move
TIC was now facing the issue of having zero automotive experience at its Houston facility. “This was very new to us and we didn’t really understand the full process of what we were about to do or what we were getting ready to undertake,” says Bates. Countless meetings between Houston and Japan ensued—and thousands of hours of preparation began.
“Between us in Houston and a team in Japan, we worked very closely together to start planning the equipment, the layout, the facility, how we were going to arrange everything, and figure out how we were going to get the plant up and running.” And a big part of the planning involved the workforce that would be necessary to move, ramp up, and maintain HEV production in the U.S. “We knew we needed about 100 people,” explains Bates, “and at the time we had three.”
While the Houston TIC facility already housed over 1,000 trained employees in its other plants, which include adjustable speed drive and induction motor production facilities, the other facilities couldn’t spare that number of workers for the new HEV operation. Bates and the three-person HEV team started with 15 people from the other Houston TIC plants, people who he says “had the right attitude, the right personality, and the work ethic that represents what Toshiba believes in.”
An additional 20 people were hired from outside the company and given two weeks of training on the fundamentals of motors, the manufacturing process in Japan, and Japanese culture, Bates says. After those two weeks, everyone left for Japan for about four months to learn how an HEV plant was run. Once everyone felt like they had the “fundamentals down,” TIC shipped all of the equipment to Houston. “We tore everything down, shipped it overseas, and then we set everything back up in Houston at our new facility,” says Bates. The workers returned to Houston, along with a dozen Japanese workers who would continue to help train the employees back in Houston. “We probably built about a million dollars of parts that we scrapped just so we could make sure that we perfected the process before we started shipping to our actual customer,” says Bates.
Up And Running
Working on ramping up HEV manufacturing in the U.S., TIC hired about 30 people outside of the company in 2011. Between January and October of 2012 is when the plant “staffed up,” explains Bates, and at the end of 2012 is when the plant was fully staffed at two shifts. Today, the Houston HEV plant employs 120 workers.
At the HEV plant, new hires go through a training process that takes approximately three weeks before they actually start working on the production line by themselves. “First, we introduce them to Toshiba and the HEV plant,” explains Bates. “We educate them about culture of our company and the sub-culture of our plant. This is probably more important than teaching them about the product or the process—it establishes the foundation for what we are ultimately trying to accomplish.”
The next phase consists of product training and employee evaluation to determine where they will best fit in the operation. And lastly, training moves to the actual process of where they will be working. “There is significant classroom training and shadowing of workers to make sure they understand all the ins and outs of the process,” says Bates. “Once they have been tested and are fully qualified, they can begin working on their own.”
The evaluation to determine where the employee will fit in the operation involves “training tools” that appear to be a game but provide critical information about the innate skills and characteristics of a person “so we can fit them in the right station in our manufacturing facility,” he explains. “Each operation requires a different set of skills that is easier if someone naturally has those skills. ”
Watching how someone completes a pegboard game, for example, displays their problem solving skills, explains Bates, and a person with natural problem solving tendencies might be a good fit working on an operation that involves a complicated machine. “Other stations don’t have any equipment, but it’s basically a quality control station and they’re visually inspecting something. So you want that person to be very detail-oriented.”
Quality First
“Quality is engrained in all of our employees from day one,” says Bates. “If you were to casually watch any of our operators, you would assume they are building a part or operating a machine. But with a closer look, you will see that about 50 percent of what they are doing is part inspection.
Quality is at the center of TIC’s culture, explains Bates, and what everything else is developed off of. Every process, every change is judged by how it will improve quality or how it will maintain the quality of a product. “And we instill that in all of our employees from day one.” By teaching new employees about Toshiba, about Japan, TIC demonstrates the importance of quality.
“The training that we did and focusing on building a positive culture are the two things that make this plant a lot different than other startups,” adds Bates.
“Every operation has a substantial portion of the cycle time dedicated to quality checks. This ensures that by the time the part travels to the end of the production line, we are packing a perfect part that will be delivered to our customer each and every time.”