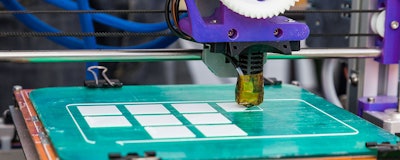
As the additive manufacturing (AM) industry continues to grow, expand, and generate more interest, it is important to understand how to protect workers from injury or illness associated with the various hazards of the additive manufacturing (AM) processes. This article is a primer to explain many of the known hazards as well as providing general control measures. This information is applicable to companies that are just beginning to get into the AM industry as well as lab-sized operations and for current companies as they mature in the industry. The AM industry is still developing with new materials being used and new processes being proven so the hazards and control measures will change as more is learned and as the industry develops and matures.
(This is the second part of a two-part series. Read part one here.)
Post-Production Processes Hazards And Control Measures
The various post processing operations can be, generally, grouped per similar hazards and their respective control measures.
The first-group of processes include those involving the “normal” machine shop-style processes including machining, final machining, and final milling with machines including lathes, drill presses, CNC machines, and similar machines. Proper training on the specific use of each piece of equipment is essential. The training should include the proper use procedures, safe work practices, and the proper use of PPE. Other procedures include the Emergency Action Plan.
These machines have similar hazards to include rotating parts, flying material chips or dust, and possible material kickbacks. Engineering controls such as machine guards are required for hazard reduction and control. Workers need to know how to properly shut down the machine, de-energize the machine, disable all power sources, and verify the machine is in a safe state to be worked on. Safeguards or machine guards should be in place to protect workers from contact with the rotating parts and hazards associated with the point of operation. Ventilation will control the airborne dust and proper clamping will prevent kickback. Wear the proper PPE such as safety glasses or goggles and face shield.
Testing involving both destructive and non-destructive tests have many hazards. Hazards include the equipment used in destructive testing to apply pressure, forces, twisting, cutting, high pressure air or fluids with the resulting pieces potentially coming loose from their clamping devices, flying objects, and sharp edges. Control measures include enclosing the area in which the testing will be conducted to contain any loose or airborne parts. At a minimum, personal protective equipment may include safety-toed shoes, gloves, and hearing protection. Hazards associated with non-destructive involve the specific type of testing such as radiation, electrical currents, and lasers. Following specific regulations for the use of radiation and lasers as well as industry standards is recommended to determine the specific control measures.
The post-production processes consist of acid baths and cleaning using acid or alcohol. The use of hydrochloric, sulfuric, sodium hydroxide, or phosphoric acid-based chemicals are used for cleaning of the parts or for removing support structures used during certain Additive Manufacturing processes. Hazards are those basically present when using the chemicals such as having the chemicals contact the skin or get into the eyes, spilling or being released into the work area. Control measures include having SDS available, wearing the proper PPE such as goggles and a face shield, apron, gloves, protective sleeves and having no exposed skin, potentially respiratory protection, having procedures on handling these chemicals, having emergency eye wash and showers available, and providing training on the use of and neutralizing of the acids.
Another grouping includes that of polishing and surface finishing operations. The hazards include absorbing polishing compounds into the skin with the very small particles. These same small particles can become airborne and be inhaled. Workers should wear respiratory protection if there is no ventilation system in place. Barrier creams may be used prevent skin absorption of metals and chemicals. These same small particles can get into the eyes so wearing safety glasses or goggles and a face shield is recommended when power buffing. Inhalation of vapors and metal particles can be prevented with the proper use of respiratory protection.
The group that includes heat treating, stress relief, and Hot Isostatic Pressing (HIP) have potential hazards including hot surfaces and liquids in various temperatures during cooling or quenching processes. Liquid quenches normally involve the use of mineral oils, water-based solutions or molten salt, circulated gases or forced air, or involve cooling in still air. Quenching operations pose various health and safety hazards to include exposure to chemicals, working in high temperatures, and the risk of fire or explosion.
Hazard controls for heat treating, stress relief, and Hot Isostatic Pressing (HIP) include the use of PPE such as a face shield with safety glasses or goggles, gloves, and heat-resistant protective clothing when working with hot metal. Quench oils may be very hot (above 100°C) and oil temperature increases during quenching. Splashes or skin contact cause burns. Avoid skin contact with oils by using gloves and protective clothing. Check that all safety devices, such as automatic shut-off valves, air switches, and exhaust fans are working properly before operating a furnace. Ensure that quenching areas have enough ventilation to keep oil mists at recommended levels. Follow the manufacturer's instructions when operating the furnace. Stand to one side when lighting a gas- or oil-fired furnace. Ensure that water does not contaminate the quenching oil.
Other Safety Concerns
Other safety concerns with the chemicals, equipment, and other materials used in additive manufacturing (AM) processes include the current practice of the storage of the chemicals in small lab-sized containers. As the industry grows and expands, the parts made will become larger and AM equipment will increase in size and capacity, this increases the amount of materials needed which increases the size of the storage containers from the current lab-size containers. The largest containers could include hoppers or silos at production facilities or manufacturers requiring material handling. Materials, at some point, may come in boxes larger than current lab-size boxes that would require the use of forklifts to handle materials in larger containers which requires the training and certification of forklift operators.
Another safety concern is that of repetitive motions to load and unload objects from containers and machinery in potentially awkward positions using awkward and forceful grips. Engineering out the hazard is the best means of control by using lift tables, angled tables, shallow boxes, and job rotation (though not an engineering control). Training should be provided on ergonomic issues to reduce the need to be in awkward positions, reduce the use of awkward grips, and the proper use of the lift tables and similar equipment.
A hazard that is related more to thermoplastic and AM is that of nanoparticles. Nanoparticles are of concern because they are very small, have large surface areas and can interact with the body’s systems, including the skin, lungs, nerves and the brain. Control measures that can be implemented include the use of ventilation, performing operations in an enclosed area, glove box or hood. The use of respirators that are in the 100-class are recommended. Wearing of a lab coat and impermeable gloves then keeping these items limited to use and storage in specific nanomaterials use areas will reduce the exposure outside of the area.
Summary
This article very basically reviewed hazards and control measures associated Additive Manufacturing (3D Printing). As the industry develops and grows, the number of companies involved with the industry will increase as will the number of workers potentially exposed to hazards discussed above. The necessary control measures to protect workers need to be implemented effectively.
This article was condensed from a White Paper prepared by Wayne Vanderhoof CSP of RJR Safety Inc. To get a copy of the White Paper titled “Additive Manufacturing Safety”, contact Wayne Vanderhoof.