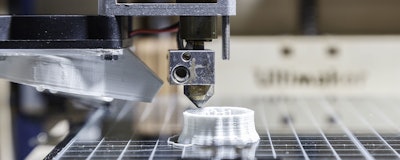
As the additive manufacturing (AM) industry continues to grow, expand, and generate more interest, it is important to understand how to protect workers from injury or illness associated with the various hazards of the additive manufacturing (AM) processes. This article is a primer to explain many of the known hazards as well as providing general control measures. This information is applicable to companies that are just beginning to get into the AM industry as well as lab-sized operations and for current companies as they mature in the industry. The AM industry is still developing with new materials being used and new processes being proven so the hazards and control measures will change as more is learned and as the industry develops and matures.
Brief Explanation Of Additive Manufacturing
Additive manufacturing has many names though the most common name is 3D Printing. It can be described as “…the sequential layering of material to create multi-dimensional objects.” (SMC Working Parts 11/2015) The term Additive Manufacturing (AM) is becoming the term used by those working to develop an identity for the industry.
Materials used in additive manufacturing (AM), generally, are polymers, metals, and ceramics. Some of the polymers used include ABS, polycarbonate, nylon, polypropylene, and silicone. Some of the metals, mostly in powder form, include titanium, aluminum, Inconel, and nickel. The ceramics used include silica/glass, porcelain, and silicon carbide. Some binders used in the various processes include chromite and zircon. Gases used during some of the additive manufacturing processes include helium, argon, and nitrogen.
Post production processing includes tasks involving cleaning using an acid bath, polishing, heat treating, machining, surface finishing, removing support structures, inspections, and destructive or non-destructive testing.
With additive manufacturing briefly explained, the general hazards and control measures can be described.
Mechanical Hazards And Control Measures
The first type of hazards are the mechanical hazards associated with the various AM processes. There are similar hazards among the various AM processes as well as some hazards associated with just one process. The mechanical hazards include UV light/lamp, laser, electron beam, plasma arc, air for drying, heater elements, heated surfaces, operations done in a vacuum, and oxygen-reduced (inert) atmosphere.
Most of these hazards are addressed with the actual work area of process equipment, “printers”, being self-contained and the point of operation protected with a door or gate that is interlocked to disable the machine operations if opened, by-passed, or otherwise disabled.
Common control measures include the use of protective eyewear and face shields, protecting skin from exposure by covering it, and signs in areas where specific hazards are present. For some of the hazards, there may be a need for a person trained as a Radiation Safety Officer (RSO) with the use of this equipment. The equipment should include shielding as necessary to protect workers and have radiation detection instruments on the process equipment or in the immediate work area which will automatically shut down the equipment if radiation is detected. Some airborne particles may require the use of respiratory protection. Oxygen monitoring continuously should be conducted in areas using inert gases with an alarm when the oxygen gets below a specific safe level. The equipment will need to have procedures in place to control hazardous energy during maintenance or repairing, and machine guarding issues.
Chemical Hazards And Control Measures
The materials used in AM include polymers such as ABS, polycarbonate, polypropylene, silicone, nylon, and HDPE. Other materials include metals & alloys such as titanium, aluminum, Inconel, stainless steel, carbon steel, and ceramics such as silica/glass and porcelain. The materials come in, generally, four forms — liquid, powder, sheet, and wire depending upon the materials and the processes in which they are used.
As with any chemicals in the workplace, especially those that are listed as hazardous, the Safety Data Sheet (SDS) should be reviewed to understand the information needed to protect the worker. The SDS should be reviewed to understand information such as, yet not limited to, the specific hazards of the chemical, worker protective measures such as ventilation and/or personal protective equipment, the physical characteristics such as the auto-ignition temperature, and reactivity, proper storage, firefighting measures, and first-aid.
Some metal powders are designated as pyrophoric or combustible on their Safety Data Sheets. These are two of the main hazards of metal powders. Pyrophoric materials may ignite without any spark or ignition source and they may react violently when exposed to air. Special handling techniques should be used with pyrophoric materials such as using it in an inert environment in an enclosed box, glove box, or hood. Storage of pyrophoric material should include keeping it away from heat, flames, oxidizers and water sources, and keeping containers closed. Class D fire extinguishers or a specialty extinguishing foam should be readily available. There should be very specific procedures for handling, storing, and disposing of pyrophoric materials.
Combustible dust can be defined as a solid material composed of distinct particles or pieces, regardless of size, shape or chemical composition, which can present a fire hazard when suspended in air. For a dust explosion to occur, the dust must be combustible, be airborne, have a size distribution capable of flame propagation, the dust concentration must be within the explosive concentration range, an ignition source with high enough temperature must be present, and the atmosphere must contain sufficient oxygen to support and sustain combustion. To control the hazard of an explosion, control and eliminate the accumulation of combustible dust by inspecting for the presence of combustible dust, practice good housekeeping to eliminate the accumulation of dust, using explosion-proof dust collection systems and filters, use only approved electrical and wiring equipment and methods, and bond and ground equipment properly to control static electricity.
When working with or around any hazardous chemicals, safety glasses with side shields or chemical goggles and a face shield should be worn, and for the protection of skin, wear long sleeves and gloves. When working with pyrophoric or combustible powders, the worker should wear flame-resistant overgarment and flame-resistant gloves. Conducting an air monitoring assessment including for the particle size will aid in determining the need for and type of respirator that may need to be used — wither APR or supplied air.
Static electricity is a concern with the movement of the powders, the developing of friction, and the creation of static electricity that may, when discharged as a spark, may be enough of a source of heat to ignite a concentration of combustible dust and oxygen. To dissipate the static electricity the machines, tools, and equipment should be properly bonded together and grounded, static dissipative mats and/or static dissipative shoes are recommended for additional protection.
Storage of pyrophoric and/or combustible powders should be in flammables storage cabinets in the correct quantities when the materials are not being immediately used. The Safety Data Sheet will provide information on the proper storage of the materials.
This article was condensed from a White Paper prepared by Wayne Vanderhoof CSP of RJR Safety Inc. To get a copy of the White Paper titled “Additive Manufacturing Safety”, contact Wayne Vanderhoof.