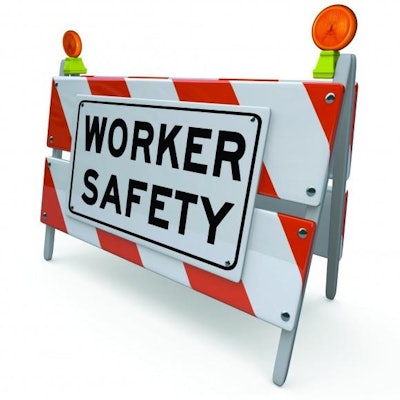
Here we have it. The OSHA Top 10 violations. The biggest list of the biggest citations given out in the past year. It seems that very little has changed from last year’s list.
And people may run the risk of not paying attention because it’s the same.
But that’s a risk you don’t want to take. So what are you supposed to do with it?
Well, when it comes to making sense of the OSHA Top 10, Grainger’s got your back. Below are insights from 10 Grainger safety professionals on the Top 10 and how they can help you keep your facility and your people safe as well as compliant.
(This is part two of a two part series. Read part one here.)
6) Hot Topics: Lockout/Tagout, Hazcom And Machine Guarding
By John Foston, Grainger Safety Regional Program Manager
People say that the OSHA Top 10 never changes. But that’s not necessarily true. If you look closely, you can see that certain areas do stand out from time to time. The Safety Record spoke with John Foston to find out why certain areas deserve more attention.
“Identifying the Top 10 violation isn’t difficult. It’s easy to walk into a facility and see a piece of equipment that’s in the ‘off’ position, and there’s no lock or tag on it,” says Foston. But that’s just the beginning. Organizations are not staying up-to-date with changes to the regulations, and OSHA knows this. “They walk into a facility and see Windex in plastic bottle with no label, and that could potentially lead to them investigating your program,” he says. And these are questions every safety manager has to be ready to answer. “Why isn’t this labeled? Let me see your written program. Let me see where you’ve trained your employees, etc.”
So every facility basically has this “low-hanging fruit” for OSHA inspectors. What can you do? John thinks it comes down to education. “Making certain that you’re in compliance. Whether that's bringing in a supplier to talk about a hazard communication program or understanding where you’ve got gaps and how to bridge those gaps.”
7) Compliance. It’s Not A One-Size-Fits-All Situation
By Michelle Star, Grainger Field Safety Specialist
Every organization is set up differently. That’s a given. And when it comes to safety, it’s important to have strong structure in place. In small organizations, safety may be handled by the head of Human Resources. In larger ones, there may be several employees in charge of safety programs. So how do you maximize success? According to Michelle Star, you fit the safety plan to the company structure.
“A lot of people feel very overwhelmed by this,” says Star. “Especially if they don’t have a safety person and it’s going through Risk Management or Human Resources.”
For those smaller facilities, “They look to you to guide them through their safety program, go through their SDS sheets, tell them what kind of products they need and help them with training employees. When you're dealing with HR and supervisors they don't have the time or the knowledge [to create a safety program]”. Michelle also sees the flip side of a large facility. “They’ll have an actual safety person that has a lot more knowledge of OSHA, PPE, etc.,” says Star. “But compliance is the minimum. There are still different ways to injure yourself. Just because you’re in compliance doesn’t mean you’re at the finish line.” Finding the correct safety programs that fit your organization is where you start. Where it goes from there depends on you.
8) The Lists Behind The List
By Richard Martin, Grainger Field Safety Specialist
When you look at the OSHA Top 10, the list can be overwhelming. But if you start to slice and dice the data, there are more important lists within the Top 10. And you begin to see the actions and areas that lead to worse accidents, the highest fines and, most importantly, how to prevent them. Richard Martin took us through them.
“Typically, when they create the list, what [OSHA] does is sort by the number of citations. Here's the top citations from this past year, and the list just runs in order of the most citations.” But Richard thinks there’s more to it. “There's several different parameters that you could re-sort the list by and end up with very different lists simply because of the parameters that you're sorting on,” he says. Martin cites Fall Protection as an example. “The top violation on the OSHA top-ten list of most cited standards is fall protection, but within that you've got fall prevention, fall restraint…it goes on and on.” And if you break down that area into more sub-categories, you can begin to see how complicated it can be. “The most common injury type is actually slips and trips. That's part of falls as well…we get a lot of broken bones and a lot of time out of the plant due to people just slipping on something wet or tipping over an uneven walking surface. Sometimes those injuries end up getting categorized into some other list, such as sprain or something else.”
And while priorities can vary from organization to organization, it takes time and expertise to figure out which list is important to your facility. Martin continues, “The number of citations may not be impactful for a particular organization. What may be the most impactful may be the number of fatalities and serious injuries or ... number of dollars in fines. Depending on where they're at in their safety program and what's important to them, the list being re-sorted might be more impactful.”
9) It’s All About Behavior
By Tim Reinke, Grainger Field Safety Specialist
One of the main factors keeping the OSHA Top 10 the same is behavior. People are doing the same things — climbing on scaffolding, working with certain chemicals and machinery. Tim Reinke, thinks it’s time we start thinking about behavior, trying to change it and being prepared when you can’t.
“They call it behavioral safety,” begins Reinke, “and it’s the largest struggle behind the OSHA Top 10.” Tim has visited hundreds of customers over the years and has seen it firsthand. “Sometimes you'll walk through a facility, and everyone is scrambling trying to find their glasses and their gloves and their respirators.” He believes that type of mentality comes from up top. “The high-ranking people in the building when they walk out the door don't have safety glasses or a hard hat on, and there are 25 signs that say you've got to have a hard hat, safety glasses, and steel-toe footwear, so it affects the perception of the employees. It's like, well if he's not going to wear it, then I shouldn't have to wear it.”
How do you change the “behaviorial safety” of your facility? Tim points to oil and gas refineries as the model. “Large O&G refineries make it real simple: You wear your specific PPE, follow procedures, policies and programs, training, stay in compliance or you don’t work there, period. That starts at the top of the organization and trickles down.” Taking the action is the key, according to Reinke. Getting upper managers to attend safety meetings and having them start talking to the employees about safety so they see the importance of the PPE they wear — and why it’s so important to keep them safe — so they go home the same way they came to work. “Make sure all managers and supervisors wear PPE to set the example,” he continues, “Remember, it’s a partnership and we are all on the same team to keep employees safe. They will see it and begin to change. Not an easy task but this will help begin the journey.”
10) Safety Starts With A Plan
By Frank Grasso, Grainger Safety Regional Program Manager
So what does this all mean? With all the complex issues that the OSHA Top 10 highlights, where do you start? Well, according to Frank Grasso the answer is simple: have a plan.
“I think the worst thing you can do is nothing,” says Grasso. "Don't put it off because it seems complicated, because you're not going to get anywhere with that kind of a plan," According to Grasso, too many companies sacrifice safety for budgetary reasons, and it’s not necessary. “It's not really expensive to have the right eye protection, hearing protection. Hand protection is a little more expensive; but an affordable solution can be found when you consult someone with the right knowledge. You find the things that involve money, because they require a capital budget expenditure, and they have to be planned for and submitted for approvals, which is why there's always a time delay. But in the meantime, there is something they can do. There are other ways to attack this and get the proper assessment and make sure your people are protected.”
Grasso recommends looking at what you can do right now, with the budget you have available, to get moving forward. “Talking with a safety specialist can open doors you thought might be closed to you. They may be able to show more cost-effective ways to maintain your existing safety program and free-up money for other compliance projects.”
This article was originally posted on Grainger's The Safety Record.