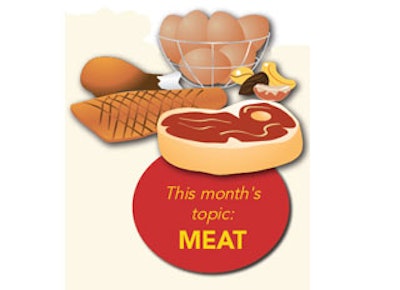
This article originally ran in the May 2013 issue of Food Manufacturing.
According to recent USDA figures, prices for most types of meat are higher year over year. Rising commodity costs due to drought and other inflationary factors are likely to drive these prices even higher in the months and year to come, representing a significant challenge against an economic backdrop of consumers still not back to confidence levels experienced prior to the Great Recession. Efficient operations at processing facilities are more critical than ever if meat product manufacturers are to remain profitable. Fortunately, advancements in packaging machinery and the potential for automation resulting from these innovations can play a pivotal role in enhancing efficiency for meat processing operations.
Evaluating packaging machinery for meat product manufacturers must begin with a discussion of Total Packaging Cost. At its most basic level, Total Packaging Cost incorporates all costs associated with the packaging of a given product, including packaging material costs (primary package material, labels, code dating, etc.), packaging equipment costs (purchase and lease costs, operator costs, maintenance and spare parts costs, utility costs, operations costs, etc.) and secondary packaging costs (palletizing, stretch wrapping, code dating, etc.) — all costs associated with taking a given product from a “ready to package” state to a “ready to ship” state.
New equipment, such as automatic bag loading systems or automated rotary chamber vacuum machines, can provide increased packaging speeds, better quality packages, reduced package rework and reduced labor. Additional advantages may also include less downtime for cleaning, maintenance and changeovers; improved troubleshooting capabilities; and effective use of data acquisition (to record critical packaging equipment details).
New and advanced equipment can also deliver the ability to automate much of the packaging process. Meat processors can incorporate technologies such as vision systems, robotics and next generation packaging equipment into their automated packaging lines in order to increase packaging consistency and reduce labor. Additionally, new software technologies enable processors to integrate multiple modules on a particular packaging line to increase the overall level of automation. Packaging equipment software also can be used to enhance system troubleshooting, provide remote access and perform data acquisition in order to further increase automation and productivity.
Meat processors have recently implemented systems that utilize vision components to accomplish specific tasks and ensure package quality. These systems can be used for identification and recognition of different types of product for improved production line routing or other efficiencies. Additionally, vision technology can be implemented in conjunction with other systems, such as robots.
While specific guidelines, accepted practices and standards for cleaning packaging equipment must be met, systems exist to streamline the process, monitor hygiene and ensure proper procedures are completed at necessary intervals. The specific procedures and cleaning substances to be used vary based on equipment, product and application. Packaging machinery solutions providers offering expertise in cleaning, hygiene and maintenance offer a concerted approach and can ensure that equipment design offers optimal efficiency for required cleaning and maintenance.
Despite other advantages, automated equipment can often be more complex, more expensive and require greater training or skills to properly operate and maintain. Automated equipment often is more electronic in design, with more complex electrical components and circuitry. These factors can result in reliability challenges when equipment is placed in less than harsh environments.
Other factors that warrant consideration are the upstream steps in meat production that occur before the introduction of automated packaging machinery, including buffering, orienting, accumulating and sorting of the product. In non-automated processes, these tasks are managed by humans. Designing systems that handle these complex situations effectively requires understanding and thorough evaluation of these upstream steps.
Opportunities abound to develop and implement machinery solutions that can enable automation-related efficiencies. However, there is no one-size-fits-all approach; a number of considerations exist based on the unique challenges of individual food manufacturing operations. These challenges must be addressed and mitigated, making it critical for meat processors to work with a packaging partner that understands the challenges of the industry and takes a total systems approach to develop the packaging and machinery solution that will best meet their needs.
During John King’s 26 years with Sealed Air, he has held various positions at the Packaging Equipment Systems Center including Project Manager for Furukawa Packaging Systems, QA Manager, Purchasing Manager, Manufacturing Engineering Manager, Marketing Manager and Director of Operations. He holds a degree in Electrical Engineering from Clemson University.