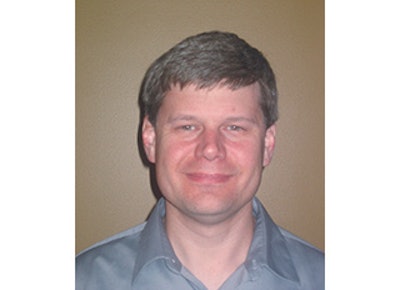
This article originally appeared in the March/April 2014 print issue of Food Manufacturing.
The Food Manufacturing Brainstorm features industry experts sharing their perspectives on issues critical to the overall food industry marketplace. In this issue, we ask: What types of plant automation should food manufacturers be looking at on a component level to most effectively streamline their operation?
For food processors to streamline day-to-day operations as efficiently as possible, it’s imperative that they have full visibility into the performance of their systems. While most processors may have a good feel for their production rates, fewer have a complete understanding of their system capacity and utilization metrics. As a result, these processors may be surprised to discover that their systems are performing at a fraction of their full potential.
Providing access to real-time and historical performance data helps plant operators maximize productivity and troubleshoot potential problems sooner. Some processors wait for external system audits to identify inefficiencies, when in reality they could evaluate deviations and adjust capacity levels and running rates immediately with detailed data monitoring tools. In-depth performance data also enables processors to mitigate labor needs down the line. For instance, one of the most prominent sources of processing inefficiency results from overrunning machines. While accelerating machines moves products along faster, it also increases the likelihood that products will be improperly placed or packaged, and will eventually need rework. Locating potentially overrunning machines earlier can save processors additional work later.
An effective data monitoring solution also can help processors eliminate machine downtime. Automated machines by nature are designed to run constantly, and with better planning, processors can maintain a steady product flow to keep the machines running rather than sitting idly between batches. Additionally, systems that are operating under capacity may still experience the same wear and tear as equipment performing at full capacity. By identifying these inefficiencies, services can help processors avoid maintenance issues that are premature when compared to product throughput or production levels.
Automation within a food processing plant will only be as effective as the insight operators have into their systems’ performance. It is advantageous to partner with a total solutions provider that can help operators understand how to acquire, review and react to critical performance statistics.
For more food industry news and information, subscribe here and follow us on Twitter, Facebook or LinkedIn.