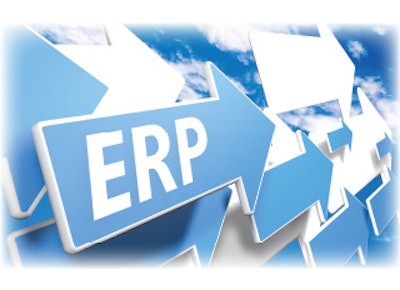
This article originally appeared in the March/April 2014 print issue of Food Manufacturing.
Food manufacturers can implement traceability programs to generate revenue as software becomes more integrated and user-friendly, said experts offering advice on how to choose those systems and put them into action.
Enterprise resource planning (ERP) has long been a mainstay in any business endeavor. Tracking resources and their use, as well as day-to-day business responsibilities, is a task considered by many as best completed by a software system. Putting a computer in charge cuts down on errors seen in manual paper tracking. Similarly, the traceability programs deemed increasingly vital in the global food system, due to regulation or customer demand, can be most accurately monitored and documented by software systems.
“Most requests we have now have an awful lot to do with regulatory compliance,” said Mike Edgett, director of industry marketing and process manufacturing at Infor. The company focuses on processing and manufacturing solutions including ERP and best-in-breed applications catered to user needs.
“If we can integrate [traceability capabilities] into something that helps the organization avoid cost or capture revenue, it really turns into a win-win for the organization and for the end consumer,” said Christian Hutter, senior vice president of food and beverage for Junction Solutions. The company is a single-source provider of vertical-specific applications and consulting services for food and beverage, among other industries. “We’re on the leading edge of how we turn regulation and traceability into a revenue-generation tool.”
ERP
ERP software offers visibility so manufacturers can make the most profitable decisions.
“If you can’t measure your yield appropriately and efficiently, you’re running blind,” Hutter said.
The myriad factors ERP software systems can manage include lot tracking, warehouse management, packing solutions, sales and customer management, materials requirements planning and bill of materials (BOM) management.
Some companies elect to operate with a piecemeal ERP system, implementing only the capabilities that they find most vital. However, experts said the benefits of a fully integrated system are plentiful, despite an often hefty initial investment.
“A lot of companies are working off of ERP systems that are old and outdated or ones they built themselves. As they continue to grow, they’re finding the systems aren’t really able to support what they need,” Edgett said. “The food and beverage industry is cursed in that it’s a low-margin business in most cases, so [manufacturers] are always looking for ways to peel a few more dollars out.”
“Data is king in analyzing business. It really allows you to push your company in new directions for growth,” said Jim Levy, senior account manager, ProVisions and Seasoft. Seasoft is customized for seafood processors and ProVisions is designed for meat processing and distribution, specialty food processing, and coffee and coffee products processing.
With the wide reach of software, from warehouse management, inventory tracking, production and expiration dates, software is essential to keep an operation running smoothly. “That’s very tedious work to do manually, and very simple with software,” Levy said
A topical example of the benefits of integrated ERP capabilities is evident in the current drought plaguing California produce processors, several experts noted.
When resources are tight, asset management, resource allocation and revenue optimization are more easily analyzed with seamless ERP. ERP software is vital for optimizing use of resources like energy and water. ERP can help manufacturers optimize to the point that they consider moving operations to a more cost-effective location, Edgett said.
One chief concern with ERP systems is communication between modules for accounting, warehousing and inventory, Levy said. Smaller and mid-sized food manufacturers are looking into moving away from disparate pieces of software. They can adopt more integrated approach to business, including warehouse management with barcode scanning capability, he said.
A seamless, paperless, real-time ERP system allows for schedule adherence and optimization. Shipping schedules are particularly important for manufacturers that work with third-party pickups, as well as those that man their own fleets, Hutter said.
Traceability
Traceability is essential for many food manufacturers striving to meet federal and international food safety standards. Plenty of processors are also working to comply with the growing list of third-party certifications demanded by grocery chains and consumers.
These certifications can open doors for manufacturers, as they’re nearly rule-of-thumb to sell to large chains, Levy said.
While traceability is often part of ERP systems, these capabilities are not always employed. But experts said that traceability is vital to keeping food safe and consumers confident.
“It’s not a question of if, it’s more of a question of when your organization is going to take part in of a recall,” Hutter said. This danger is more clear and present for produce manufacturers whose procedures don’t contain a kill-step, like pasteurization, he said.
End-to-end lot genealogy and a fully integrated supply chain is critical in maintaining food safety and consumer confidence, Hutter said.
“Safety is not just ability to trace the product, but it’s the ability to maintain customer confidence once you have a recall,” Hutter said.
Food processing software is turning the necessity of good traceability programs, typically for overhead projection or regulatory compliance, into a revenue-generating project.
New software can better connect the manufacturer of ingredients or products to the end consumer, even though the product may be combined with other products and sold to various retail chains.
Traceability measures can allow for control of the product from the field to the shipping dock. But when products are sold to other manufacturers, as with ingredients, or to various retail chains, manufacturers can lose sight of where the products go next, Hutter said.
“In the processor world, the most demand is for traceability with lot tracking. Most processors under $30 million in revenue continue to do this manually,” said Paul Hernandez-Cuebas, president, Integrated Management Solutions. The company’s Food Connex and Food Connex Cloud manages barcoding for traceability.
Though some software options allow some lot tracking with manual entry, they don’t validate what’s really happening. They simply augment the manual records, he said.
Implementation
Researching, purchasing and implementing food safety software is not an undertaking for the faint of heart. The effort involved can daunt food manufacturers. However, experts said it’s necessary to acquire a customized system that fits each company’s business needs. Differences in raw materials, end product, facilities and customers are just some of companies’ considerations for approaching the best type of manufacturing software.
“The solution they need within the portfolio is going to vary a lot, based on the size of the company and the business they’re in,” said Infor’s Edgett. For example, a glut of chicken wings is produced annually ahead of Super Bowl season.
Finding software that can expand with a company is fundamental to getting the right fit.
“[Manufacturers] want to think about where they want to be 10 years for now. Is the software going to allow them to grow?” Levy said.
Deciding on a firm to partner with can be just as crucial as software capabilities.
“Manufacturers are getting a lot smarter about how to implement these systems, which implies they’re starting to look more at the partner than the platform,” Hutter said. “The platform plays an important role… but really, what’s going to make you successful is the implementation partner: their size, their methodology and how they’ve dealt with customers in the past.”
Companies should plan for a year to investigate and implement software, Levy said. A process of converting data often follows once the new system is in place. For example, product codes have to be changed, customer lists cleaned out, and other general housekeeping, he said.
“There’s a learning curve. Some places might find out that they have to change their production process,” Levy said. “There are places that we sell to that have decided not to grind any beef because didn’t want to have to handle that traceability. But now that they have the capability, they end up processing it.”
Software Trends
User-friendly, integrated, mobile and cloud systems are top trends in food manufacturing software, experts said.
“A unified collaborative tool that goes across those systems really is important and helps facilitate understanding and minimize miscommunications. The chances for error are diminished and the chances toward response are increased," Edgett said.
Cross-company collaborative tools that allow, for example, employees in R&D and operations to work with procurement employees, enables real-time information sharing that gives every department the same information and ability to react.
In addition, experts said it behooves manufacturers to employ easy-to-use software that’s also accessible from mobile devices.
Seeking simple and intuitive, user-friendly interfaces can minimize training losses in a high-turnover environment like food manufacturing, Edgett said. Manufacturers are seeking consistency across software platforms and the ability to work with tablets.
In addition, cloud-based and software-as-a-service tools are popping up across the industry.
“Cloud based solutions are currently the rage in the market, but they do not remove the requirements of automating the shop floor,” Hernandez-Cuebas said. “It will be some time for these hybrid solutions, i.e. cloud and [on-] premise are effective.”
For more food industry news and information, subscribe here and follow us on Twitter, Facebook or LinkedIn.