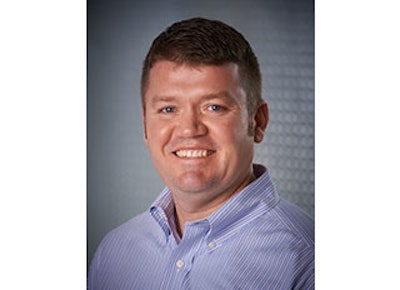
Loading docks are a busy and sometimes dangerous place. In most loading dock environments, you have semi-trucks pulling in and out of the approach, material handlers buzzing about and employees working around the dock. All of this activity can lead to accidents without the proper systems and procedures in place.
According to the Department of Labor and the Occupational Safety and Health Administration (OSHA), approximately 100 workers are killed and 95,000 injured every year while operating forklifts. Many of these accidents are related to turnovers or when a forklift operator drives off the dock.
Loading dock safety is just one of several issues facility managers must face. Other issues that must be addressed include theft prevention, environmental control and supply chain security, which are all critical issues for food manufacturers.
Greater safety, security and efficiency at the loading dock can be achieved when food companies incorporate a system of products and a detailed sequence of operations at the loading dock. The use of barrier systems, automated vehicle restraints, dock levelers, doors, shelters and lighted communication systems – working together – can help reduce the risk of accidents and injuries to workers, while improving security and supply chain integrity.
Interlocking vs. Interconnecting
For many companies, a loading dock safety strategy may encompass one or all of the following elements:
- Interlocking Systems — An interlocking system prevents the operation of equipment until certain conditions are met. For example, an automatic vehicle restraint would not release a trailer until a loading dock barrier is put in place.
- Interconnecting Systems — An interconnecting system allows a piece of equipment to operate only when another piece of equipment is activated first. An example is when a button is pushed to activate a dock leveler, then a vehicle restraint engages.
To determine which system is most ideal for your loading dock application, you must first address some important questions: What types of trailers are coming to your loading dock? What is the process for securing these trailers to ensure the safety of material handlers? What type of communication system is being used to alert drivers and workers of vehicle restraint status? When a truck departs, how is the loading dock opening secured?
Sequence of Operation
It’s important to break down your sequence of operation to fully understand your risks, while identifying areas for process improvements.
In a typical loading dock environment, the process starts when a truck driver is backing up in the approach. Communication is key at this point. The truck driver should see a green light indicating that it’s clear to back into the loading dock bay. Conversely, loading dock workers and material handlers should see a red light inside the facility alerting them that it’s unsafe to enter the trailer. Additional options include a barrier system covering the loading dock door until the truck is secured at the dock. Once the trailer has backed into the dock and is secured using a vehicle restraint, the lights inside the building change to green letting workers know that it’s safe to remove the barrier and enter the trailer. Outside, a red light tells the driver not to pull away. The process follows a similar pattern when a trailer leaves the loading dock.
Once you’ve broken down your sequence of operation, you can look at specific products and how they work together to improve safety, security and productivity. Here are some product categories to consider.
Vehicle Restraints
From low-tech wheel chocks to automated vehicle restraints, there are a variety of ways to secure a semi-trailer at your dock. An automatic vehicle restraint – which is often viewed as the most effective way to secure a trailer – can help prevent theft, reduce contamination and improve the safety of dock workers. An automatic restraint wraps around a trailer’s rear-impact guard (RIG), securing the trailer to the loading dock. There are also restraints designed to secure intermodal containers or trailers with RIG obstructions, which are becoming more commonplace at loading docks. Automated vehicle restraints help reduce trailer separation accidents and serve as a theft deterrent. In addition to improving safety and reducing damage to equipment, a tight connection reduces environmental contaminants from entering a building.
Some automatic restraints can be integrated into building management or security systems, providing another level of security and protection.
LightedCommunication Systems
Traditional vehicle restraint systems use a red or green light on the control box and outside the building to indicate restraint status. This is an important safety feature, but it has limitations. For example, what if the control box inside the building is not in the line of site of the forklift operator? What if the control box is covered by pallets? Fully integrated communication systems that provide instant, status-at-a-glance feedback are the safest solution. Look for a system that offers lights along the top of the door on the inside of the building as well as the dock leveler.
Barrier Systems
Full-time security at the loading dock often includes a removable barrier to guard the loading dock opening when a truck is not present. A dock barrier provides a visual cue that the loading dock is open but a truck is not present. If you plan on making a dock barrier part of your safety strategy, look for one that can withstand the weight of a moving, loaded forklift (consider 10,000 pounds as an upper limit). Also, look for a barrier that can interlock with a vehicle restraint, creating a sequence of operation that prohibits the barrier from being removed until a vehicle restraint is fully engaged.
Levelers
Once a trailer is secured at the loading dock, the next step is bridging the gap between the loading dock floor and the trailer bed. A vertical-storing dock leveler is considered the standard for maintaining cold chain integrity, environmental control and security. Unlike a pit-style leveler, a vertical leveler (when in the stored position) allows the loading dock door to close directly on the pit floor – rather than the leveler itself – reducing energy loss by minimizing outside air infiltration. In dry or cold storage applications, this tight seal helps reduce dust, debris, rodents and other contaminants from entering a building. It also reduces energy loss by controlling the exchange of air. A vertical dock leveler improves security by minimizing points of entry at the loading dock. Finally, the vertical design makes it easy to clean the pit floor when the leveler is in the upright and stored position.
When considering vertical dock levelers, look for a “drive through” application that allows dock workers to open trailer doors inside the facility. Opening and closing trailer doors inside, rather than on the drive approach, helps ensure cold chain integrity by minimizing outside air exchange into a cold environment. Equally as important, loading dock workers are placing or removing the seal from inside the building. This reduces the chance of theft or tampering. It’s important to look for a vertical leveler that provides the smoothest path between the facility floor and the trailer. This helps reduce “dock shock” to forklift operators, and damage to product and equipment
Seals and Shelters
A dock seal or shelter creates a barrier between the back end of the semi-trailer and the inside of the loading dock. This connection helps companies control their environment by keeping contaminants outside the building, while preventing the escape of valuable energy from inside the building. An effective dock sealing system also helps prevent weather-related product damage as they move in and out of a facility during manufacturing, processing and shipping. Seals and shelters can also provide deterrence against theft at the loading dock by sealing gaps that could otherwise be passageways for thieves. For maximum protection, equip all dock door openings with a system that closes the gaps that are created when a trailer is backed in for loading or unloading. This includes securing the tops, sides and bottoms of the openings when the trailer is in place. A four-sided seal is critically important.
Doors
Proper loading dock doors can increase safety and security while reducing energy consumption. If your company has a “closed door policy,” look for doors that incorporate translucent panels that allow sunlight in your loading dock area. These windows help increase visibility and safety, while reducing energy consumption. In addition, research doors that come with built-in ventilation systems. Vents will increase worker comfort without sacrificing loading dock security.
A Sytematic Approach
In most instances, a systematic approach that incorporates a variety of products and the proper sequence of operation is the best way to secure a loading dock. These products – working together as a system – enhance the safety and security of workers, while improving environmental control and supply chain integrity.
Schedule an assessment with a loading dock professional who can help analyze all aspects of a loading dock environment, including:
- Drive approach
- Loading dock dimensions
- Loading dock door configuration
- Building construction (Brick, metal, etc.)
- Weather conditions (Extreme heat, snow, etc.)
- Types of trailers (Semi-trailer with rear-impact guard, lift gates, intermodal containers, etc.)
- Weight and type of materials being loaded/unloaded
- Security and safety risks
- Environmental conditions inside the facility