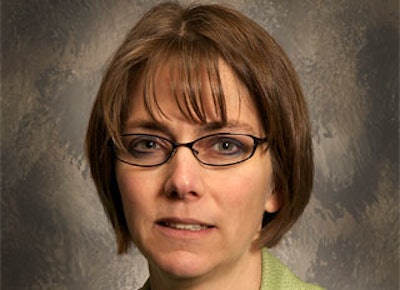
The Food Manufacturing Brainstorm features industry experts sharing their perspectives on issues critical to the overall food industry marketplace. In this issue, we ask: How can accurate instrumentation increase efficiency in food processing plants?
If more accurate information is provided from the sensor, the whole control system is better able to consistently provide the desired results with tighter specification in terms of product quality and cost optimization.
In a food application, one of the primary challenges users address is getting the right blend ratio of raw materials. Raw material supply can change, or cost pressure may require different ingredients to take advantage of changes in commodity pricing. A defined ratio of raw materials helps the end product taste right, and meet both nutritional and regulation requirements. When they are not mixed to the correct finished product specification, the product must be reworked or disposed of as waste. Automated blending technologies leverage a special algorithm based on the quantity of material being mixed and correlating it with the quality characteristics of both the raw material and finished product. This allows blending operations to utilize capital equipment more efficiently and reduce, or even eliminate, the need for intermediary vessels.
Feedback from smart instrumentation is the key to effectively monitoring raw materials. Process control sensors and actuators (devices measuring and controlling level, flow, temperature and other variables) provide seamless interconnectivity into critical business systems like MRP and LIMS.
There’s a growing need to capture more data, deliver it faster, perform additional diagnostics, access all device information remotely and leverage the data across the manufacturing enterprise. Many instruments now communicate using EtherNet/IP™ to help collect this information. With EtherNet/IP, which is based on standard unmodified Ethernet, users have easier and better access to real-time data, which improves the ability to monitor overall performance, troubleshoot out-of-margin conditions and minimize downtime.
Read Part I here.