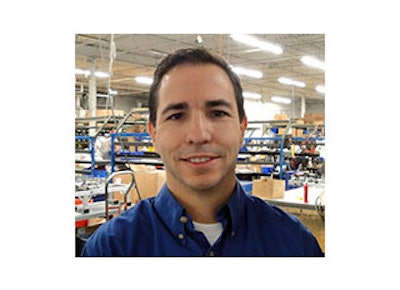
Out on the plant floor, workers often innovate on ways to get something done faster or more efficiently, and that's great, but sometimes, these shortcuts can run a company afoul of OSHA regulations. In operations where workers end up getting covered in dust or chips of some sort, they might turn a compressed air gun at themselves in order to clean themselves off quickly. The problem is that this can be exceptionally dangerous depending on the output pressure of the air line, and even whether the worker has an open cut on their skin. And even in more standard use of compressed air, there's many ways companies could accidentally create a dangerous or non-compliant situation. In order to get some insights into the nuances of what is safe and approved, our sister publication, Manufacturing.net, spoke with Mark Yorns, the director of engineering with Guardair Corporation.
Manufacturing.net: What is Guardair’s history with the compressed air regulations from the 1970s?
Mark Yorns: Guardair Corporation developed the first “safety air gun” in 1942. It incorporated a safety air shield to protect the operator from “chip fly-back.” This feature was patented, as were further technical innovations which followed. Occupational Safety and Health Administration (OSHA) was established by the US Department of Labor in 1970 to help tackle safety concerns in the workplace. In the early days of OSHA, Guardair worked closely with OSHA officials to craft the standards and consequently was in a unique position to introduce the first safety air gun designed to meet these newly minted regulations.
Manufacturing.net: Can you give a fairly simple overview as to what those regulations require/standardize?
Yorns: The three main regulations that apply to cleaning with compressed air are:
Output Pressure: Factory air lines normally operate between 80 psi and 120 psi. Most pneumatic tools, including air guns, need high pressures to operate effectively. OSHA requires that when an air gun is dead ended (the tip of an air gun is blocked), the static pressure at the point of blockage is no more than 30 psi.
Chip Guarding: Whenever blowing off debris with an air gun in close quarters, workers are subject to chip fly-back. This term refers to the tendency of loose particles or chips to fly back into the operator’s face, eyes or skin. For operations which require close-in work, OSHA requires that effective chip guarding be incorporated into the workplace.
Noise: Excessive noise generated in the workplace can be harmful. To address this problem, OSHA has developed permissible daily noise exposure specifications. Since safety air guns often contribute to high levels of occupational noise, the use of low-noise, safety air guns can be an important component in noise compliance.