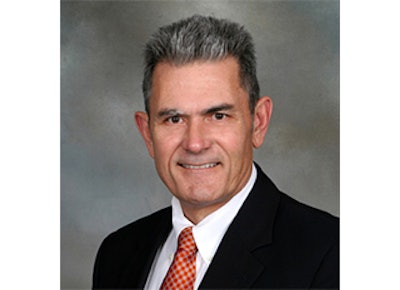
It is rare for a small to midsize manufacturing company today to not be utilizing an MRP/ERP system to conduct their business. System implementations may range from very aged, MS-DOS based systems to the most modern and sophisticated available. Regardless, these systems exist and can serve as the primary source for information used to efficiently execute, measure, and improve the business
Managers use performance data daily to operate and drive their business. Often such data is directly sourced from the MRP/ERP system in use. In some cases the use of this data is effective while in others it is not. When it is not, the MRP/ERP system is often designated as the root cause of the failure and, given the cost to replace such systems, it is concluded no action is possible and management works to construct other methods to work around the outcomes. It has been our experience that the base system is rarely the cause, rather, it is how the selected systems are implemented and used that cause the performance variation.
Common implementation causes for MRP/ERP systems to fail to adequately support management with suitable data have been experienced to be:
- Inaccurate Bill of Material (BOM) and manufacturing performance data input into the system resulting in erroneous measurement of performance. Inaccuracies in BOM data inputs result in improper relieving of material, inaccurate inventories, and often drive both the purchasing and scheduling activities outside of the system creating waste. Inaccurate input of manufacturing data, to include manning and production cycle times, results job to job variation in machine and labor efficiencies. Such false readings drive unnecessary analysis to understand the data and frustrate management to the extent that some may disregard the data, finding other methods to attempt to measure and understand performance. Again waste is being created.
- Variation in the Bill of Material and manufacturing performance data from module to module resulting in variation in measured performance between areas. In our experience, data fidelity between MRP/ERP modules is not always 100%. When data is used from the different modules results vary and managers enter into exploration of which outcome is correct. Often, the issue is recognized and not corrected leading to repeat efforts at a future date compounding the waste generated. Time spent reconciling data is time unavailable for managing business outcomes.
Common usage failures causing management to be less than effective in using MRP/ERP sources performance data have been, by our experience, know to include:
- The failure to adequately maintain and use performance data, recognizing a time dependence of performance, in the form of trend or run charts. In our experience we commonly observe management teams examining prior day performance and comparing it by memory to how the same metric has performed in their memory, typically over the last week or several days. Missing is the accurate, data driven analysis of performance over time. Is it trending up, down or flat? More often than not, when system generated performance data is, for the first time, looked at objectively over time performance is either declining, or, more likely, is flat.
- The failure to adequately use resident data for purpose of analysis and driving actionable improvement activities. Generally when observing companies we find that performance data required to prioritize and drive improvement activity is resident within the MRP/ERP system. It is consistently surprising to learn that management is not informed that this data can be accessed and as a result is not being used. It is rare that scrap and equipment downtime data, often with reason codes, are not captured and recorded in the MRP/ERP system. What is fairly common however is the lack of a systematic way to access the data for analysis. In the absence of these methods, critical data is unused and actions taken may be based on opinion.
What separates those using data effectively from those not is centered in how the above causes are treated. It revolves around management approach, not software sophistication. Characteristic behaviors experienced with teams that succeed include:
- An absolute dedication and commitment to rely upon the tools at hand and make these tools work to their benefit. There is no acceptance of BOM or manufacturing performance data inaccuracy. Such inaccuracies may have originated at system implementation but, more likely, have developed with changes to the product or process. Corresponding data entries may not have been updated within the MRP/ERP system in a timely and disciplined fashion. Regardless of origin, a focus on identifying and eliminating inaccuracies must be initiated. This would include ensuring that data is consistent between modules and all modules are updated as required. To maintain system integrity and usability management places high priority on and dedicates suitable resources to ensuring accurate and consistent data entry.
- A resolute direction to use resident data for understanding performance over time while developing and prioritizing action items, from this data, aimed at creating improved performance. Depending on age and sophistication, not all MRP/ERP systems will easily allow internal data manipulation for the purpose of analysis. Further, system defined reports may not provide information for examining metric trends. Rather than this being a reason for inaction, a majority of systems will allow for the export of data into a data file. Such a file can subsequently be used to populate any spreadsheet application. Once in that format creation of trend and pare to data can proceed and be available for management review and action. Obviously, when such data handling is required, creation of standard work to ensure consistency over time of the results is required.
With the above direction, daily and weekly accountability sessions are performance focused in nature. The is little or no time wasted questioning the results and full attention is paid to problem solving, action item definition, and measuring results for confirmation of impact and sustaining performance. Should an inaccuracy in data be identified, management in response to such definition places high priority on timely correction to ensure there is no on-going waste associated with the inaccuracy. While this may seem like a cost increase to performing the business, recall that doing so eliminates management waste and facilitates the real automated capabilities of that the systems were designed to provide eliminating the inefficiencies involved with manual processes.
Through our experience we have found most MRP/ERP systems can be employed to facilitate successful management and improvement of company outcomes. Some systems may be easier than others to work with but the systems are largely found to be capable. The next time you are informed that the data is not available, is not accurate, cannot be accessed, have another look at how well the management really understands their business.
About Douglas Olander, Managing Director, BBK
Doug has more than 25 years of experience in large-scale manufacturing and/or multi-site management. He has a proven ability to improve processes and achieve results. An expert in performance improvement, Doug’s specialties include lean manufacturing, quality operating system assessment/support, problem analysis and problem solving. His expertise in operations intervention includes manufacturing transition, launch readiness, engineering/operations support and interim management. Specific process experience includes stamping, metal fabrication, plastic molding, machining, and assembly processes.