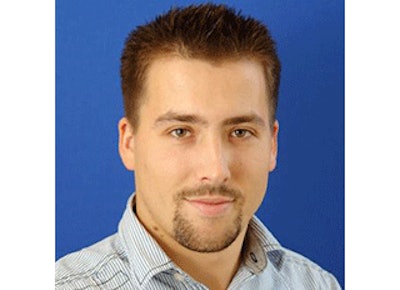
Where quality and efficiency are concerned, innovations in the food industry generally result in new complexity for engineers. But every once in a while, new technology comes along that has the potential to remove multiple components from the production line, saving time and money, boosting quality and simplifying processes.
Hygienic twin-screw pumps, which can convey liquids as well as suspensions (two phases like fruit particles within a juice) thanks to their contact-free intermeshing screws, represent an area where this confluence of opportunities is yielding dramatic results for manufacturers in a large portion of the food industry.
Pump system-based food conveyance has come a long way. The cost dynamics around pump-based applications are shifting rapidly. As standards regulation has increased and technology that’s worked in other industries for years has arrived to sanitary applications, investment in advanced pumps, valves and other systems components has become easily justifiable in many cases.
Defining a New Class of Pumps Through 2-in-1 Functionality
Remember when you first saw HD television? The fact that it was revolutionary enough to warrant its own new category was immediate obvious. This is exactly what twin-screw pumps have done by entering the market for hygienic pumps. For years, manufacturers have described the last generation of hygienic pumps as “clean-in-place-able,” because they marked a sea change in sanitation convenience. Plant managers no longer had to disassemble these pumps—positive displacement process pumps and the subsystems fed by them could be washed by separate clean-in-place (CIP) pumps, which are typically centrifugal pumps that are not able to move high viscous products. Today, a single twin-screw pump can fill the role of positive displacement process pump and centrifugal CIP pump in systems with a wide range pipe diameters and sanitation challenges. Twin-screw pumps aren’t just clean-in-place-able. They’re truly self-cleaning and they generate the required CIP flowrates.
This is because the highly engineered hygienic twin-screw pump can move fluids under an incredibly wide range of constraints while also being able to operate at high velocities. They offer a 2-in-1 solution, delivering the benefits of both positive displacement pumps and centrifugal pumps. Like positive displacement pumps, at low RPMs they offer low turbulence and ability to pump highly viscous fluids (1 to 500,000 cP) and fluids with diverse viscosity compositions, including fluids with entrained air. They can even run completely dry for extended periods of time when seal quench is maintained—enabling manufacturers to suck the last drops of liquid out of containers or move solid foods like whole strawberries.
Like centrifugal pumps, they can operate at high RPMs and generate enough force and flow to flush systems quickly. At these high velocities, they also create enough turbulence to scrub themselves clean, since their mechanical feeds sit directly in the pumping chamber and are completely flooded by the fluids being pumped. There are no dead ends where food residue can build up. Typical cleaning scenarios require flow velocities of 1,5 to 2,5 m/s which requires often pump speeds of 1,500 to 2,000 RPMs. As the requirements are also rising here, flow velocities up to 3,5 m/s are sometimes required but well-made twin-screw pumps can operate safely up to 3,600 RPMs under the right system conditions.
Unparalleled Total Cost of Ownership Through 2-Part Efficiency
By investing in twin-screw technology, plant managers can buy one pump instead of two, leaving CIP pump piping, valves and other components out of the system and saving valuable room on the floor. Instead of wasting time on complex cleaning processes that could otherwise be spent manufacturing, engineers can clean systems with the twin-screw pumps that are already in place, meaning improved uptimes. But that’s not the end of the uptime efficiency that twin-screw pumps offer.
Twin-screw pumps involve zero metal-to-metal contact thanks to an internal timing system, so they’re much less susceptible to wear and tear than some other positive displacement pumps types. This is the second source of efficiency and decreased downtime that hygienic twin-screw pumps offer.
Maintaining Quality and Sanitation
In scenarios where maintaining quality and sanitation are paramount, hygienic twin-screw pumps offer a few benefits compared to well-known and often used PC Pumps (Progressive Cavity) in areas where the PC pump was the only suitable pump (high suction power required or gentle handling of sensitive products). First the food particles are not exposed to rubber components. Also, the twin-screw technology delivers low shear so easily damaged particles in both large and small sizes are handled properly and kept intact. Finally, there is no centrifuge, thereby reducing the separation among nonhomogeneous fluids. These pumps move fluids in a straight line. The low turbulence and very low pulsation even with a pressure increase is possible due to a multi-chamber design which reduces frothing and agitation and increased the suction power of the Twin Screw pump up to the physical limits.
Hygienic Twin Screw Applications in Food Manufacturing
Hygienic twin screw pumps can handle a variety of high viscous products. Diced tomatoes that need to be delicately handled without being damaged, meat products like sausage preparation, yogurt processing, or fish paste in sushi production are all examples that can be adeptly handled by twin screw pumping technology.
Sanitation and proper product handling are equally important to food manufacturers. One example is a large North American tomato processor who was using rotary lube pumps for conveying and they were having reliability issues before the end of the production cycle. Tomatoes can be abrasive to a pumping system causing considerable wear, pump failures and unplanned downtime. This processor eventually switched to hygienic twin screw sanitary pump to handle tomato concentrate. After pumping tomato paste for five straight months over the course of the tomato harvest season, the pumping system showed no signs of wear. This included the seals that were exposed to the abrasive materials. The processor realized less plant downtime and higher productivity through their season of peak activity thanks to the twin screw technology.
A Superior Solution
The hygienic twin screw pump is a breakthrough technology available to food manufacturers that can increase reliability, reduce plant downtime and adeptly pump a wide range of viscous food products. The 2-in-1 systems offer a high level of sanitation with a real clean in place functionality. Furthermore the pumping systems are flexible enough to handle a variety of solid, liquid and even gas mixtures at a wide range of speeds and still gently maintain the appropriate pressure to handle a variety of foods. As technology continues to advance manufacturers can benefit from the increased efficiencies and capabilities related to the hygienic twin screw pumping technology.