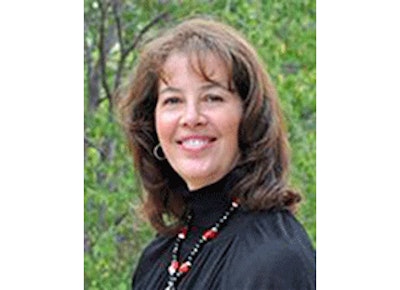
Workforce training is not all it should be in the food processing and manufacturing industries. According to the recently released 2014 Global Food Safety Training Survey, training tends to come up short due to the unavailability of two necessary resources—time and money. Such limitations increase risk for the company, its workers and, in particular, consumers.
Survey responses attribute the lack of time for training and refresher courses to meeting production workload requirements in a time of lean operational staffing.
There has to be assurance that the concepts taught will be practiced long after classroom training has ended. Thanks to technology, that wish has become a reality. An app on a tablet has been developed to enable supervisors to act as coaches in real-time on the plant floor. The idea is to positively influence behavior. Based upon the survey conclusions, behavioral influence is essential for continuous food and workplace safety.
What the survey revealed about behavior
Campden BRI, U.K., developed the 2014 survey in association with Alchemy Systems and several other partners: BRC Global Standards, the SQF Institute and SGS, Geneva. The survey probed a wide variety of training topics; e.g. time for training, measurement metrics of training success, audit deficiencies, challenges and goals. It was distributed to 25,000 meat, dairy, fish, produce, spices and bakery companies worldwide. The survey’s goal was to enable companies to benchmark their training against similar sized companies globally especially in these areas:
- Employee ability to read and understand policies
- On-the-job training
- Refresher courses
- Onboarding
- On-site classroom training
It should not be surprising that an overwhelming number of respondents named establishment of a food safety culture as the most important training goal. How to get there is another matter. More than 75 percent identified time and resources as their biggest challenge for conducting effective new and refresher course training. Another surprising finding was the inability of many recipients to quantify the training budget allocated for food safety training.
The survey is also revealing for how its respondents measure training’s value. Three most common standards of measurement are product quality, product safety and employee performance/behavior. Nearly 80 percent list improved food safety culture as a benefit of training but in a seeming contradiction, only 45 percent identify achieving the culture as a standard of measurement. At the same time, such areas as product quality, fewer food safety incidents and reduction of complaints—all factors for successful risk mitigation—are named as training benefits. The downside: a large majority of respondents could only pronounce themselves “somewhat satisfied” with the quality and quantity of training.
One need not be versed in risk management to appreciate the exposure created by these training issues. The newly developed tablet-based coaching app has been designed to address those risks while keeping food safety front and center on the minds of all employees.
Coaching in real-time
While few question the value of coaching on-the-job to verify food safety behaviors, perhaps some might be somewhat reluctant to launch a wholesale employee behavior assessment program because they see it as time consuming and paper-intensive. Notations, written by hand, would have to be entered into data in each employee’s file. So would corrective actions, a procedure requiring extensive amounts of time that could be put to better use elsewhere. Survey responses show a growing recognition of the value of supervisory coaching, but there remains a question whether supervisors possess the skills required of an effective coach. Supervisors generally receive little formal training in either effective communication and motivation skills or problem-solving.
The new technology addresses this issue by providing behavioral coaching guidelines applicable for each process in food manufacturing. The templates are not generic. They can be customized for coaching at each step of the process. The app is also proving effective for instilling and enforcing GMPs and behavioral standards. Every step to influence the right behavior is extensively detailed enabling two outcomes: (1) supervisors develop into more effective coaches and (2) employees become more conscious of food and workplace safety at every step of the process.
Data entered with the app measures performance behavior and helps improve productivity and safety while reducing potential risk. Observation data is electronically entered into employee files from the app, which eliminates manual data entry and excessive paperwork. Users have already reported positive results.
“We have saved time capturing data needed for audits and training records,” said Jennifer Vanzego, training specialist for Lactalis American Group, a global dairy products company. “We look forward to seeing a definitive change of behaviors on the floor.”
A second look
Time and training costs may still be perceived by some companies as revenue drains. The truth is just the opposite. Based on the responses to the Global Food Safety Training Survey, more companies worldwide are turning to coaching because of the growing recognition of the benefits of influencing behavior on a daily basis—behavior that can now be measured and recorded instantaneously in personnel files with the ease of the touch on a tablet.
There is no reason for companies to place themselves at risk for audit deficiencies, workplace accidents, and incidents of contamination and recalls. It is time to take a second look at the ROI of employee coaching as a necessary component of a comprehensive food safety training program for mitigating risk. Such training can optimize production by improving safety awareness, reducing customer complaints and the possibility of recalls, and elevating the performance of all employees to improve operational efficiencies. All are part and parcel of a true food safety culture.
About the Author
Laura Dunn Nelson is industrial relations director for Alchemy Systems, Austin, Texas. Alchemy is the global leader of innovative technologies and services designed to align employee behavior with a company’s quality and safety commitments. Tel: 888-988-1832 or visit our website: www.alchemysystems.com