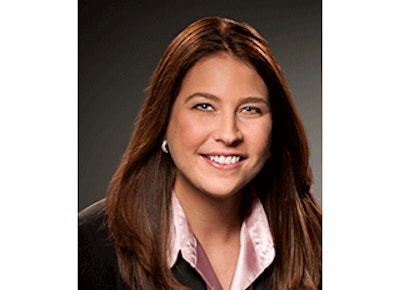
Collaboration among trading partners represents a tremendous opportunity for business and industry that cannot be underestimated. While food manufacturers large and small may have diverging business interests, working together with their trading partners to agree upon standards can make the supply chain operations more efficient, less complex and less costly.
Food Manufacturing recently interviewed Angela Fernandez, vice president of retail grocery and foodservice at GS1 US, a non-profit standards organization that facilitates industry collaboration through formal industry initiatives and connects stakeholder communities through education and support, on the importance of collaboration through the use of global standards in the food industry.
Q: How important is it that manufacturers collaborate with retailers and other trading partners to enhance supply chain success?
A: A couple of years ago, a study by the Boston Consulting Group and the Grocery Manufacturers Association sought to quantify the value of business-to-business collaboration. It found that collaboration is a major source of untapped value in the food industry, worth up to $21 billion industrywide.
The reality is that today, there are so many challenges and market forces impacting the retail grocery industry—many more than 40 years ago when the barcode was first born. Food safety, data accuracy and product information are topics that continue to be top of mind in the industry. By collaborating more with their trading partners, food manufacturers can more readily identify emerging industry challenges, develop a standards-based approach to solve for the problem and create best practices to address those key issues.
In our experiences working with all industry stakeholders under two industry initiatives (one in the retail grocery industry and one in foodservice), we see that companies are able to accomplish more working on a few common challenges, as opposed to focusing on multiple projects that might impact only a small community within the industry. Participating in one of these initiatives means taking advantage of one of the few opportunities available where all industry stakeholders from various supply chain roles come to a consensus on what we need to work on, and how to accomplish those goals in a way that best benefits all. Because our initiative discussions involve participants from all supply chain stakeholders , there is, most often, a compromise for the value of the benefits achieved by each participant, but they always keep the usefulness for the industry in mind.
Q: What are the top issues driving the need for best practices and standards development?
A: Today, consumers have high expectations and are more informed than ever due to the everyday use of a smartphone to look up prices, ingredients, nutrition facts and allergens. At a recent meeting of our new GS1 US Retail Grocery Initiative, two of the top themes that recurred throughout the discussion were the need for alignment on product information for business and consumer use, as well as the standardized usage of product images. These can be key differentiators for a business and can enhance the overall customer experience. Both of these issues tie closely with the needs, demands and expectations of the hyper-connected grocery shopper scanning barcodes with her phone at the store, and the movement toward improved e-commerce, particularly among the Millennial generation.
Regulations such as the Food Safety and Modernization Act (FSMA) are also driving forward the need to enhance supply chain visibility. Many industry stakeholders we work with are placing a greater emphasis on supply chain visibility using GS1 Standards not just because they anticipate future FDA regulations will require them to have better traceability capabilities, but because they know they’ll gain additional business benefits when they can better see the details of their internal processes as well as where the product originated from or the point of consumption. GS1 Standards enable companies to globally uniquely identify products in the supply chain in order to optimize visibility and efficiency. Using GS1 identification numbers, including the Global Trade Item Number (GTIN), companies around the world can identify trade items as well as supplementary information, (expiration date, serial number, batch/lot number) to facilitate the communication of product-specific information wherever a barcode is scanned. Organizations that have full visibility based on these standards ultimately gain the ability to protect their brands and company image by knowing the exact attributes and location of each product.
Q: What are some internal benefits to be gained from operating standards-based business processes?
A: Internally, the concepts of visibility based on standards provide many benefits. With visibility into their supply chains, companies achieve more operational efficiencies and process improvements, such as better inventory/category management, more accurate ordering, improved product availability, improved shrink management and, ultimately, efficient and accurate traceability when required.
Recently, food manufacturers participating in our initiatives are focusing on reducing supply chain inefficiencies from decreasing total delivery costs (TDCs) in order to remain competitive and successful. We are currently identifying the gaps and opportunities for operational efficiencies where leveraging GS1 Standards can lead to positive results. For example, the initiative could soon develop industry guidance to address the inefficiency of using multiple barcodes by providing education on the proper use and selection of barcodes for specific business applications. Instituting this best practice could mean major savings for manufacturers and their trading partners.
Q: What are some immediate results manufacturers will see once they collaborate more with their trading partners?
A: Manufacturers are the experts when it comes to their products. They should have a voice in how standards are adopted and used by industry and help develop guidelines and resources that benefit all trading partners in the supply chain. In addition to joining a work group or a food industry association to learn from your peers, adopting standards can help manufacturers overcome the limitations of using proprietary solutions and systems, and make trading more efficient and responsive to customers on a global scale.
How is that achieved? The answer is through improved supply chain visibility. The need for improved supply chain visibility is becoming more critical to ensuring the delivery and tracking of safe foods not only to comply with emerging regulations, but also to enable rapid and precise responses to product withdrawal and recalls. We’re working on aligning a common approach to uniquely identifying and tracking products as they move throughout the food supply chain. This means driving broader awareness of the benefits of a standards-based system and working to improve key business operations overall to enable that visibility that is so critical as the marketplace evolves.
Basically, manufacturers as well as consumers want to know “where did my product come from?” and “where did my product go?” Traceability is enhanced with the use of standards to help answer both questions. It takes the collaboration of manufacturers, distributors, retailers, as well as solution providers offering scalable solutions to ensure the technology supports the industry requirements, to fully implement these best practices.
Angela Fernandez, Vice President of Retail Grocery and Foodservice, GS1 US