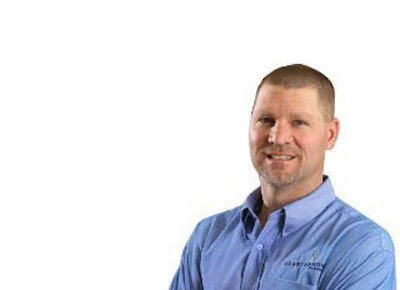
Austin Packaging Company (APC), a Minnesota-based USDA contract manufacturer for some of the world’s largest food companies, is known for the speed and quality of its prepared foods product development and production capabilities. Manufacturing and packaging more than 125 shelf-stable, refrigerated and frozen products, APC provides unique services that allow food manufacturers to quickly test and bring new products to market and to manufacture and sell smaller volume products more economically than could be done in-house.
Business Challenges: All Things Point to Volatility
The kind of flexibility and speed-to-market capabilities APC offers bring some difficult challenges. At the heart of these challenges is the inherent volatility that comes with unpredictable and seasonal production demands. The fluctuation in production runs in turn translates into frequent and sometimes extreme fluctuations in APC’s demand for labor. A change in production schedules can mean one day requires 150 workers, and the next day the demand calls for 300. These common yet often times unpredictable demand spikes make it very difficult to have a trained pool of workers at the ready.
Keeping skills current and employees cross-trained is important to the success of APC, yet having to use temporary labor to backfill jobs during production ramp up makes this difficult. After a number of weeks working elsewhere, temporary employees returning to APC need to be re-trained. Planning and scheduling with this amount of variability in staff and skills tend to create unpredictable schedules, which can, in turn cause high turnover within both the core and the temporary workforce. Reducing staff turnover has become a key focus for APC because having a well-trained, available workforce is critical when ramp up is necessary.
Business Drivers: Why Scheduling?
Prior to implementing ScheduleSoft, APC used spreadsheets and what it refers to as “tribal knowledge” to create schedules. Supervisors would attempt to accommodate employee needs for various shifts or jobs rather than scheduling based on the business demand. While it has come to expect a certain level of demand volatility, APC has not yet been able to consistently match labor to production requirements. In order to grow the business and maintain their reputation of flexibility, speed and quality, APC needed to find a way to effectively leverage its workforce. After looking at various solutions, APC selected ScheduleSoft.
The Benefits of Automated Scheduling
APC has completed implementation of ScheduleSoft and expects to be able to more consistently match labor staffing to production demands. The company is confident it now has rules configured into the application that will help create a fair, consistent and more predictable schedule.
Using ScheduleSoft, APC will now be able to:
- More easily match labor to production requirements
- Provide more predictability for all employees
- Provide its core staff with a more consistent 40 hour/week schedule
- Schedule fairly and consistently
- Increase productivity from supervisors who had previously had to manage all the scheduling manually
As the company begins to work with the system and learn what it can do and how it can be leveraged, APC is considering additional areas of automation. Moving forward, the company plans to keep a more detailed skills matrix which would help it better staff certain positions and be able to leverage the cross-training that is important for providing employees more job opportunities. APC plans to further stratify the skill sets required for all positions, including general labor jobs, which will help it gain further productivity by staffing the best talent. APC also plans to integrate ScheduleSoft with its ERP and financial systems to be able to share information and more effectively run the business. In addition, APC plans to utilize ScheduleSoft Workforce Access™ which will give employees direct access for viewing schedules, requesting time off, bidding for jobs and volunteering for overtime.
Best Practices
Implementing any system that gets at the core of a manufacturer’s operations necessitates looking at critical business practices and processes. Chris Shimek, APC’s COO has these recommendations for other companies considering automated workforce scheduling:
- The project should be led from an operations point of view rather than an HR or IT to ensure that schedules are designed to meet the objectives of the business.
- Any project that gets at the core of operations will cause some level of disruption. Anticipate and prepare for some cultural change, but know your actions will drive longer term business results.
- The tools are only as good as the information we feed them and no software provider can be expected to know our business well enough to determine the right drivers. We own that and should expect to continue to uncover ways to further leverage the system’s capabilities.