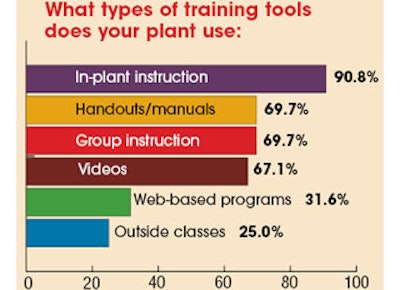
This article originally ran in the November/December 2012 issue of Food Manufacturing.
The Food Safety Update section of Food Manufacturing is designed to offer our readers insight into the state of food safety concerns across the industry. We received hundreds of responses to this month’s survey on employee training.
Proper employee training is vital in maintaining adequate food safety standards throughout a food manufacturing facility. A plant is only as safe as its least-safe employee, and the quality of final products produced in a plant depend on the diligence of the workers employed there.
When we surveyed readers this month to find out about the effectiveness of their employee training plans, we found that many readers struggle to keep their employees up to speed and engaged. As seen in the chart below, food manufacturers report a wide variety of obstacles to proper plant floor training. Of the readers who selected “other,” over half noted a failure of training programs, materials or software to adequately address the training needs of their plant.
When asked about the correlation between more training and plant improvement, Food Manufacturing readers reported seeing:
- Fewer mistakes, better product quality—38.6%
- Better food safety—34.7%
- Fewer worker injuries—22.6%
- Higher employee morale—16.0%
- Lower turnover—14.6%
- Higher efficiency—12.4%
These results indicate that manufacturers are noticing a variety of benefits from increased training regimens, but they are, as indicated above, having a difficult time finding adequate time to perform these beneficial training sessions. In an effort to utilize the time at hand, food manufacturers report relying on a variety of training methods, as noted in the chart above.
In addition to varied training methods, the topics covered by training vary as well. Readers reported that, in addition to food safety training, workers in their facilities receive training in the following areas:
- Mandated workplace training (ie sexual harassment, workplace violence)—76.3%
- Equipment-specific training—88.2%
- Industrial safety (fire and electrical compliance, personal protective equipment)—82.9%
- Compliance training (government regulations)—72.4%
- Maintenance procedures—63.2%
- Company background/mission—51.3%
Though 69.3 percent of readers report involving plant-floor employees in food safety and HACCP plans, when it comes to food safety training, readers report that lack of time is their biggest challenge (46.1 percent). Despite the time crunch, manufacturers are working training into the daily routine. When asked about the average length of time spent on employee training, readers reported:
- Training is ongoing—59.2%
- Two to three weeks—18.4%
- One week—11.8%
- A few days—10.5%
So while processors are facing many challenges in keeping employees up to speed with proper training — in food safety as well as a variety of other areas — Food Manufacturing readers are working to do so with the resources available to them.